COMPANY
Watches from Schaffhausen
Every watch from IWC is individually assembled by one of our professional watchmakers. Using their trained eyes, dexterous fingers and precision instruments, they bring together up to several hundred individual parts to create outstanding wristwatches: showpieces of meticulous workmanship, functionality and design, each an outstanding example of the art of watchmaking at its very best.
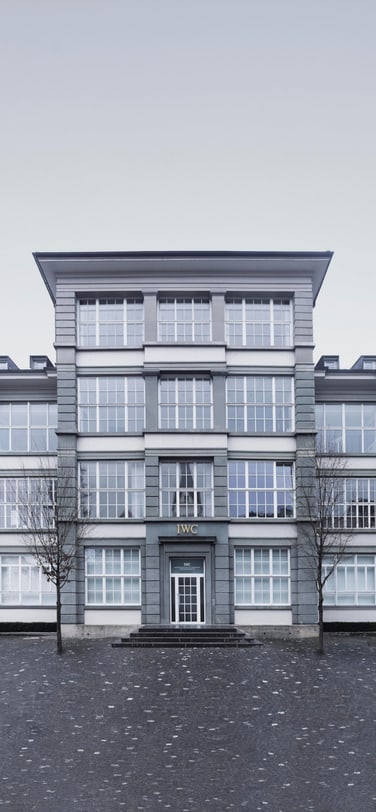
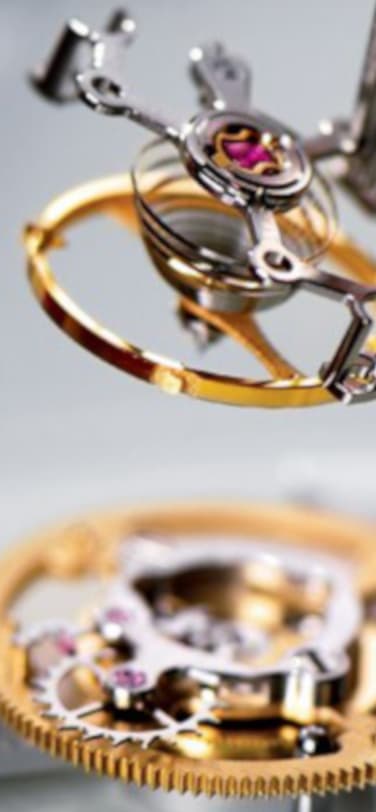
IWC’s Philosophy
The vast majority of Switzerland’s watch manufacturers are based in the French-speaking part of the country, making Schaffhausen an island in the watchmaking industry. Since IWC’s foundation in 1868, the unusual geographical location has helped shape the company’s philosophy. In its premises directly on the banks of the Rhine, IWC produces precision timepieces of lasting value with a clear focus on technology and development. With a passion for innovative solutions and technical inventiveness, IWC has established an international reputation. As one of the world’s leading premium brands in the luxury watch segment, it creates masterpieces of haute horlogerie that combine engineering and precision with exclusive design. The brand’s good name is founded not least on the fact that its highly qualified employees master every step of the production process behind in-house movements and complications such as the minute repeater, the tourbillon and the perpetual calendar. For the designers and construction specialists at IWC, the claim to excellence, “Probus Scafusia” – “Craftsmanship made in Schaffhausen”, first formulated in 1903, is not only an enormous challenge but also their great passion.
