MONTRES DE SCHAFFHAUSEN
Chaque montre IWC est assemblée individuellement par nos maîtres horlogers. Ce sont eux qui grâce à leurs yeux experts, leurs doigts agiles et leurs instruments de précision assemblent plusieurs centaines de composants individuels pour créer des montres-bracelets d’exception – fascinante synthèse entre méticulosité, fonctionnalité et design exprimant la quintessence même de notre savoir-faire.
LA PHILOSOPHIE D’IWC
Schaffhausen constitue un îlot dans le paysage horloger helvétique, la plupart des fabricants étant établis en Suisse romande. Depuis 1868, cette spécificité géographique a favorisé le développement de la philosophie particulière de l’entreprise. Mettant clairement l’accent sur la technologie et le développement, la manufacture des bords du Rhin fabrique des garde-temps de précision et de valeur durable. Fort de sa passion pour l’innovation et l’inventivité technique, IWC Schaffhausen s’est forgé une réputation internationale. Étant l’un des leaders mondiaux dans le segment des montres de luxe, IWC fabrique des chefs-d’œuvre de Haute Horlogerie mariant ingénierie et précision dans un design exclusif. L’excellente réputation d’IWC repose surtout sur le savoir-faire de ses collaborateurs hautement qualifiés, maîtrisant parfaitement chaque étape du processus de production, ainsi que les mouvements et complications conçus par la manufacture, tels que la répétition minutes, le tourbillon ou encore le calendrier perpétuel. Pour les constructeurs et les designers d’IWC, le label de qualité « Probus Scafusia », « Produit éprouvé de Schaffhausen », représente depuis 1903 non seulement un énorme défi, mais aussi une passion sans limite.
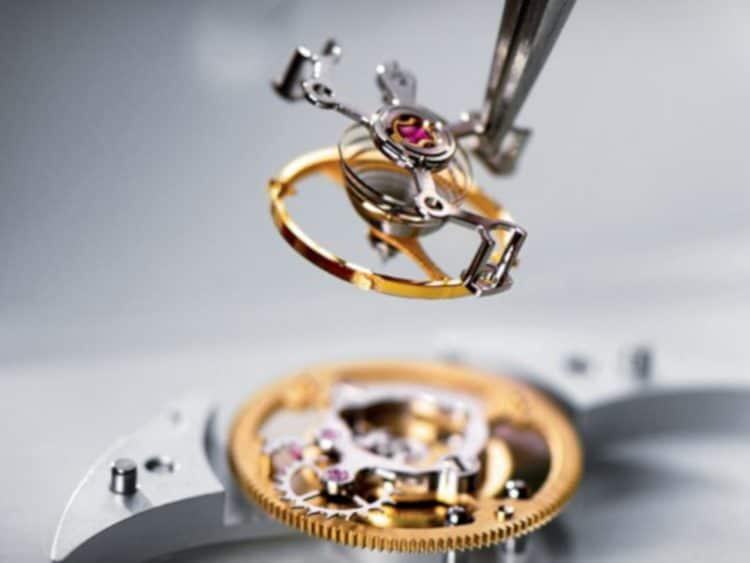
DÉVELOPPEMENT
AVANT QU’UNE MONTRE IWC FONCTIONNE POUR LA PREMIÈRE FOIS
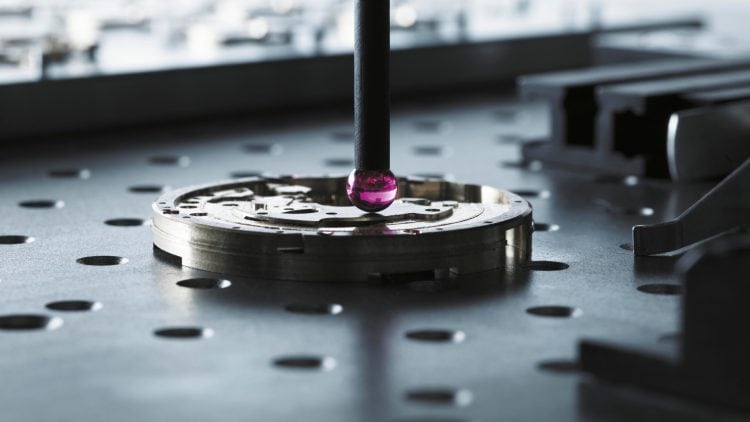
CONCEPTION ET ASSEMBLAGE
Lorsqu’IWC décide de développer un nouveau modèle, les designers et les ingénieurs horlogers commencent par se poser une question essentielle : quel est le résultat souhaité ? S’agit-il de battre un nouveau record de complexité ? S’agit-il d’optimiser un aspect en particulier comme la réserve de marche ou l’étanchéité ? En premier lieu, les composants principaux sont modélisés par ordinateur. Ici, IWC attache une grande importance aux technologies de production modernes lors des phases de conception. En collaboration étroite avec les ingénieurs, les designers jouent un rôle crucial pour harmoniser au mieux esthétique et fonctionnalité. Le choix du cadran, du bracelet, de l’affichage, des matériaux, des couleurs et du revêtement sont toujours le résultat logique d’un travail collectif. Outre les prouesses technologiques et le design attrayant du modèle, d’autres aspects plus affectifs, comme l’impression que la montre procure au poignet, entrent également en ligne de compte. Ainsi, la tranche du boîtier, le mécanisme d’activation du bouton-poussoir ou le son de la couronne ne sont jamais laissés au hasard. Les designers et ingénieurs horlogers s’inspirent souvent d’anciens dessins et croquis. Enfin, c’est le respect du travail des pionniers de la manufacture horlogère qui nous aide à perpétuer l’héritage de la marque de Schaffhausen.
