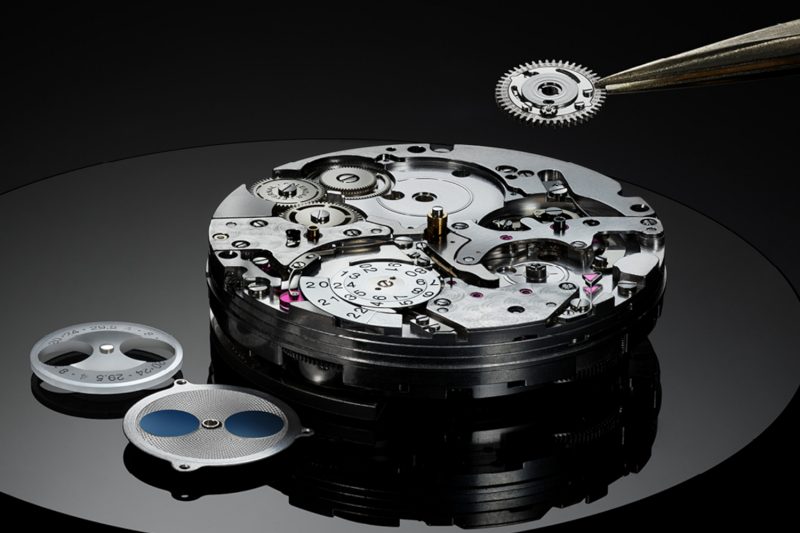
The Journal
WHY NOT COMPLICATE THINGS?
Shipping and delivery conditions
THE BRAINS BEHIND THE DESIGN AND CONSTRUCTION OF IWC’S TIMEPIECES DISCUSS THE NEW PORTUGIESER ETERNAL CALENDAR, PUSHING BOUNDARIES, AND THE UNIQUE IWC WAY OF CALENDARS
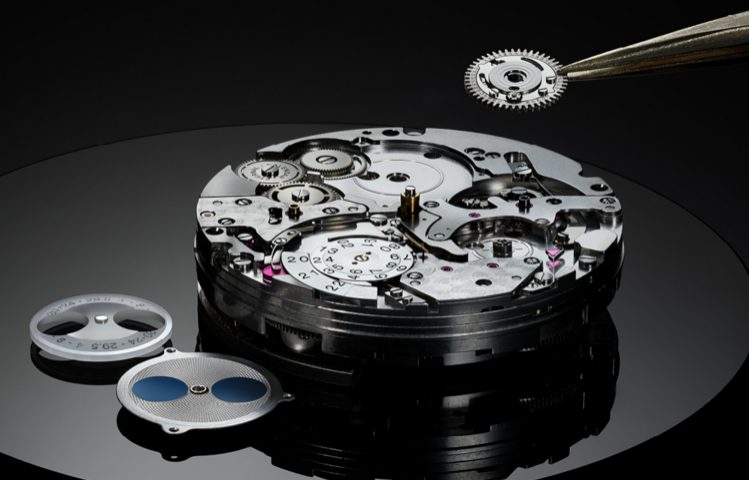
The new Portugieser collection is an inspired combination of craftsmanship with precision technology, fueled by the instinctive need of engineers to make things better. That need manifests itself in sophisticated complications, elaborately crafted dials, and a slimmed-down case design with double box-glass sapphire crystals.
THE IWC SPIRIT OF INNOVATION
Christian Knoop and Markus Bühler, what makes IWC Schaffhausen so unique?
Christian Knoop (CK): We are one of a small group of watch manufacturers in northeastern Switzerland. Schaffhausen is far removed from the traditional watchmaking centers in the French-speaking part of the country. As a result, we’ve gone our own way from day one. We’ve consistently invested in the training of our specialists and developed a complete range of craft-related skills. In addition to watchmakers and surface finishers, we now also train poly-mechanics and design engineers.
Markus Bühler (MB): Equally important is a corporate culture characterized by curiosity and a spirit of innovation. During my time as an apprentice watchmaker at IWC Schaffhausen, I took part in several competitions. That led to the birth of the Big Pilot’s Watch with its jet engine-inspired turbine. It’s also why I’m so delighted that the idea for the day/night display in the new Portugieser Hand-Wound Tourbillon Day & Night also came from an apprentice watchmaker.
— Markus Bühler, Associate Director Watch & Movement Assembly (left), and Christian Knoop, Chief Design Officer (right)
We see ourselves as engineers, so it’s part of our make-up to question things and want to improve them. We’re constantly exploring the limits of what is feasible and developing functional, robust and technically elegant solutions
— IWC-manufactured 52616 caliber of the Portugieser Perpetual Calendar 44 IW503703 with a Horizon blue dial
INTERPLAY BETWEEN CRAFTSMANSHIP AND STATE-OF-THE-ART TECHNOLOGY
What makes IWC’s approach so unusual?
CK: It was initially inspired by our founder, and we’ve since developed a watchmaking culture that combines craftsmanship with state-of-the-art technologies. Wherever maximum precision and accuracy are called for, we use machines – to produce components to tolerances of a few thousandths of a millimeter, for example. But it’s a different story regarding tasks only humans can carry out. For the assembly and precision adjustment of our in-house movements or complex complications such as the tourbillon, we rely entirely on the skills and expertise of our watchmakers.