Development
Before a watch from IWC ticks for the first time
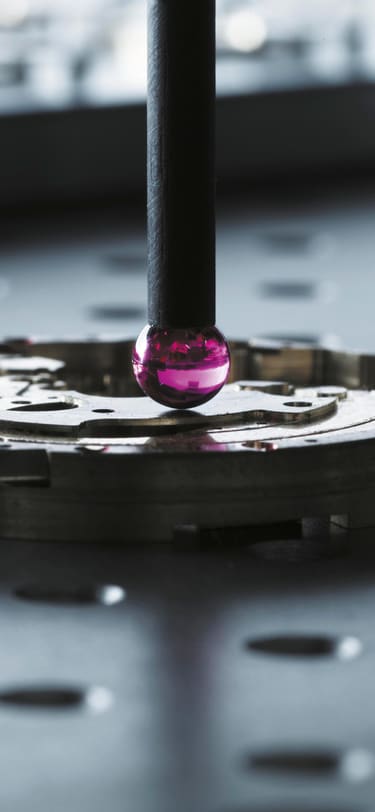
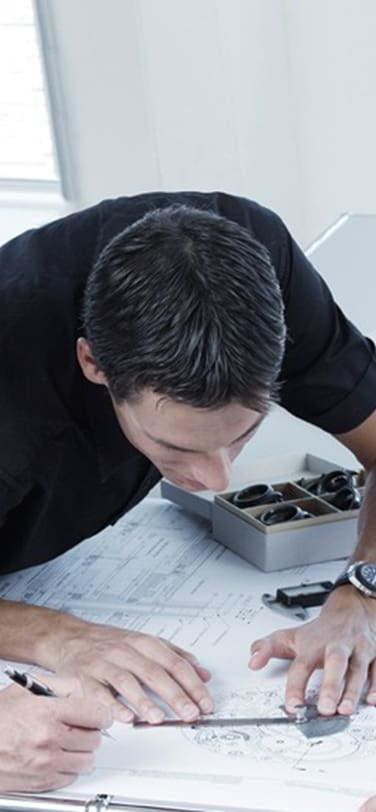
Construction and Design
When IWC starts developing a new model, our designers and construction specialists ask themselves one question: What precisely do we wish to achieve? Should the watch set new standards in complexity? Will its main strength be the power reserve, or perhaps its water-resistance? They start out by modelling the first components using computer-aided design. Here, IWC attaches enormous importance to integrating the work of construction and design with modern production technology. Working closely with our construction engineers, the watch designers play a crucial role in determining how best to harmonize form and function. The dial and the strap or bracelet, the position of the displays, the choice of materials and colours and the surface finish are always the logical outcome of constructive teamwork. Apart from the technological achievement and an attractive design, other, more emotional, aspects – such as the way the watch actually feels in the hand – also play an important role. Thus, the feel of the edge of the case, the way a push-button is activated or the sound of the crown as it engages are not left to chance. Often, the construction engineers and designers take their inspiration from old sketches and drawings. Ultimately, it is respect for the watchmaking pioneers of the past that guarantees continuity at the Schaffhausen-based company.
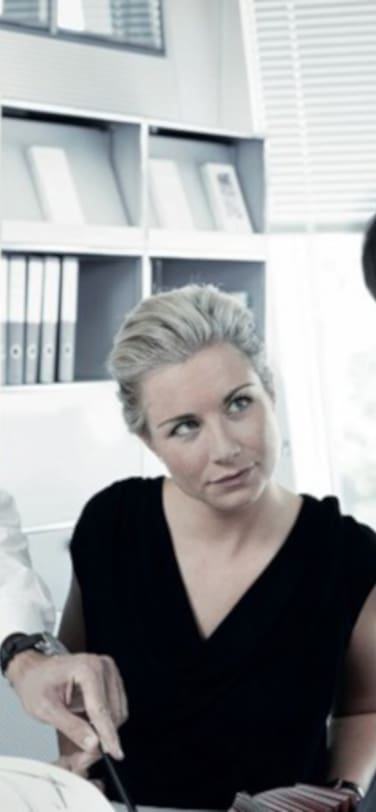
Quality Management
Thanks to a sophisticated development and quality management system backed by an exacting inspection and testing programme, IWC can guarantee quality of the highest order. The advanced scientific methods used include three-dimensional computer simulations, X-ray-based material analyses or tests designed to show how watches behave under extreme everyday conditions. The use of high-speed cameras and laser measuring instruments makes even the tiniest movements visible, while sophisticated software calculates exactly what stresses a part will tolerate.
Details such as wheels, shafts, tooth profiles or the dimensions of springs are examined for potential sources of error from the earliest phases of development. IWC refers to this process as “failure mode and effects analysis” (FMEA). The developers draw on their experience from earlier projects, feedback from the market and suggestions about ways to make watches more service-friendly. The result is an IWC watch that will continue to run and can be repaired for many years to come.