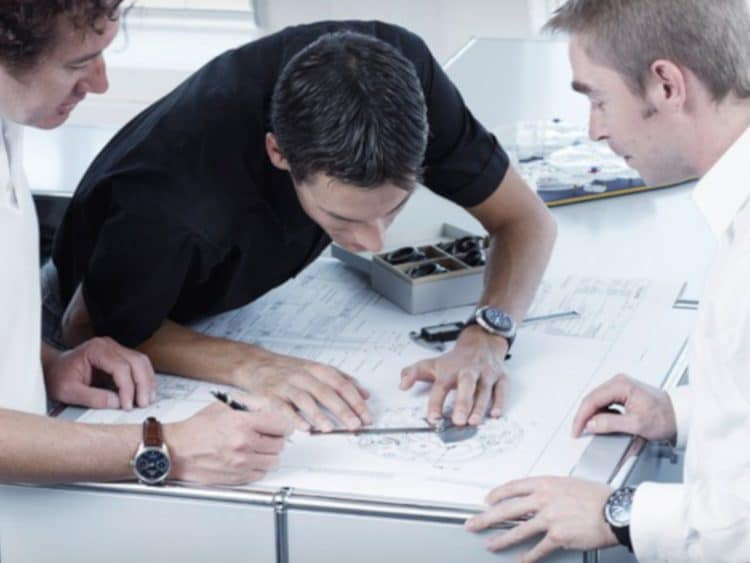
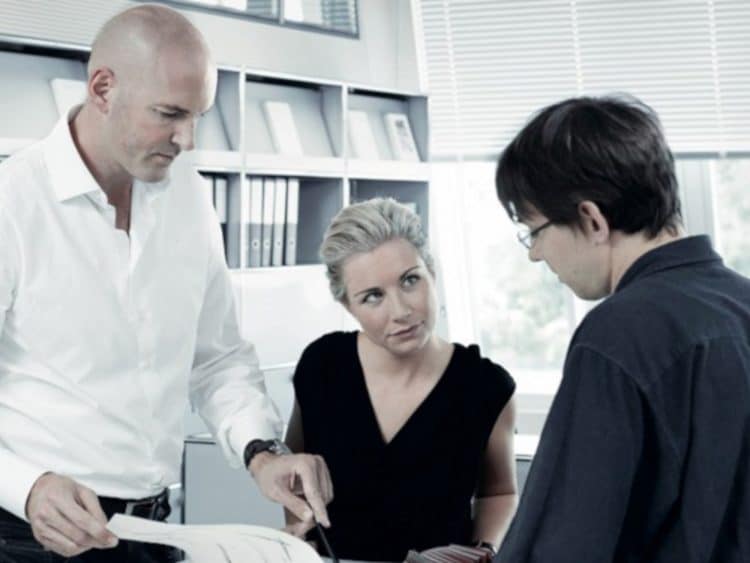
GESTION DE LA QUALITÉ
Grâce à un dispositif avancé de gestion de la qualité et du développement doublé d’un programme drastique de contrôle et de tests, IWC est en mesure de garantir un niveau de qualité de tout premier ordre. Nous utilisons des méthodes scientifiques telles que la simulation informatique en 3D, les analyses de matériaux par rayons X et de nombreux tests visant à évaluer le comportement des montres au quotidien ou dans des conditions extrêmes. Le recours aux caméras ultra-rapides et aux instruments de mesure laser nous permet de déceler les mouvements les plus infimes, tandis que nos logiciels de pointe calculent les contraintes maximales pouvant être exercées sur les composants.
Dès les phases initiales de développement, les roues, arbres et profils de dentures, sans oublier les dimensions des ressorts, sont contrôlés pour identifier toute erreur en amont. IWC appelle cela le « processus d’analyse des sources d’erreur ». Les développeurs s’appuient sur l’expérience acquise dans le cadre de projets antérieurs et tiennent compte des commentaires du marché et des diverses suggestions pour garantir que chaque montre IWC continuera de fonctionner pendant de nombreuses années et pourra être réparée plus facilement le cas échéant.
