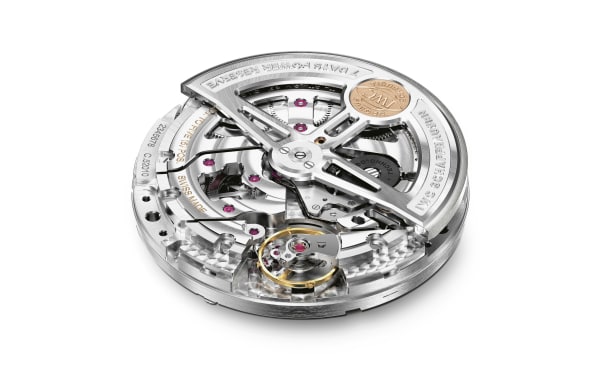
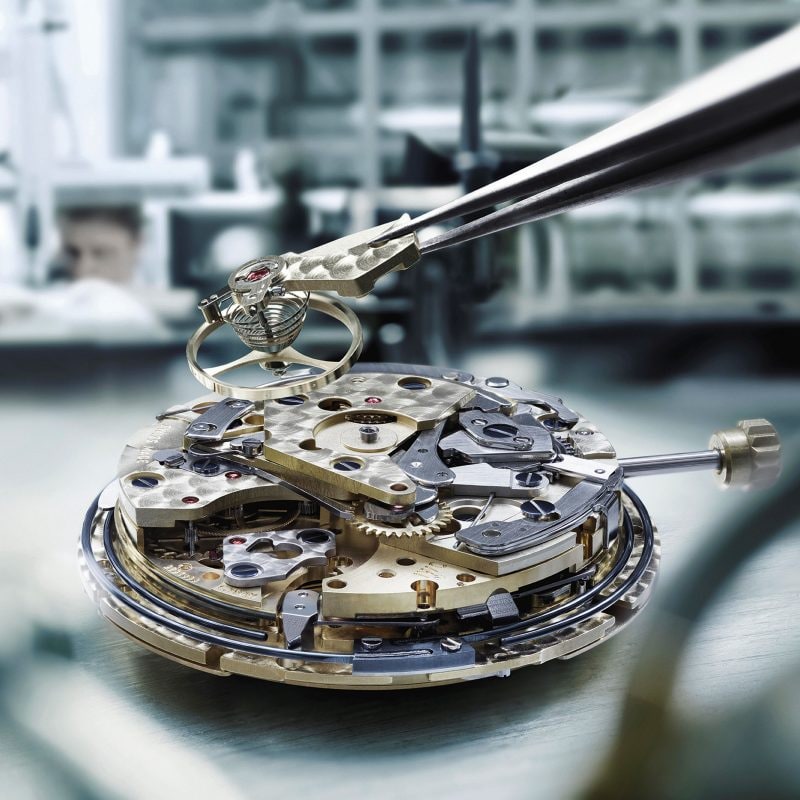
The Journal
ALL WOUND UP
Shipping and delivery conditions
FIND OUT EVERYTHING YOU NEED TO KNOW ABOUT THE MAINSPRINGS IN IWC’S AUTOMATIC, HANDWOUND AND CHRONOGRAPH MOVEMENTS
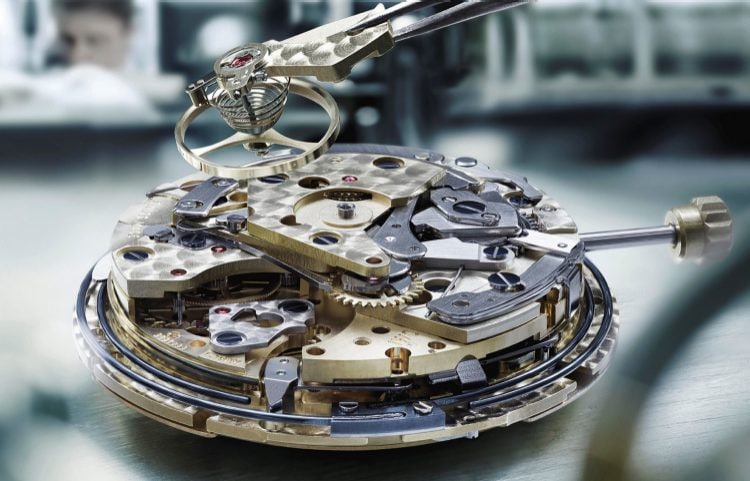
Before a mechanical watch movement can start moving, it needs an energy source to drive it. That energy source is the mainspring. And while there are some who enjoy engaging with the machine, lovingly winding it by hand, others take pleasure in the automatic mechanism, which will keep the watch running indefinitely, simply from the movements of the wearer’s arm.
Children are awestruck when a mechanical toy springs to life after being wound, or when music is emitted magically from a box. A mechanical watch is rather similar: as soon as it is supplied with the necessary energy, its heart starts to beat.“When the 59210 calibre’s mainspring is fully wound, it stores 1300 millijoules-worth of energy,” reveals Thomas Gäumann, head of IWC’s own movement development department in Schaffhausen. That’s roughly equivalent to the energy needed to lift a bar of chocolate through one metre thirty centimetres. This energy is generated and stored either when the watch is manually wound or, in the case of automatic watches, by the untiring revolutions of the rotor. Both mechanisms are technically sophisticated and incredibly precise.
