Lighter and harder than steel, absolutely scratch-resistant and with a mirror-like surface that feels pleasingly soft. This unique combination of properties makes ceramic an ideal material for watches. IWC is a trailblazer in the field and has been making ceramic cases for various watches over a period of almost 30 years. The main challenge lies in the highly complex manufacturing process. More recently, the non-wearing material has made its way into the movement.
The fascination of ceramic becomes tangible if you run the tip of a finger over a piece of high-quality porcelain. The surface feels as smooth as velvet and also pleasantly warm, particularly if snowflakes are drifting down outside the window. Apart from this, ceramic is absolutely scratch-resistant. The unique combination of properties also makes the material interesting for watches: as an imposing case for mechanical timepieces.
Obviously, porcelain would be out of the question for this purpose. The choice falls on specially developed engineering ceramics. “These inorganic, non-metallic materials are lighter and harder than steel, but at the same time extremely resistant to physical and chemical influences,” explains Lorenz Brunner, Head of the Innovation and Predevelopment Department with IWC in Schaffhausen. The material is unaffected by temperatures of well over 1000 degrees as well as moisture and even acid. The range of applications for which engineering ceramics like these are suitable is enormous: it includes capacitors, sealing rings and dental implants, but also extends to aircraft and rocket engines as well as components in low-consumption, high-performance engines.
EXTREMELY HARD CERAMICS START OUT AS POWDER
The high-tech ceramics used in watches are different from others in that the raw materials are much purer and the production processes more complex. Compared with porcelain, which is simply fired clay, they do not break so easily. “The source materials are polycrystalline powders, mostly minerals like silicates, aluminium oxide or silicon carbide,” explains Brunner. They are mixed with a number of auxiliary materials to a homogeneous mass, shaped and finally sintered at high temperatures in an oven. During the sintering process, the auxiliary materials are volatilized to leave extremely stable ceramic bodies consisting of countless microscopically small grains.
The production of ceramic cases for mechanical watches is a masterpiece of engineering. And IWC can look back on almost 30 years’ experience in this area. As early as 1986, it became the first watchmaking company to use specially hardened zirconium oxide ceramic for a case. The Da Vinci Ref. 3755 was a resounding success. The elegant and robust material was later used for the Pilot’s Watches and more recently made inroads into the Ingenieur family. With the special limited edition of the Top Gun Chronograph Antoine de Saint-Exupéry, the pioneers from Schaffhausen have once again trodden virgin territory: it is the first watch in IWC’s history to be housed in a case made of brown silicon nitride ceramic.
FEELING YOUR WAY FORWARD TO THE BEST SOLUTION
“The design and production of a ceramic watch case is a lengthy and difficult undertaking. IWC’s engineers liaise closely with their suppliers’ own specialists in the search for the best solutions,” says Brunner, in summary. One of the more unusual challenges is that ceramic shrinks by about a third during the sintering process. To ensure that the movement later fits snugly inside the case, the shrinkage has to be factored in as early as the design phase. And there is another unusual feature: unlike metals, whose properties are clearly defined and finalized before machining, ceramics – and thus the finished product – are influenced by the individual stages in the manufacturing process. The use of different sintering methods, together with the chosen grain size and sintering temperature, can lead to end products with significantly different properties from the same basic materials.
In the case of the brown ceramic used for the Pilot’s Watch Chronograph Antoine de Saint-Exupéry, the engineers carried out countless attempts and had to feel their way towards the optimum manufacturing process. During sintering, for example, the silicon nitride must not come into contact with oxygen because it could otherwise oxidize. This meant that the cases had to be baked in an oven at 1800 degrees Celsius using nitrogen to create an inert gas atmosphere. To make the material even denser, it is sintered under overpressure. The sumptuous brown colour was achieved by mixing the silicon nitride with titanium nitride.
This specific combination of raw materials makes the sintered silicon nitride even harder and more shatterproof than most other ceramics. But this, in turn, posed an additional challenge for the subsequent machining of the case. “The fact that the new material was so hard and robust made the milling process enormously hard work and we found ourselves replacing the diamond-tipped tools much more frequently than usual,” reminisces Brunner.