MB: Yes, assembling and adjusting a tourbillon is incredibly demanding. The flying minute tourbillon in the new collection comprises 56 individual parts and weighs just 0.675 grams. Handling minuscule, intricate components like these is always a challenge, even for an experienced watchmaker. And because the escapement rotates around itself in its cage once a minute, the precision adjustment is also very complicated.
So, how did IWC’s affinity with engineering come about?
CK: Our American founder, Florentine Ariosto Jones, was both a watchmaker and an engineer and came to Schaffhausen from Boston in 1868 to realize his vision of centralized watch production. He planned to combine the skills and artisanship of Swiss watchmakers with advanced American manufacturing methods, powered directly by the current of the Rhine. That laid the foundations for IWC’s engineering approach.
MB: We see ourselves as engineers, so it’s part of our makeup to question things and want to improve them. We’re constantly exploring the limits of what is feasible and developing functional, robust and technically elegant solutions. If I can stay with the example of the tourbillon, we’ve made the mechanism even more efficient by giving it a diamond coating. This reduces friction and improves the movement’s energy flow while contributing to a high-power reserve.
In the new Portugieser Eternal Calendar, the moon phase will deviate by one day in 45 million years. Of course, that’s a purely theoretical value. But we are engineers and simply can’t stop pushing the boundaries of what is possible. Admittedly, we sometimes overshoot the mark
CONTINUOUSLY PUSHING BOUNDARIES
Calendars are another typical example of engineering at IWC.
CK: Absolutely. Our master watchmaker, Kurt Klaus, pioneered the perpetual calendar in the 1980s. All the displays are synchronized and easily adjusted using the crown. His perpetual calendar has remained a paragon of user-friendliness to this day. The entire mechanism contains 81 parts but fits into a module only 1.5 millimeters high.
Nevertheless, the calendar needs to be corrected in centuries that aren’t divisible by 400. That’s why we’ve now taken the concept to a new level with the Portugieser Eternal Calendar. Our first secular perpetual calendar allows for these anomalies and will calculate the leap year correctly, at least until 3999.
MB: Yes, typical IWC. You can also see it in the moon phase display, which we’ve continued to improve over the years. The 1985 Perpetual Calendar was precise to one day in 122 years, and by 2003, the Portugieser Perpetual Calendar had pushed that to one day in 577.5 years. In the new Portugieser Eternal Calendar, the moon phase will deviate by one day in 45 million years. Of course, that’s a purely theoretical value. But we are engineers and simply can’t stop pushing the boundaries of what is possible. Admittedly, we sometimes overshoot the mark.
— The Portugieser Eternal Calendar IW505701 calculates the leap year correctly until at least the year 3999
— The Eternal Calendar’s characteristic Double Moon™ indication of the IWC-manufactured 52640 caliber
EXQUISITE DECORATION
Then we have the intricately decorated in-house movements in the new Portugieser collection, another demonstration of IWC craftsmanship.
MB: We use high-quality IWC-manufactured movements for all the models in the collection. For the Portugieser Eternal Calendar, we developed the IWC-manufactured 52640 caliber, which integrates the eternal calendar module.
Another highlight is the IWC-manufactured 81925 caliber in the Portugieser Hand-Wound Tourbillon Day & Night. It has a gold-plated bottom plate decorated with circular Côtes de Genève. The area containing the barrel is also skeletonized. The movements in the 52000- and 82000-calibre families have a Pellaton winding system reinforced with ceramic components. And finally, the IWC-manufactured 69000 caliber, our robust and reliable chronograph movement, holds its regular place in the collection.
The dials of all the watches in the collection have a high-quality finish and a compelling aesthetic appeal. How do you produce those?
CK: The dials result from a complex manufacturing process involving up to 60 individual machining steps. We first give the precision-punched brass blanks a sunburst finish or finely blast the surface. Then we apply the color. The key to the extraordinary visual depth is the application of 15 layers of clear lacquer, which is sanded smooth and then polished to a high gloss. The totalizers or subdials are milled into the blank and the lacquer layers.
The printing further emphasizes the three-dimensional effect, adding to the sensation of depth. Finally, the appliques for the numerals are hand-mounted. The glass dial of the Portugieser Eternal Calendar is an unusual feature. It is printed in white on the underside. The subdials are ground and polished separately. Here, too, the appliques are hand-mounted.
SLIMMER CASE AND DOUBLE-BOX GLASS
For specific models, you’ve also reworked the case design, which now looks much lighter and more elegant.
CK: We managed to slim down the casing ring for the Portugieser Perpetual Calendar 44 and the Portugieser Automatic models both geometrically and visually. At the same time, we use box-shaped sapphire lenses at the front and rear, enhancing the sense of elegance and lightness. The manufacturing process for these glasses is also very complex.
MB: Sapphire is exceptionally scratch-resistant and hard-wearing. It is the second-hardest material in the world after diamond. That means you can machine it only with diamond tools. Strictly speaking, however, this is not a glass but a synthetically produced corundum crystal. High-purity aluminum oxide powder is heated to over 2,000 degrees Celsius.
From below, a solid sapphire block grows out of the powder, from which rods are cut out as raw material for the watch crystals. Due to their domed shape, the glasses have to be hollowed out from below. Milling is a challenge with glass thicknesses of just over one millimeter and very thin walls. At this stage, the glass has a cloudy surface and only becomes transparent after polishing.
Thank you, Christian and Markus, for sharing your thoughts.
— The movement and dial of the Portugieser Perpetual Calendar 44 are visible through the box-glass sapphire crystals