TESTS
LE LONG CHEMIN DU PROTOTYPE AU PRODUIT FINI
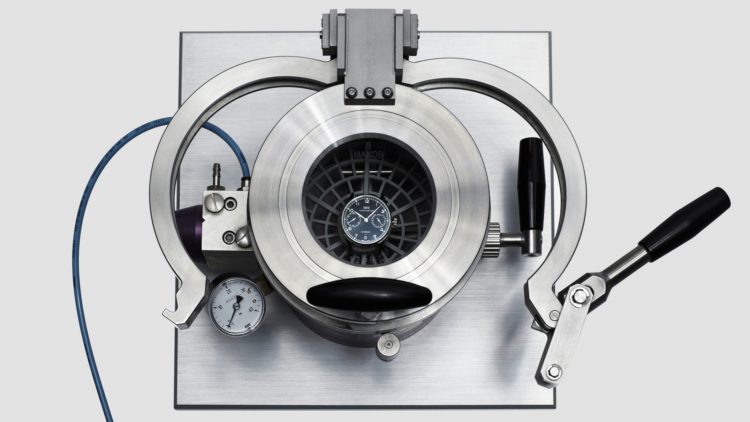
QUALIFICATION ET HOMOLOGATION
La qualification couvre un programme de plusieurs mois au cours duquel sont effectués plus de 30 tests de précision pour les nouvelles montres au stade de prototype ou, plus tard, lors de l’homologation de la série zéro. Sous forme concentrée, les tests simulent tout ce qui peut arriver, en situation normale ou exceptionnelle, au cours de la longue vie d’une montre. Ce n’est que lorsque plusieurs prototypes et une production zéro de la montre ont réussi les tests rigoureux qu’IWC commercialise une montre et enrichit sa légende d’un nouveau chapitre fascinant.
TESTS DE CORROSION ET D’UV
Pendant deux semaines, la montre est plongée dans une solution saline à 37 degrés Celsius afin de s’assurer que les matériaux sélectionnés ne seront pas soumis à la corrosion lors de leur utilisation quotidienne ou lorsqu’ils seront immergés dans l’eau salée. Exposés à de puissants rayons ultraviolets pendant plusieurs jours, les cadrans ne doivent subir aucun changement de couleur.
TESTS D’USURE
Pour mener à bien les tests, certains composants particulièrement exposés à l’usure sont fabriqués dès la phase de conception afin de déterminer leurs spécifications requises. La lunette tournante de l’Aquatimer, par exemple, est soumise à un test de durée équivalent à quatre plongées par jour, de manière à garantir une durée de vue minimum de 10 ans. Les lunettes tournantes des montres de plongée IWC doivent également prouver leur fiabilité en eaux souillées. Au stand de test, les boutons-poussoirs du chronographe sont sollicités de 10 000 à 20 000 fois pour évaluer leur résistance à l’usure.
TESTS CLIMATIQUES
Lors des tests climatiques, tout le spectre des conditions thermiques pouvant être rencontrées par l’utilisateur est testé de manière systématique. Géographiquement parlant, ce test reproduit les températures allant de l’Alaska au Sahara en passant par la forêt amazonienne brésilienne. Pendant plusieurs jours, voire plusieurs semaines, les montres sont placées dans une armoire climatique où elles doivent résister à des températures allant de -20 à +70 degrés Celsius et jusqu’à 95 % d’humidité relative. C’est ensuite le fonctionnement à long terme de la montre qui est examiné avec attention. Un microphone automatique multicouche est utilisé pour vérifier la régularité des alternances.