Tests
The long hard road from prototype to finished product
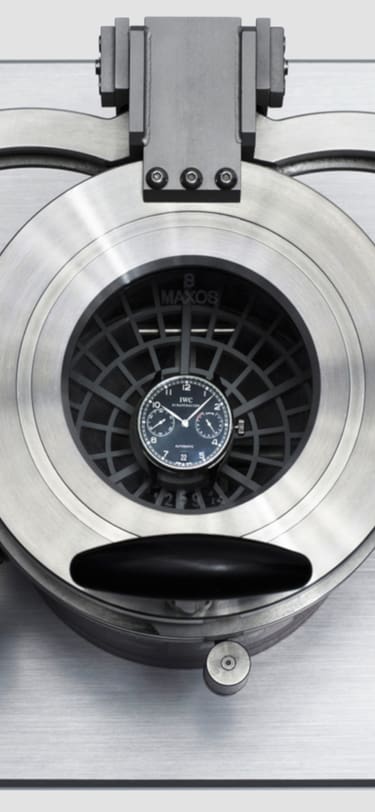
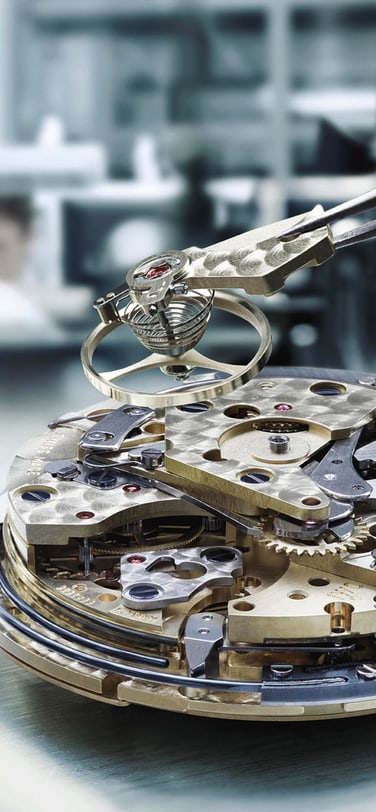
Qualification and Approval Process
Qualification is a term used to describe a programme of around 30 exacting tests lasting several months that are designed for new watches at the prototype phase or later as part of the approval process for the pilot series. The tests simulate, in condensed form, just about everything that can happen to a watch, under normal and extreme conditions, during the course of its long life. Only when several prototypes have passed stringent testing and a pilot run has revealed no more problems is the company ready to go into series manufacture and add another fascinating chapter to the legend that is IWC.
Corrosion and UV Tests
A two-week test in a saline bath at 37 degrees Celsius weeds out materials that would corrode in daily use or salt water. Dials are exposed to strong ultraviolet light for days on end and must not show any change in colour.
Abrasion Test
For test purposes, some parts are manufactured as early as the design phase in order to check the minimum requirements for those components subjected to unusually high wear and tear. Take the Aquatimer’s rotating bezel, for instance, which undergoes a fatigue test equivalent to four dives per day, guaranteeing a minimum service life of 10 years. The rotating bezels in IWC’s diver’s watches also have to prove their reliability in dirty water. On the crown/push-button testing stand, chronograph push-buttons are operated 10,000 or even 20,000 times to assess their resistance to wear and tear.
Climate Tests
In the climate test, the entire spectrum of thermal conditions a watch can be exposed to are systematically tested. Geographically speaking, this embraces everything from Alaska to the Sahara and the Brazilian rainforest. Watches are placed in a test chamber where, over a period of days and sometimes weeks, they have to withstand temperature changes from –20 to +70 degrees Celsius and up to 95 per cent relative humidity. The next item on the agenda after this ordeal is long-term monitoring of the rate. This test makes use of an automatic multilevel microphone to check the regularity of the beat.
