A series of mellifluous chimes from inside the watch announces the time on demand to the nearest minute. In bygone days, people relied on the minute repeater to tell them the time even when it was completely dark. Comprising more than 200 individual parts, the mechanism is considered to be the most sophisticated complication that can be integrated into a wristwatch. IWC first reached this pinnacle in precision mechanics with its legendary Grande Complication of 1990. Today, the minute repeater also has its place in the Portugieser family, where it continues to enchant watch devotees.
In today’s 24/7 society, street lighting and garish neon displays turn night into day. The minute repeater, which announces the time acoustically, is a reminder of a past in which neither electric light nor luminescent hands existed. The first repeating watches were produced in the 17th century. However, the mechanism was first used in a wristwatch around the beginning of the 20th century. When the repeating slide on the side of the case is fully depressed, a complex mechanism translates the time shown on the dial into a series of tones, which are produced by small hammers striking two gongs inside the case. First, the hours are chimed out on the lower-pitched gong. These are followed by double strikes on the lower- and higher-pitched gongs for the quarters and, finally, by the number of minutes on the higher-pitched of the two gongs.
The first repeating watches were produced in the 17th century
THE REPEATER HAS ITS OWN SEPARATE SOURCE OF ENERGY
Unlike the chronograph or perpetual calendar, which is supplied with energy by the basic movement, the minute repeater has its own autonomous power source. This is essential, because activating the repeater sets many energy-sapping lever movements in motion. When the repeating slide is pushed down, it winds a spring approximately 10 centimetres in length. The energy it stores is sufficient to generate the longest possible series of strikes, 32, which takes place twice a day at one minute to one. The sophisticated all-or-nothing mechanism ensures that the repeater cannot chime out an incomplete sequence of notes. A rocking bar and a hook release the strike train only when the repeating slide is fully depressed.
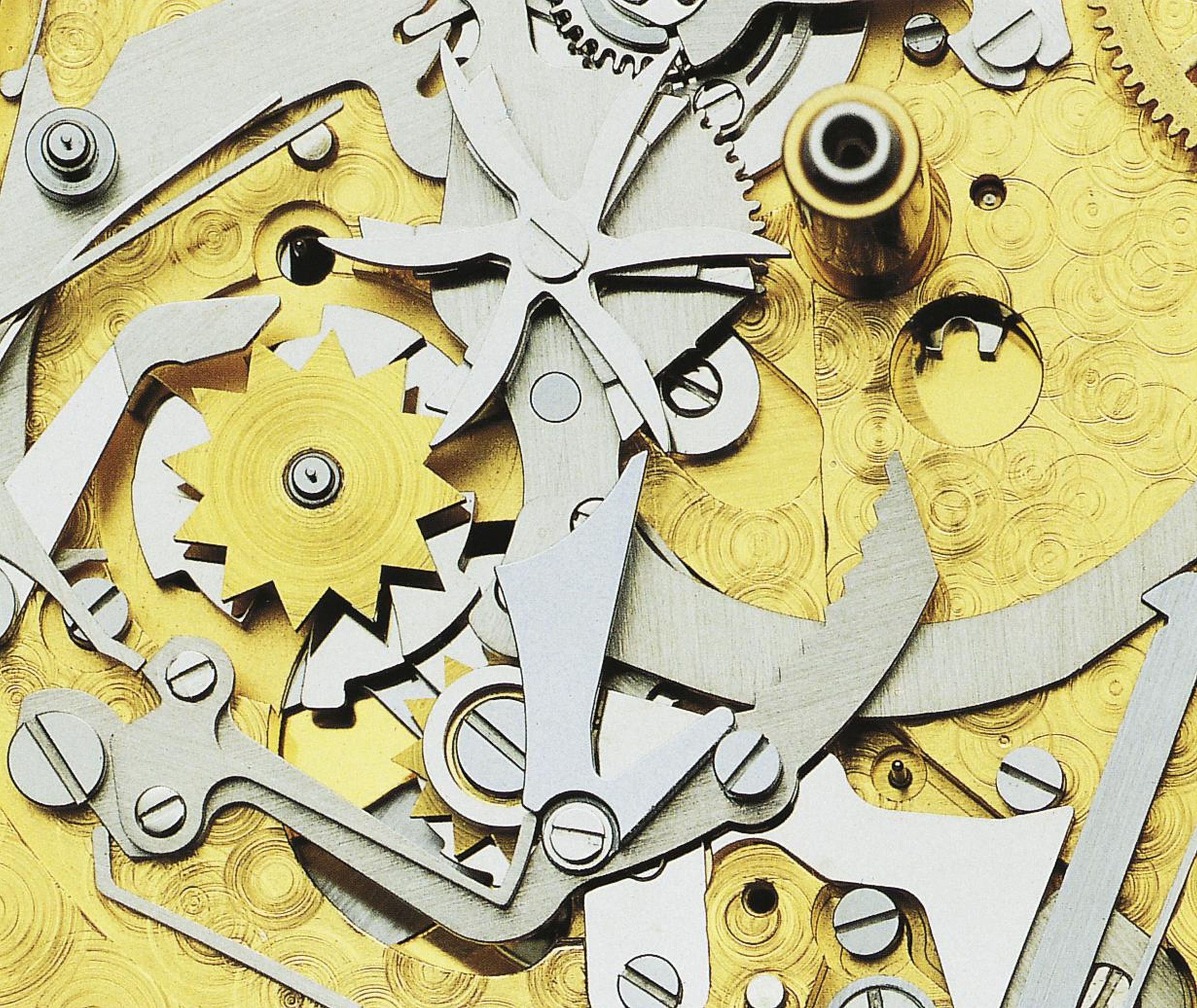
TIME IS TRANSMITTED TO THE REPEATER BY SNAILS