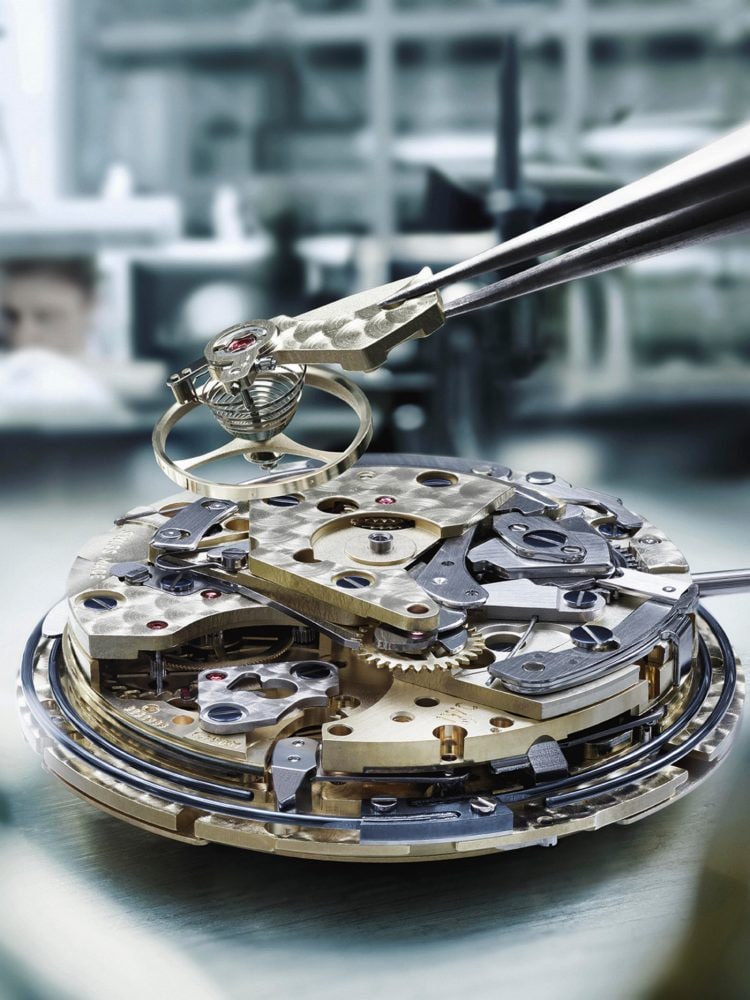
ASSEMBLAGE
CHEZ IWC, HAUTE TECHNOLOGIE ET ARTISANAT NE SONT PAS DES NOTIONS CONTRADICTOIRES
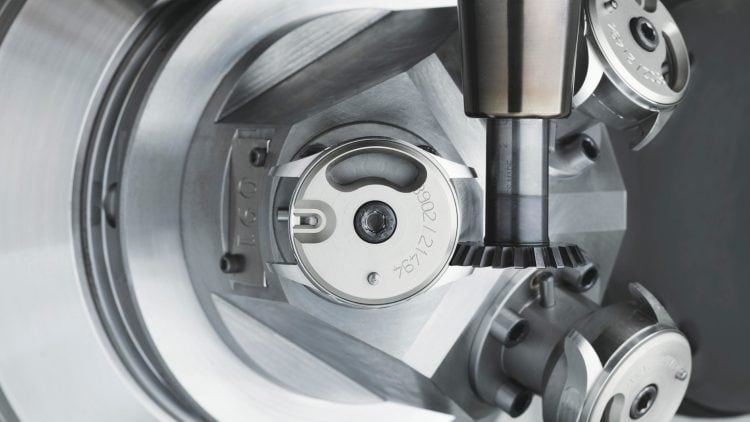
TECHNIQUES DE PRODUCTION
Durant la phase de fabrication des composants, les découpes sont réalisées au moyen de fraiseuses CNC. Après traitement des surfaces, la tolérance des composants n’est généralement que de +/- 0,02 millimètre, mais peut se limiter dans certains cas à +/- 0,002 millimètre. Après usinage, les composants sont finis manuellement ou sont traités par une machine d’usinage par étincelage (EDM). Ces machines à électroérosion CNC servent principalement à usiner certaines parties du mouvement. Les tolérances pour la rugosité de la surface peuvent atteindre 0,005 millimètre – jusqu’à 0,001 millimètre au moyen de l’EDM.
ASSEMBLAGE DU MOUVEMENT
L’assemblage du mouvement passe par le montage successif du remontoir, du rouage et de l’échappement, suivi du réglage précis de la montre. Selon le modèle, on assemble le mécanisme de remontage automatique ou celui du chronographe, ainsi que le compteur du calendrier et des heures. La part la plus complexe de ces opérations consiste à ajuster l’échappement ainsi que l’enroulement et le déroulement du spiral pour assurer leur bon fonctionnement : une tâche manuelle de haute précision qu’aucune machine ne peut réaliser, même télécommandée, avec la haute qualité attendue. À chaque étape du montage, on vérifie et corrige en permanence les fonctions et les réglages de précision. Ensuite, dans le département des complications, des horlogers hautement qualifiés intègrent au mouvement de base des complications telles que le calendrier perpétuel et le mécanisme de la rattrapante. Les mouvements avec tourbillon et répétition minutes sont entièrement montés dans le département des spécialités, où ils passent par les étapes de prémontage et de montage, et subissent l’ensemble des réglages de précision avant d’être emboîtés.