Assembly
At IWC, high technology and craftsmanship are not a contradiction
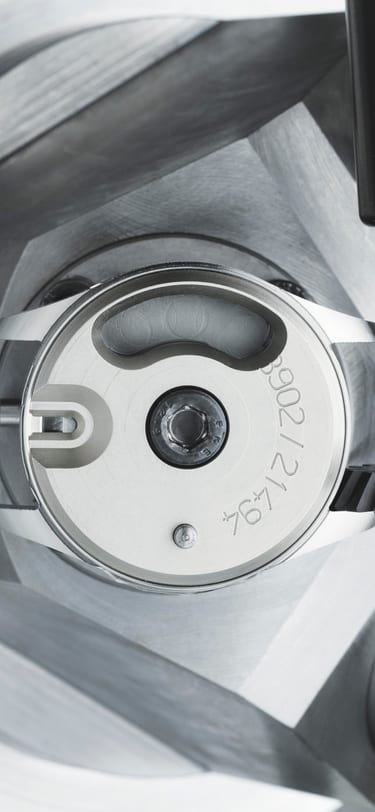
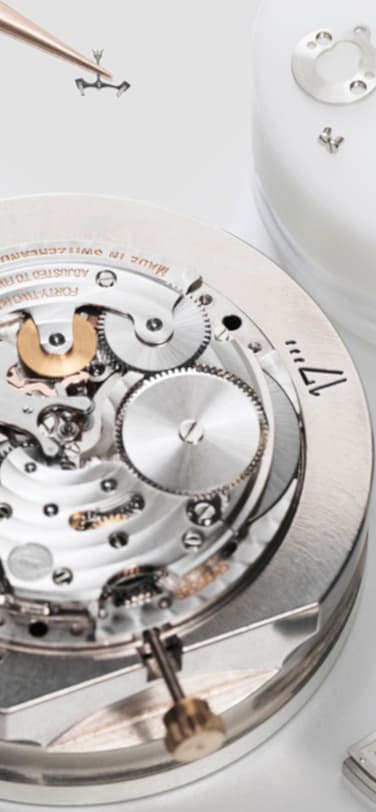
Production Techniques
During parts production, blanks are machined with the help of CNC milling machines. After surface machining, the acceptable tolerance for components, in general, is just +/–0.02 millimetres, but in certain cases this may be as low as +/–0.002 millimetres. After machining, the parts are finished by hand or proceed to an electric discharge machine. CNC wire electric discharge machines are used primarily for parts in the movement. The surface roughness can be controlled to a tolerance of 0.005 millimetres, but for precision EDM work, it is as low as 0.001 millimetres.
Assembling the Movement
Assembly of the movement consists of connecting the winding mechanism, train and escapement, followed by “réglage”, or precision adjustment. Depending on the model, it may also involve the automatic winding and chronograph mechanisms as well as the calendar and hour counter. The most complex of these jobs is adjusting the escapement and aligning the balance spring so that it runs true and flat: this is a high-precision manual task that no machine could ever carry out, even remotely, to the same high quality standards. Functions and precision adjustments are checked and corrected continuously at every stage of the assembly process. After this, highly skilled watchmakers in the complications department add on complications such as the perpetual calendar or split-seconds mechanism to the basic movement. In the special features department, the watch movements are fitted with tourbillons and minute repeaters from the bottom up: they pass through the preliminary assembly and assembly stages, all fine adjustments are made and they are fitted into the cases.