A French watchmaker invented the crown-winding system so widely used today in around 1850. Before that, the mainspring was wound with a separate key. When the crown is turned, an intricate mechanism comprising levers, pinions and wheels transmits the rotations all the way to the barrel arbor, which winds up the spring from its inner end. To keep the watch running, the outer end of the spring distributes a continuous supply of energy to the wheel train. In a hand-wound movement, the spring is at maximum tension after about 70 rotations of the crown. A small click retains the spring to prevent the energy stored in it from running down immediately.
The mechanism is further complicated by the integration of the hand-setting system. When the crown is pulled out, a tiny clutch switches from the winding to the setting function. As so often in the world of mechanical watchmaking, the difficulty in the design lies in the minuscule dimensions of the entire subassembly. Simply fitting and setting the moving parts in the constricted space available is a masterstroke of precision engineering.
When the 59210 calibre’s mainspring is fully wound, it stores energy equivalent to the power needed to lift a bar of chocolate through one metre thirty centimetres.
THE SIZE OF THE SPRING ULTIMATELY DETERMINES THE POWER RESERVE
Hand-wound movements made in-house have a long tradition at IWC. In the 59000-calibre family, which today is the driving force behind the Portofino and Portugieser Hand-Wound Eight Day, Schaffhausen’s designers have created a veritable powerhouse. “The aim was to allow the owner to wind his watch just once a week,” explains Gäumann.
In practice, a number of factors have a bearing on the power reserve. Prime among these is the capacity of the energy storage medium: the bigger the barrel and the longer the mainspring, the more revolutions the barrel wheel will complete and the longer it will continue to power the wheel train. But complications such as a chronograph require energy and decrease the power reserve when active. Apart from this, there is a loss in efficiency caused by the transmission of power in the wheel train and the consumption of energy by the escapement.
Mindful of this, the design engineers consciously decided to omit all complications on the new hand-wound calibre with the exception of the date and power reserve displays. The generously sized barrel measures 1.7 centimetres in diameter and accommodates an 86-centimetre-long spring, which discharges its energy in 14 revolutions.
To put this in perspective: IWC’s in-house chronograph movements have a mainspring just 50 centimetres in length, which runs down after 11 revolutions. The energy stored by the 59000 calibres would suffice for nine days. But to ensure that the level of power discharged — and thus the rate — remain as constant as possible, the movement stops automatically after exactly 192 hours, or eight days. A display shows how much power remains at any one time.
GENERATING TENSION FROM NATURAL MOVEMENT
Automatic movement fans can forget all about this because they have something akin to a perpetuum mobile on their wrists. “In a self-winding system,” says Gäumann, explaining the principle behind it, “a centrally mounted, half-moon-shaped rotor converts the wearer’s natural movements into energy for the spring.” It is all made possible by a combination of the rotor’s inertia and gravity: its weight constantly forces it downward, and it starts to move as soon as there is any acceleration. The movements of the wearer’s arm when walking are a particularly efficient way of generating energy.
At IWC, the automatic winding system is inseparably linked with Albert Pellaton. In 1944, as the company’s Technical Director, he pushed forward with the development of a solution that still powers many of the movements made by IWC. To achieve it, he had to surmount several problems. The systems that existed back then transmitted the movements of the rotor through an intricate system of gears and, as a rule, could use rotations only in one direction. As a result, the power and energy losses were considerable. The trailblazing feature in Pellaton’s solution was that it converted the revolutions of the rotor into an oscillating motion that could be used much more efficiently for winding the spring. At the heart of his winding system is an eccentric cam, which transforms the revolutions of the rotor into to-and-fro movements in a rocking bar. Two offset pawls mounted on the bar transfer the energy to the winding wheel. While one pulls the wheel (i.e. winds it), the other glides smoothly over its teeth until the roles are reversed. This pawl-winding system makes use of any movement in the rotor, no matter how small and in either direction.
EVERYDAY USE PUTS THE AUTOMATIC MECHANISM TO THE TEST
The rotor completes almost 2000 full revolutions, for instance, until the imposing IWC automatic movement is fully wound. Someone who moves a lot will achieve this in just a few hours. In the case of a careful owner, who occasionally takes the watch off, it can take up to a day. “The main problem with designing a mechanism like this is to find a compromise that suits everyone, regardless of how much they move,” explains Gäumann. For this reason, early on in the development phase, Schaffhausen’s automatic movements are put through their paces by a range of testers with very different lifestyles.
In everyday use, the automatic winding system is exposed to all kinds of stresses and strains. Although the rotor weighs only a few grams, the massive forces exerted on the components during rapid movements may be as much as 1000 times that of gravity. In some models, the rotor is protected against severe impacts by a spring-mounted bearing. Although the way the Pellaton winding system functions has remained fundamentally unchanged for over 60 years, it has still undergone continuous improvement. Today, for example, the pawls are ceramic and virtually impervious to wear and tear. For the 89000 chronograph calibre, the entire mechanism has undergone a thorough overhaul. The resulting double-pawl winding system does the job with fewer parts and, thanks to the use of two pairs of pawls, is even more efficient.
So whether manually or through the wearer’s own movements, both systems reliably serve their purpose of supplying the watch with energy and bringing the delicate mechanism to life. But ask devotees which of the two mechanisms is better or more beautiful and the answers are as different now as they will be in a hundred years.