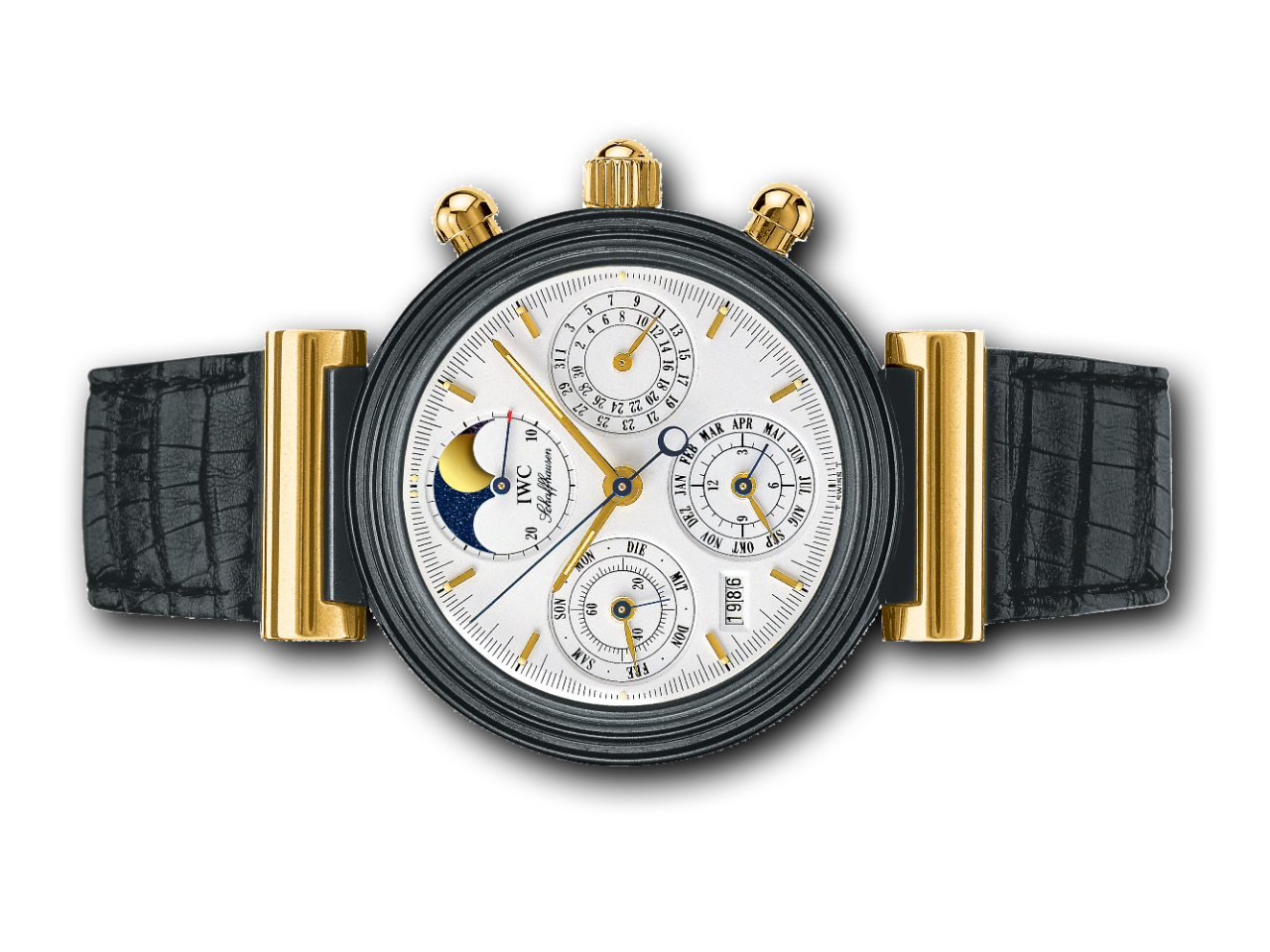
These inorganic, non-metallic materials are lighter and harder than steel, but at the same time extremely resistant to physical and chemical influences
CERAMIC COMPONENTS NOW FEATURE IN WATCH MOVEMENTS
The extreme wear-resistance of ceramics also makes them interesting for use in the watch’s interior. “Some of the parts in the movement are subject to incredibly high stresses and strains. And for that reason, we are trying to replace certain metal parts with ceramic components,” continues Brunner.
As with its cases, IWC is also taking a pioneering role in this area. The biggest difficulty lies in the fact that a part made of brass or steel cannot simply be replicated in ceramic. As a rule, the material itself influences the geometry of the piece. It is made all the more difficult by the minuscule dimensions and minimal tolerances in a watch movement: here, too, the engineers need to make allowance for the fact that ceramic loses around a third of its volume during sintering.