But how does the strike train know how many times to hit the gongs? “The time of day is transmitted through a series of snails that advance synchronously with the hands,” is how Kittlas describes the sequence. The hour, quarter and minute snails have different angles of rise and fall, gear depths and notches. Rather like punch cards in the early days of computer technology, they can be read off mechanically. One special feature of IWC’s design is that the cannon pinion does not serve as the point of contact between the basic movement and the repeating mechanism. In fact, the rotations of the minute wheel are used to transmit information about the time to the snails. The developers chose this approach in order to keep the mechanism clearly separate from the switching impulses for the calendar module in the Grande Complication and to ensure no interference.
Even when the repeating mechanism is in its rest phase, the basic movement never stops providing information about the time of time. But it is only actually read off when the repeating slide is fully depressed and the spring is put under tension. At the same time, several levers engage with the snails and read off the number of strikes to be transmitted to the strike train. This information is transmitted via distributors to two racks: one for the hours and quarters, a second for the minutes. At a later phase, the teeth on these racks will activate the so-called gathering pallets and initiate the strikes on the gongs. During the winding phase, the two racks are moved precisly to a point where the correct number of teeth come to rest behind the gathering pallets. All this takes place within fractions of a second.
VERY FEW WATCHMAKERS MASTER THE CHALLENGE
As simple as it may be for the watch’s owner to activate this acoustic spectacle, all the more complex is the way in which it works: “Within the confines of a space just 2.2 millimetres high, 220 parts work together with the utmost precision. In some places, a few thousandths of a millimetre determine whether the mechanism will function correctly,” explains Hansjörg Kittlas, who heads up the department of speciality movement assembly at IWC in Schaffhausen. The assembly and adjustment of a minute repeater take over three weeks to complete and demand expertise, experience and skilled craftsmanship of the highest calibre. And only a very small number of watchmakers are able to construct this complication by themselves from scratch.
At IWC, it was the highly ambitious Grande Complication project that gave the company the motivation needed to develop its own minute repeater. Two watchmakers, Dominique Renaud and Giulio Papi, spent thousands of hours developing a solution that has remained pre-eminent to this day and made its first big appearance in the Reference 3770 of 1990. Later, the mechanism was also used in “Il Destriero Scafusia”, which was produced to mark the company’s 125th anniversary. Today, the delicated chimes that ring out from the Portugieser Grande Complication and the Portugieser Minute Repeater are a reminder of the ship’s bells on frigates announcing the changing of the guard.