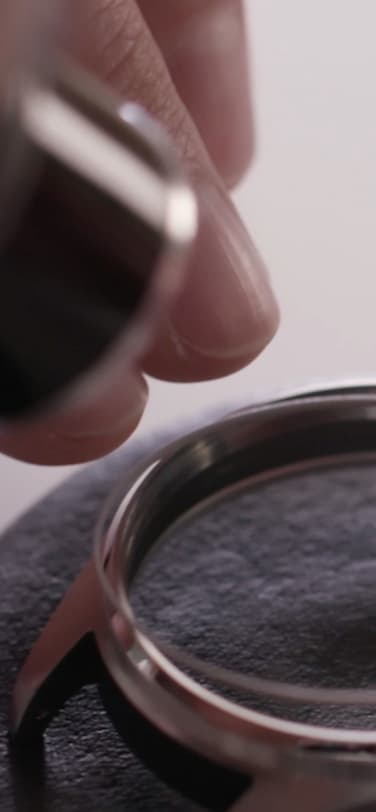
Case Manufacturing and Assembly
In terms of the precision and effort involved, the manufacture of the case is in no way inferior to the other stages in production. For watches made of a precious metal, the case parts are manufactured from pre-formed blanks. Stainless-steel and titanium cases are made from bars, specially produced for IWC, which are machined on CNC lathe and milling machines to an accuracy of one-hundredth of a millimetre. Milling machines are used to cut the horns for the strap or bracelet and the apertures for the crown and push-buttons into the casing rings, and to create the complex open surfaces, such as those on the cases of the Ingenieur watches. After the cutting process, the measurements are meticulously checked and the surfaces brought up to IWC standards of precision. The edges are deburred and rounded off, or faceted. All traces of lathing, milling and machining are removed, and the surfaces are finely ground and polished, satin-finished and blasted. Specialists now apply decorative surfaces such as circular graining to certain parts of the case, including places not visible from outside. Finally, a series of complex tests, such as water-resistance and outward appearance, completes the case production process.
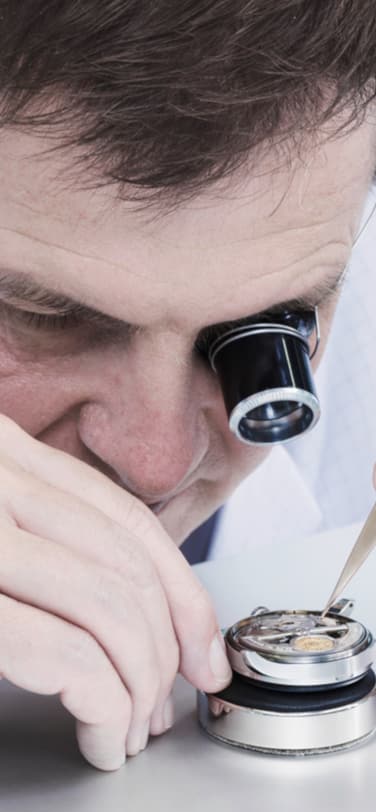
Dial, Hands and Casing Up
In these departments, all processes are manual. Depending on the model, specialists mount the dials on the fully timed and regulated movement by hand or using special tools. The same applies to the hands, which need to be set at exactly the right height and grip the pivot onto which they are firmly mounted. With chronographs, the zero position of the hands must also be absolutely exact. The movement is secured in position either to a casing ring or directly to the case. If the movement is gripped by a casing ring, the latter is held in position by a wave spring in the case back. The winding stems are individually adjusted. A special adhesive secures crowns that are screwed onto the winding stem.
Final Inspection
Over a period of ten days, the automatic movements in self-winding watches are rotated continuously, while those with manual winding are fully wound every other day. Running-in gives the wheels and pinions a chance to adapt to each other perfectly, while the lubricant penetrates into all the prescribed places.
The quality assurance process comes to a close with extensive final inspections. A watch’s suitability for everyday use is tested one last time by fully winding the movement, measuring its accuracy, checking the functions and appearance, and confirming its resistance to air and water. The quality of any product that leaves the company on the Rhine is beyond all doubt. This seamless quality assurance process is a guarantee for every future owner of an IWC watch that the company rigorously upholds its legendary quality standards.