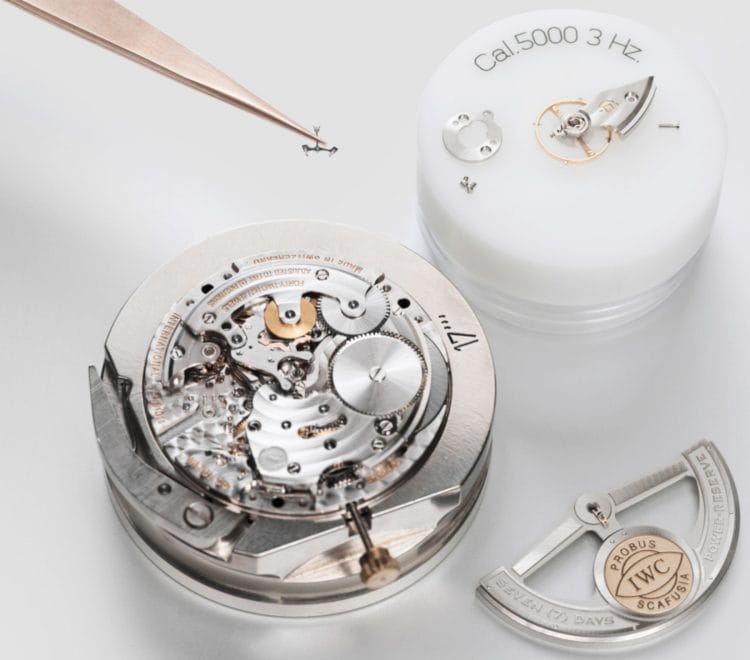
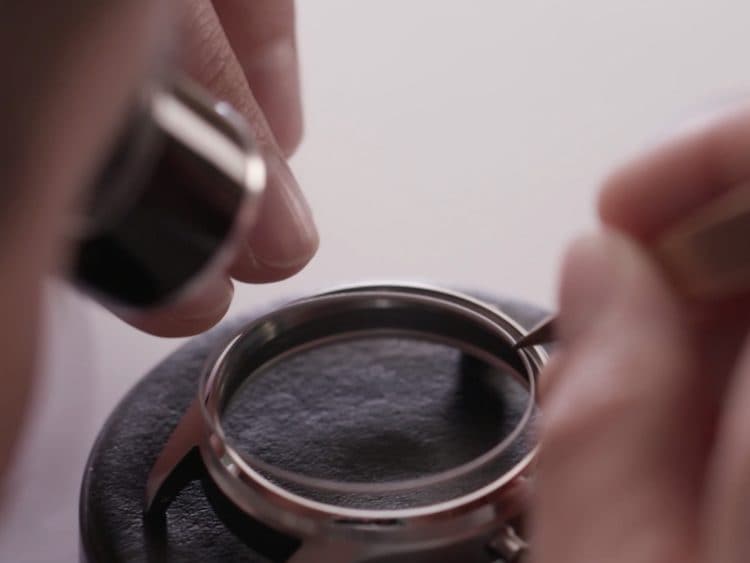
USINAGE ET MONTAGE DES BOÎTIERS
S’agissant de la précision et du temps de travail requis, l’usinage des boîtiers n’a rien à envier aux autres étapes de fabrication. Pour les montres en métal précieux, les éléments des boîtiers sont fabriqués à partir de pièces brutes préformées. Les boîtiers en acier fin et en titane sont fabriqués à partir de barres produites spécialement pour IWC et travaillées sur des tours et fraiseuses CNC à un centième de millimètre près. Sur les centres de fraisage, on ajuste les cornes des bracelets et on perce les cercles d’emboîtage accueillant les boutons-poussoirs et la couronne dans les anneaux du mouvement. C’est là également que sont élaborés les surfaces de forme libre, par exemple les boîtiers des montres Ingenieur. Après le processus de découpe, les dimensions sont scrupuleusement contrôlées et les surfaces sont travaillées à la main pour satisfaire aux normes de qualité IWC. Les arêtes sont arrondies, anglées ou facettées, tandis que les traces de fraisage, de rondage ou d’usinage sont éliminées, et les surfaces meulées, polies, satinées ou sablées. Il est temps maintenant pour les spécialistes d’ajouter des ornements à certains éléments du boîtier – un perlage par exemple – même si ceux-ci ne se voient pas de l’extérieur. Le processus de fabrication du boîtier s’achève par de nombreux tests complexes, notamment la vérification de son étanchéité et des contrôles esthétiques.
CADRAN, AIGUILLES ET MONTAGE
Dans ces départements, toutes les opérations sont effectuées manuellement. En fonction du modèle, les spécialistes montent les cadrans à la main ou au moyen d’instruments spécifiques sur les mouvements préalablement réglés. Même méthode pour les aiguilles, qui doivent être fixées exactement à la bonne hauteur et s’enchâsser sur l’axe des aiguilles autour duquel elles tourneront. Sur les chronographes, la position zéro des aiguilles doit être absolument exacte. Le mouvement vient s’insérer dans l’anneau du mouvement ou directement sur le boîtier. Si le mouvement est inséré dans l’anneau, ce dernier doit être maintenu en position grâce à un ressort ondulé situé sur le fond du boîtier. Les tiges de remontoir sont réglées séparément. Un adhésif spécial renforce les couronnes vissées sur les tiges de remontoir.
INSPECTION FINALE
Les montres équipées de mouvements automatiques sont retournées pendant dix jours tandis que les montres à remontage manuel sont remontées un jour sur deux. Cette phase de rodage permet aux roues et aux pignons de s’adapter parfaitement les uns aux autres et au fluide lubrifiant de se diffuser entre les rouages.
Le processus de contrôle qualité s’achève avec une inspection finale exhaustive. L’adaptation d’une montre à un usage quotidien est vérifiée une dernière fois avant sa mise en vente : le mouvement est entièrement remonté, sa précision est mesurée, ses fonctions et son apparence sont vérifiées et sa résistance à l’air et à l’eau est validée lors d’une série de tests spécifiques. La qualité de tout produit quittant notre manufacture ne fait plus aucun doute. Grâce à ce processus de contrôle qualité absolument infaillible, chaque futur propriétaire d’une montre IWC est certain que la marque reste à la hauteur de sa réputation légendaire.