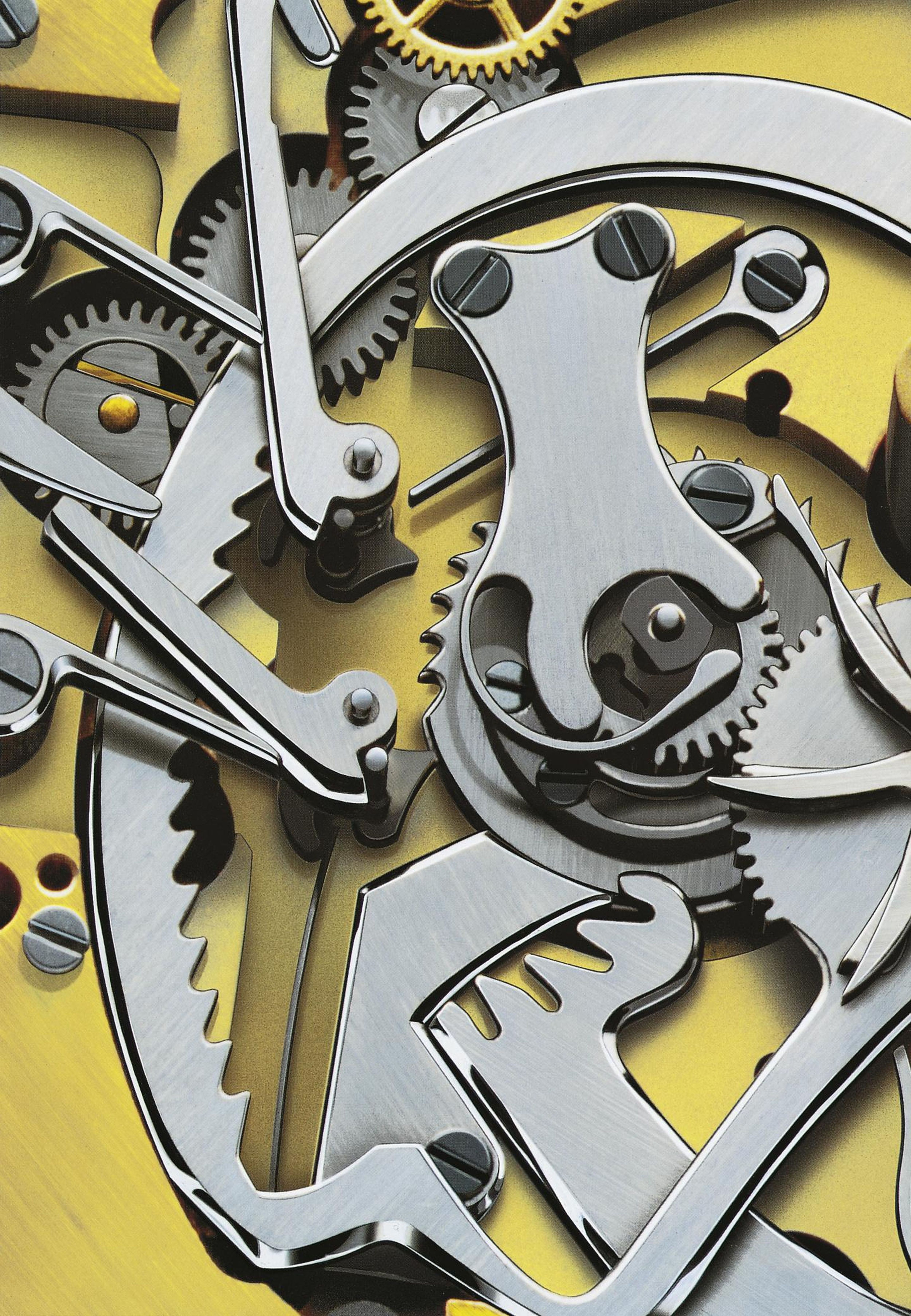
THE SOPHISTICATED DESIGN GUARANTEES STABILITY
In order to ensure that this voice continues to be heard no matter what turns the owner’s life takes, the design engineers followed an old IWC tradition and attached much importance to making the watch functional and suitable for everyday use. The mechanism is designed in such a way that even inadvertently moving the hands during the rest phase will never affect the repeater. The combined hour-and-quarter rack is another new feature: this means that initiation of the hour and quarter strikes is now integrated in a single component. The developers have also reduced the size of the system that reads off the quarters while the minute rack has a new shape with internal toothing. For the first time ever in the watchmaking industry, they have also made a miniaturized idle wheel that disconnects the strike train from the power flow when the spring is being wound. All these smart design features have made the striking sequence extremely stable.