Customization
Engraving makes IWC watches unique
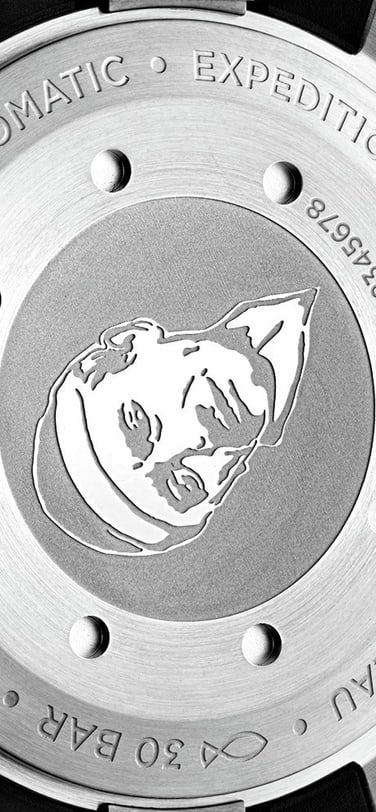
Every watch from IWC has its own personality, but there are often customers who want more and ask us to give their pocket or wristwatches a touch more individuality.
Thanks to modern engraving techniques, IWC offers a virtually unlimited range of options. Practically any request for specific changes to customize a watch can be executed to perfection. “Engraving” comes from the French word “graver” and originally meant “to plough a furrow”.
The carving of drawings, patterns, ornamentation or writing on wood, stone, ivory and metal creates attractive light and shade effects and is a means of immortalizing very personal ideas.
In this way, miniature works of art, such as the engravings on the back cover of the Aquatimer Chronograph Edition “Expedition Jacques-Yves Cousteau” or the Ingenieur Chronograph Silberpfeil, have been created for posterity. An IWC watch may also be made unique by the addition of engraved initials, a date, a family crest, a company logo or a personal dedication: the essence of individuality.
Service
Generations take pleasure in watches from IWC
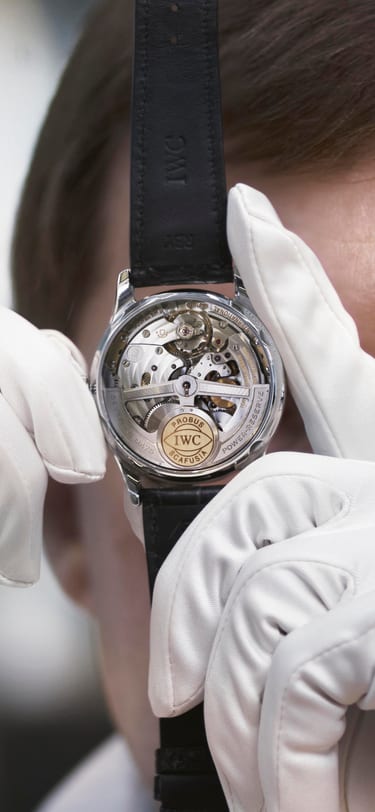
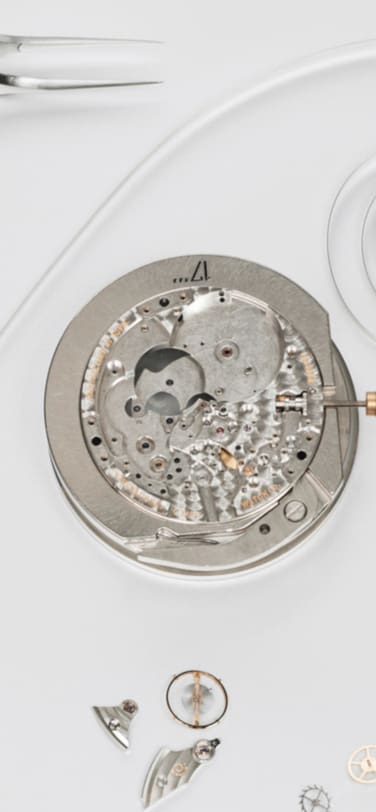
Maintenance and Service
In 25 countries around the world, over 200 watchmakers and service technicians have been dedicated to the maintenance and repair of IWC watches of every vintage since the company was founded in 1868. To ensure that no single detail is lost, IWC has maintained detailed records of every watch that has left the factory since 1885.
At the heart of the repairs department lies the spare parts store. This accommodates millions of meticulously ordered individual components. At IWC, the availability of original spare parts is crucial because they are essential if watches are to continue running for generations. Intervals between individual services vary considerably, depending on how and under what conditions the watch is used.