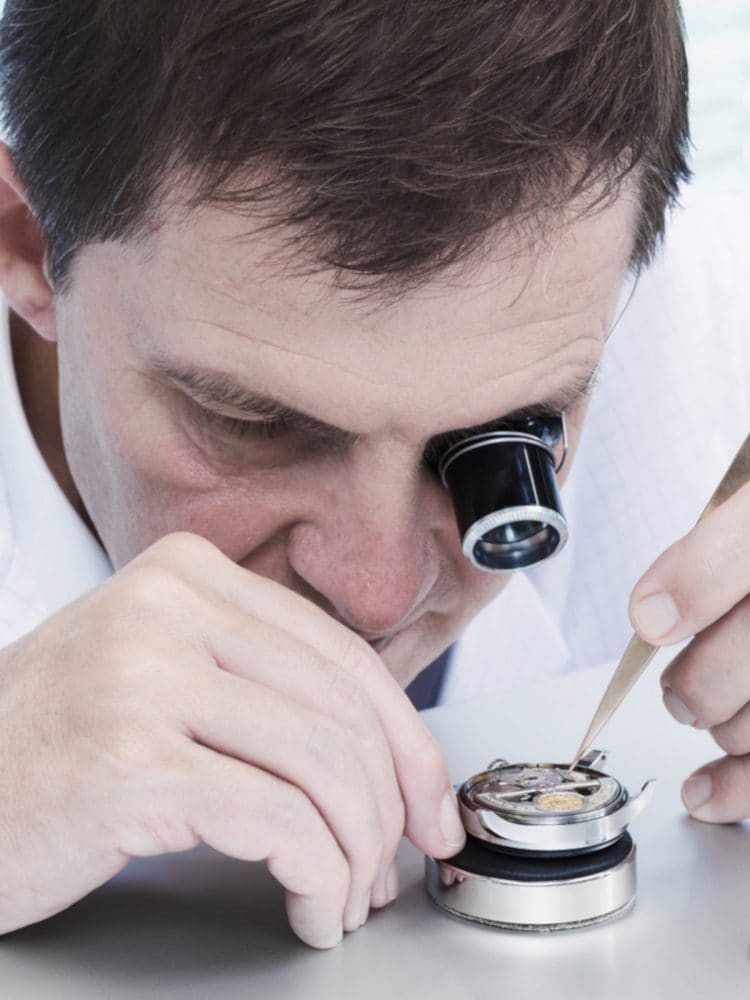
PERSONNALISATION
UNE TECHNIQUE DE GRAVURE QUI REND UNIQUE CHAQUE MONTRE IWC
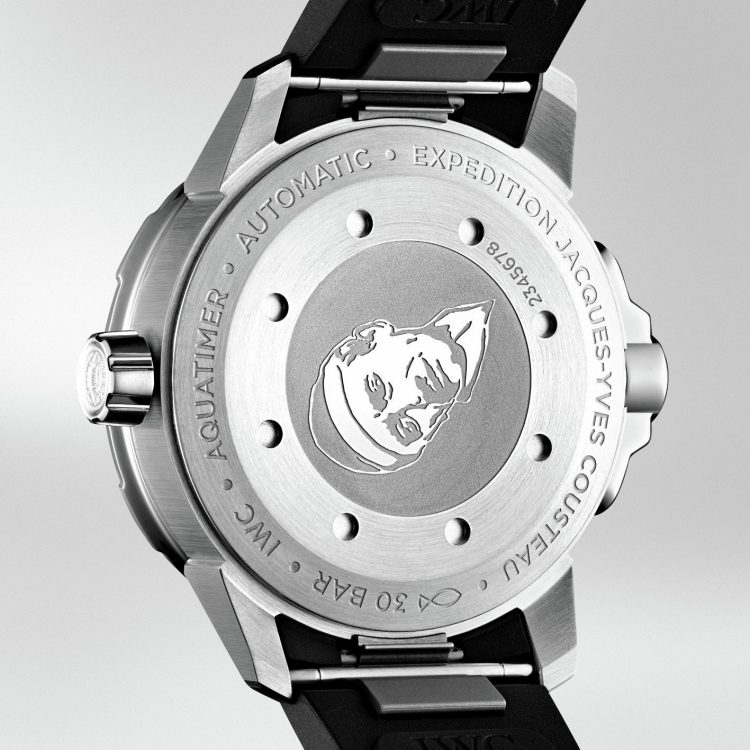
Chaque montre signée IWC possède déjà un caractère unique. Néanmoins, cela ne suffit pas à certains amateurs qui nous demandent d’ajouter une touche encore plus personnelle à leur montre de poche ou à leur montre-bracelet.
Grâce aux techniques de gravure modernes, l’éventail de possibilités offertes par IWC dans ce domaine est pratiquement illimité. Pratiquement toutes les demandes de changement pour personnaliser une montre peuvent être exécutées à la perfection. Le mot « graver » signifie à l’origine « faire une raie dans les cheveux ».
