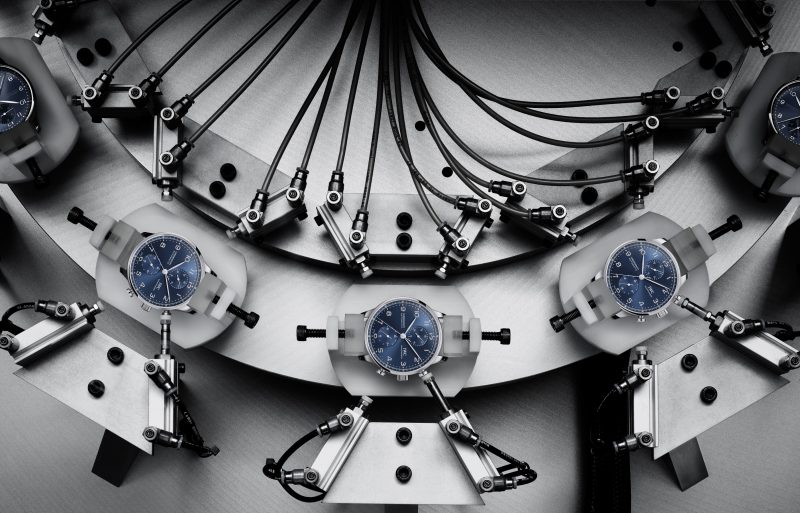
The Journal
IWC CHRONOGRAPHS: PRECISION. ROBUSTNESS. RELIABILITY.
Shipping and delivery conditions
WATCHMAKER AND ASSOCIATE DIRECTOR MARKUS BÜHLER DETAILS CHRONOGRAPH ASSEMBLY AND QUALITY CONTROL FOR THE 69000-CALIBRE LINE
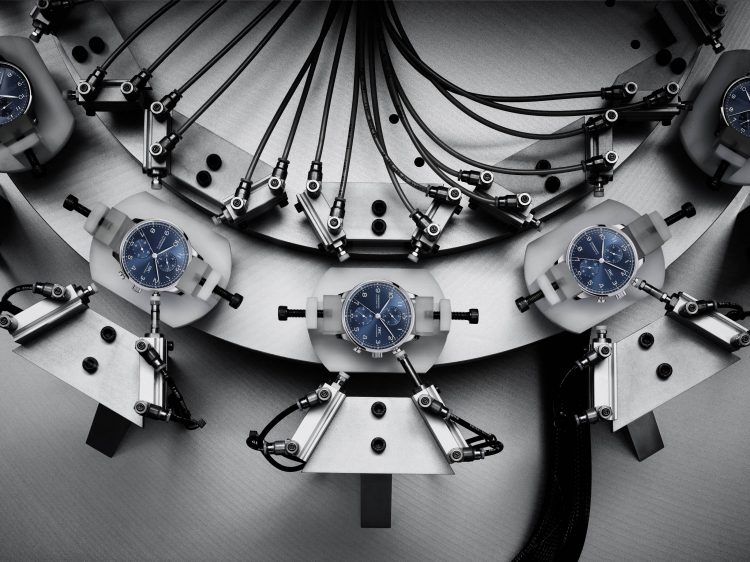
Markus Bühler is responsible for the assembly line and quality control of the 69000-calibre family at IWC’s manufacturing centre.
Here, he explains what is important when assembling a chronograph and how perfect quality is achieved on the assembly line.
— Associate Director Watch & Movement Assembly, Markus Bühler
UNDER PRESSURE
WHAT ARE THE MAIN CHALLENGES YOU FACE WHEN ASSEMBLING A CHRONOGRAPH?
As with any other additional function, we must finetune the interaction between the chronograph and the basic movement to perfection. This is so important because of the extreme stresses the components undergo when the chronograph is in use. It takes a force of 10.33 Newtons to activate the push-buttons, for example, and the hands race back to their initial position at 77 kilometres per hour. The amount of energy required by this complication also poses a challenge because the basic movement’s rate must remain constant even when the chronograph is in use.
WHAT SETS THE IWC-MANUFACTURED 69000 CALIBRE APART?
With the 69000-calibre family, we wanted to develop one of the most stable and reliable chronographs ever. We made no compromises in streamlining the overall calibre for efficient energy use and maximum robustness. In addition, we used newly developed lubricants and carefully matched material pairings in the interest of durability.
The smaller each step in the process, the better you can control the quality
GOOD VIBRATIONS
WHAT HAPPENED DURING THE TYPE TESTING OF THE 69000 CALIBRE?
As part of the type testing process, we put the movement with all its sub-assemblies through its paces and simulate ten years of wear and tear. Among other things, we turn the rotor several million times or check the workings of the chronograph over thousands of cycles. To finish off, we put the balance and escapement through a series of strenuous tests. In an accelerated wear test, we carry 2.5 billion vibrations.
HOW IS ASSEMBLY ORGANIZED IN THE MANUFACTURING CENTRE?
The assembly of the 69000-calibre family is organized in a line and divided into several smaller steps. Our main reason for this approach is quality. The smaller each step in the process, the better you can control the quality. We exploit this simple fact to achieve the best possible quality of the movement at every stage of the process.
— Assembly of the column wheel in the chronograph caliber 69000
THOROUGH TESTING REGIMEN
HOW DOES INTEGRATED QUALITY ASSURANCE WORK?
We have a three-tiered, seamlessly integrated quality concept. Firstly, the watchmaker controls the quality after every step. Then the line manager takes random samples to check that the controls have been carried out correctly.
The third stage is something we developed in-house, which we call the Final Inspection Movement (FIM) cell. Over twelve days, we test all the relevant movement functions automatically. Apart from the rate and power reserve, this includes the winding performance, the chronograph function and the date switching.
WHAT TESTS DO YOU CARRY OUT ON THE FINISHED WATCH?
After casing up, we recheck every single function. Incidentally, all the testing stages are interconnected and build on one another. It means we also integrate the results from the FIM cell in the final inspection. When the watch is finished, we can test the water resistance and perform a last visual check. And from there, it’s off to IWC’s legendary 500-hour test. Here all the vital functions are subjected to further intensive testing for more than 20 days.
HOW DO YOU GUARANTEE SUSTAINABILITY IN THE MANUFACTURING CENTRE?
We attach enormous importance to responsible manufacturing practices. For example, we use renewable energies from various sources, treat waste water or use the waste heat from our processes. The eight-year guarantee we offer on our timepieces as part of the My IWC programme likewise reflects our high sustainability standards.
— Components of caliber 69000 in detail
Markus Bühler started his apprenticeship as a watchmaker at IWC Schaffhausen in 2001. Since then, he has remained loyal to the company. Among other positions, he has been Department Manager Industrialization and Head of Movement Assembly & Industrialization. Since 2020, in his position as Associate Director Watch & Movement Assembly, he has been responsible for the entire assembly process from movement to finished watch.