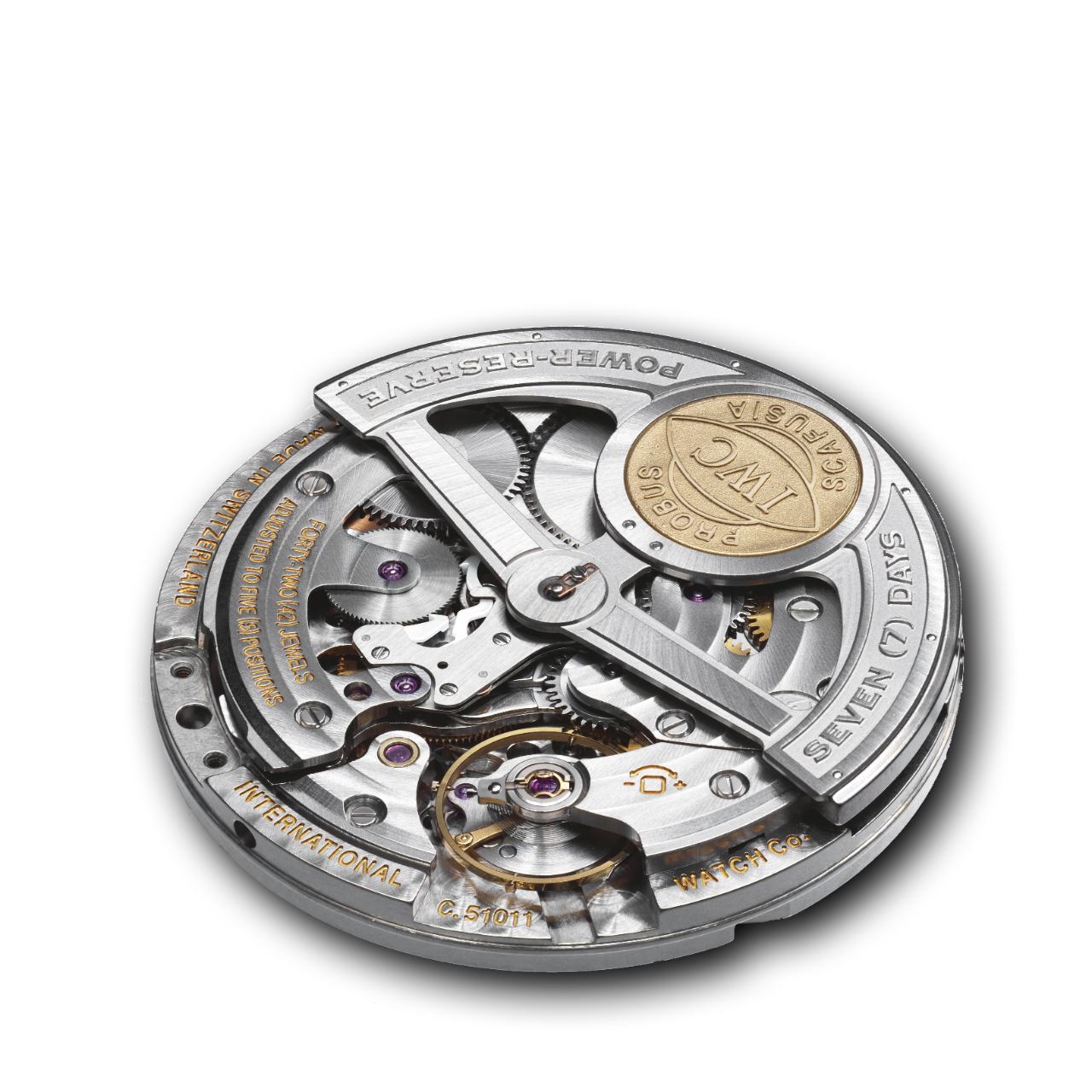
For the first time, in 2012, IWC succeeded in making the pawls for the Pellaton automatic winding system found in the Portugieser Tourbillon Mystère Retrograde from wear-resistant ceramic. Today, these pawls are used for all models in the 50000-calibre family. In addition, the oscillating pinion lever used in IWC chronograph movements manufactured in-house is mounted on ceramic bearings rather than ruby because the former is tougher than a gemstone.
In the 51000 calibres, a tiny ceramic tube has replaced the two jewel bearings at the centre of the rotor: “This facilitates more precise fitting of the rotor and eliminates the need for it to be trued,” is how Brunner describes the main advantage of this solution. Apart from wear-resistance, another reason for using ceramic is its lightness, especially when a part needs to be moved using as little energy as possible. “I’m a material scientist, and the thing that fascinates me most about ceramics is their durability,” says Brunner in conclusion. Indeed, there is hardly any other material that resists the ravages of time quite so well: a small figurine of Venus, made of fired clay, is one of the oldest known man-made artefacts and is aged around 30,000 years. IWC’s wonderful ceramic watches are destined to be a source of pleasure to their owners for a lifetime and will probably survive for many thousands of years beyond.
For the first time, in 2012, IWC succeeded in making the pawls for the pellaton automatic winding system found in the Portugieser Tourbillon Mystère Retrograde from wear-resistant ceramic
Continue reading
IWC’s New Proprietary 52000-Calibre Family
Technical improvements for maximum precision - The IWC-manufactured movements in the new 52000-calibre family feature numerous technical upgrades. Find out more.
IWC annual calendar the new small eternity
The newly developed Portugieser annual calendar shows the month, date and day in three separate, semicircular windows. Find out more.