Les dessins, motifs, arabesques et textes façonnés sur le bois, la pierre, l’ivoire et le métal créent de séduisants jeux d’ombre et de lumières permettant d’immortaliser des idées très personnelles.
Ainsi, des œuvres d’art miniatures, telles que les gravures présentes sur le fond de l’Aquatimer Chronographe Edition « Expedition Jacques-Yves Cousteau » ou l’Ingenieur Chronographe Silberpfeil, resteront dans les annales. Une montre IWC peut également être personnalisée par la gravure d’initiales, d’une date, d’armoiries familiales, d’un logo d’entreprise ou d’une dédicace personnelle : l’essence de l’individualité.
ENTRETIEN
LES MONTRES IWC RAVIRONT PLUSIEURS GÉNÉRATIONS D’UTILISATEURS
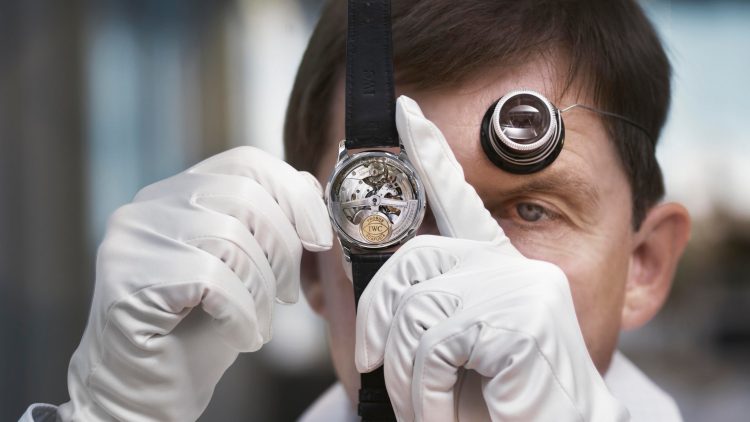
ENTRETIEN ET SERVICE
Depuis la fondation de l’entreprise en 1868, pas moins de 200 horlogers et techniciens de service répartis dans 25 pays à travers le monde se sont consacrés à l’entretien et à la réparation des montres IWC de toutes générations. Pour qu’aucun détail ne leur échappe, les données de toutes les montres fabriquées depuis 1885 sont répertoriées dans les registres d’origine de la manufacture.
Le magasin des pièces détachées est le cœur du service de réparation. C’est là que sont rangés avec un soin scrupuleux plusieurs millions de composants individuels. IWC accorde une grande priorité à la disponibilité des pièces de rechange d’origine, parce qu’il est essentiel qu’une montre puisse être maintenue en état de marche pendant plusieurs générations. L’intervalle entre les services d’entretien dépend de la manière dont la montre est utilisée et sollicitée. La fréquence des entretiens varie considérablement en fonction de l’utilisation de la montre et des conditions dans lesquelles elle fonctionne.
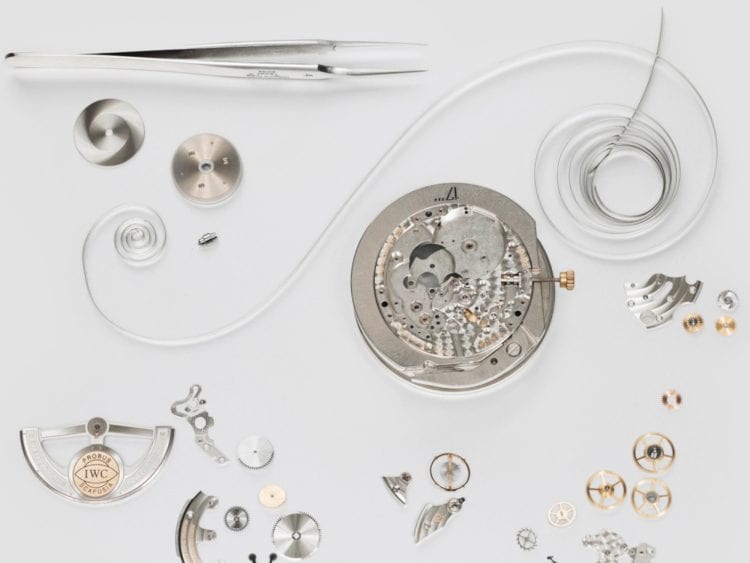
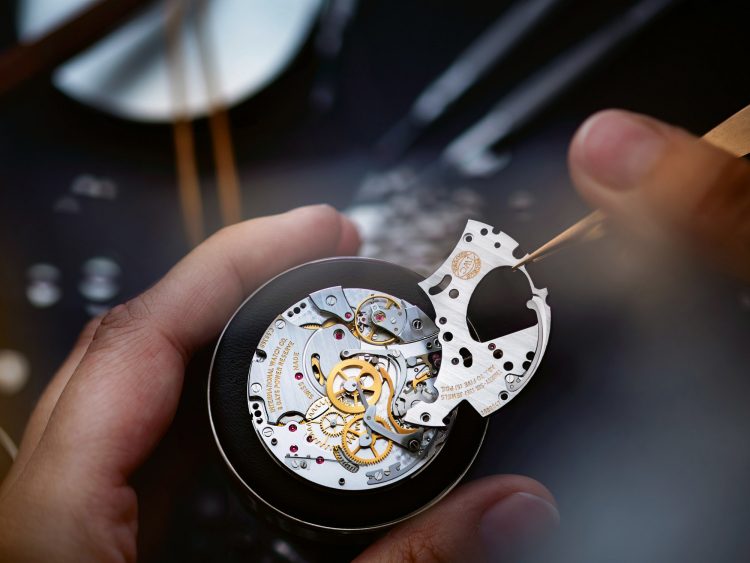
ENTRETIEN COMPLET
Lors de l’entretien complet, le mouvement est entièrement démonté et chaque composant est nettoyé. Les spécialistes contrôlent minutieusement chacune des pièces et réparent ou remplacent si nécessaire les composants usés ou défectueux. Ensuite, le mouvement est entièrement remonté, huilé et graissé là où c’est nécessaire.