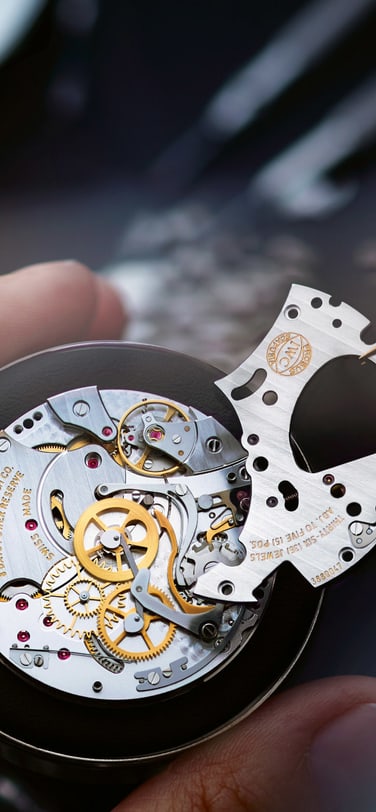
Complete Service
The complete service involves dismantling the movement piece by piece and cleaning the individual components. Specialists carefully examine every part of the movement and repair or replace worn or faulty parts. Subsequently, the watch is reassembled from scratch and, where necessary, oiled and lubricated.
Finally, the watch’s accuracy is tested and the movement is readjusted. The case is also completely dismantled. Scratches are repaired, case and strap components are ground or polished and the angles finished and then thoroughly cleaned. Before the watch is returned to the customer, it undergoes a final intensive testing phase that lasts several days. Only by going to these lengths can IWC guarantee that the watch will run accurately and remain water-resistant for years to come.
Every owner of an IWC watch can help to increase the useful service life of his timepiece. Tips and suggestions can be found on the company’s website at IWC.com and in the service brochure, “IWC service”, which can be obtained at IWC boutiques and IWC service centres, as well as from our authorized retailers.
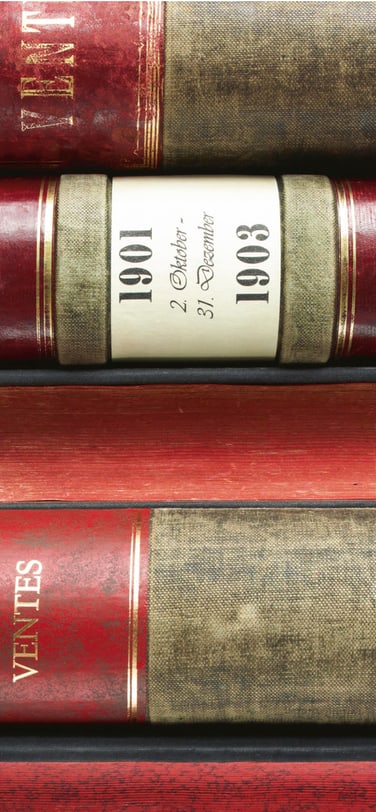
IWC’s Certificate
The story of every IWC watch begins in the workshop, where passionate watchmakers dedicate long hours to perfecting every detail. To make sure that it never loses track of a single watch, IWC began keeping records about them in 1885. All information is noted, including sale date, calibre, material and case numbers or reference numbers for newer models. Heirs and subsequent buyers have the option of obtaining precise information about their IWC watch for a fee, thus confirming its authenticity. This and further information is provided in the form of a certificate.
For a certificate to be issued, the watch must be taken to an IWC boutique or authorized retailer. In our workshop in Schaffhausen, the IWC timepiece is then subjected to careful, detailed testing by an experienced watchmaker.
Unfortunately, it is not possible to provide information about the collector’s value of specific models, because this depends on factors such as supply and demand as well as the condition of the movement and case.
In the event of a worst-case scenario involving loss or theft, it is advisable to report the incident in writing to the police and IWC. The case number, or the reference number for a newer model, in question is then entered in a special register, which ensures the watch is recognized if it is taken to an IWC service centre. This registration process has so far allowed many missing watches to be reunited with their rightful owners.