THE MULTIFUNCTIONAL BARREL ARBOR CONTROLS THE PROCESS
When the repeating mechanism has received the necessary information and the spring is fully wound, the performance can commence: “Mounted on the barrel arbor is a control mechanism comprising around 15 individual parts. This mechanism ensures that the hour strikes are followed by the quarters and finally the minutes,” says Kittlas, describing this intricate sub-assembly. To achieve this, the hour and quarter rack is first hooked up to the rotational of the barrel arbor through a system of drivers and disconnecting pieces. Every time one of the teeth passes a gathering pallet, it causes a hammer to strike one of the two gongs. When all the hours and quarters have been struck, the clutch system connects the minute rack to the barrel arbor and the minutes are chimed out. To ensure that the chimes are not struck too rapidly and that the speed of the sequence remains constant even when the tension in the spring is depleted, the system has a so-called governor.
The watch’s delicate tones are created when two tiny hammers strike the steel gongs, which are bent into shape and run around the periphery of the movement. The precise composition of the alloy used for the gongs as well as the methods used to make them are among the most closely guarded secrets of any specialist watch manufacturer. At IWC, too, it took countless experiments with a variety of materials until the sound met the high requirements. As with a piano string, the active, vibrating length of the spring determines the tone. Together, the gongs create a melodious fourth and have to be laboriously tuned by hand. But the case material also influences the tones heard by the owner. 5N gold and yellow gold oscillate especially well. “Every single Portugieser Minute Repeater is unique and has its own unmistakable voice,” says Kittlas, not without pride.
Every time one of the teeth passes a gathering pallet, it causes a hammer to strike one of the two gongs
NEW MANUFACTURING PROCESSES INCREASE PRECISION
Nevertheless, the design has not remained unchanged since it first appeared over 20 years ago. “The basic function has remained identical, but we never stop working on improving the system,” says Kittlas. New production processes have also been used. The hour and quarter rack is now made using a special lithographic process that makes extremely high levels of precision possible. Production of the complex minute transmission wheel, which has six arithmetically curved arms, is now also much more accurate.
For Hansjörg Kittlas the minute repeater belongs up in watchmaking’s higher echelons alongside the astronomic module used in the Portugieser Sidérale Scafusia. And this is precisely why it so intrigues him. “After weeks and weeks of painstakingly concentrated work, it never ceases to amaze me when this complicated little construct comes to life and makes its voice heard,” he explains. It is, of course, a voice reserved exclusively to a small circle of privileged watch lovers.
CONTINUE READING
A beautiful way to show the passage of time
The dial is the star act in any mechanical watch, so it is vital that the design and finish satisfy the most exacting aesthetic demands. Find out more.
Florentine Ariosto Jones
Florentine Ariosto Jones, who founded IWC in 1868, is one of the most important but also most enigmatic figures in the history of IWC. Find out more.
A Strict Head Timer and a Precision Watch
“Chef régleur” Jean Häberli won gold medals for IWC more than a century ago. He was responsible for the accurate timing of watches leaving Schaffhausen.