Enfin, la précision de marche est vérifiée et réglée. Le boîtier est également entièrement démonté avant de procéder à l’élimination des rayures, au meulage ou au lapidage, au polissage des pièces du boîtier et des composants du bracelet puis, finalement, à leur nettoyage minutieux. Avant que la montre complètement révisée ne soit rendue au client, elle est soumise à un dernier programme de tests intensifs de plusieurs jours. C’est la seule façon de garantir une excellente précision de marche et une parfaite étanchéité pour de longues années encore.
Chaque propriétaire d’une montre IWC peut lui-même contribuer à en augmenter la durée de vie. Des consignes à cet effet figurent sur le site IWC.com et dans la brochure « Le service IWC » que l’on peut obtenir dans les boutiques IWC, les centres de service IWC et chez les partenaires de vente autorisés.
CERTIFICAT IWC
L’histoire de chaque montre IWC commence dans la manufacture, où des horlogers passionnés consacrent de nombreuses heures au moindre détail. Pour ne jamais perdre la trace de ces garde-temps, IWC a ainsi commencé dès 1885 à les répertorier dans un registre où sont consignées toutes les données telles que la date de vente, le calibre, le matériau, le numéro du boîtier et, pour les modèles plus récents, le numéro de référence. Les héritiers ou les acheteurs ultérieurs ont ainsi la possibilité d’obtenir, moyennant participation aux frais, des renseignements détaillés sur leur montre IWC ainsi que la confirmation de son authenticité. Ces informations, ainsi que d’autres renseignements, sont délivrées sous la forme d’un certificat.
Pour l’obtention du certificat, il est nécessaire de remettre la montre auprès d’une boutique IWC ou d’un dépositaire. Le garde-temps sera alors soumis à un contrôle minutieux et détaillé réalisé par un horloger chevronné dans notre manufacture à Schaffhausen.
Malheureusement, il n’est pas possible de donner des informations quant à la valeur marchande d’un modèle de collection spécifique, car les prix dépendent des facteurs fluctuants que sont l’offre et la demande, ainsi que de l’état du mouvement et du boîtier.
Si vous deviez faire la pénible expérience de perdre votre montre IWC ou de vous la faire voler, nous vous conseillons de déclarer immédiatement cette perte par écrit à la police et à IWC. Le numéro du boîtier et, pour les modèles plus récents, le numéro de référence seront notés dans un registre afin que la montre puisse être identifiée si elle devait réapparaître dans un centre de service IWC. Cet enregistrement a déjà permis de restituer à leurs propriétaires légitimes de nombreux garde-temps portés disparus.
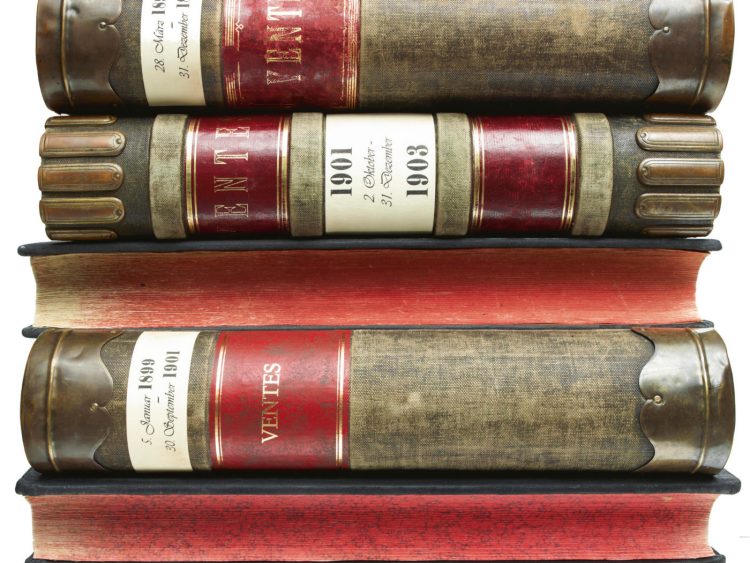