A powerful sports car engine and a mechanical watch have at least one thing in common: both need lubricants to protect moving parts against wear and tear. Depending on the stresses and strains to which they are exposed, around 50 points in the movement are treated with oils and greases developed especially for use in wristwatches.
A mechanical watch is a complex miniature machine that is constantly in motion: in the space of just a few cubic centimetres, as many as several hundred individual parts, including springs and gears, toil away ceaselessly. And in one important respect, a timepiece is no different than a sports car: “Without oil, a car or watch would grind to a halt in no time,” is how Hansjörg Kittlas, head of assembly of special movements at IWC Schaffhausen, describes the problem.
A watch movement contains dozens of moving parts that constantly rub against each other. The resulting abrasion can cause minuscule particles to break off and block up the precision mechanics. In a high-performance car, motor oil protects the engine against wear and tear. A watch’s high-precision mechanical movement likewise needs lubrication in about 50 places: in the bearings, for instance, where the wheel pivots turn. The mainspring in the barrel, the winding mechanism and the escapement also need oiling. If the watch features additional complications, such as a perpetual calendar, the number of lubrication points can quickly treble.
A millionth of a litre of lubricant is enough for a complete movement
Particularly in the case of exclusive and complicated models, lubrication calls for a great deal of patience, manual dexterity and experience. The wire tip of the oil dispenser that Hansjörg Kittlas carefully introduces into a small container is less than 0.1 millimetres thick. With a steady hand, he deposits a drop of oil into the recess of a bearing jewel on the IWC-manufactured 94900 calibre. The drop is so tiny as to be virtually invisible to the naked eye. A single thousandth of a millilitre is enough to lubricate the entire watch movement. A fast sports car, on the other hand, gobbles up engine oil by the litre.
In another respect, too, a watch movement differs starkly from a car engine. While the engine speed of a performance car driven to the limit can top 8000 rpm, a watch movement is much more leisurely. The fastest-moving gear, the escape wheel, revolves at a rate of just 20 times per minute. “The speed may be relatively low, but the surface pressures are extremely high,” is how Kittlas describes the conditions in a wristwatch. It’s rather like a woman’s stilettos: the more pointed the heels, the deeper the impressions they leave in your parquet floor. The load exerted on bearings by pivots that are often just a few tenths of a millimetre thick is equally extreme.
The special conditions demand that a watch oil has to satisfy a number of equally special criteria. Up until the end of the first quarter of the last century, the lubricant of choice was neat’s-foot oil, which is extracted by boiling the fat glands in the feet of cattle. Its main disadvantage is that it rapidly deteriorates with age. A little over 50 years ago, the speciality chemical industry started developing synthetic watch oils with specific properties. Expensive high-tech products like these do not thicken or evaporate, even after long periods of time, and are resistant to both corrosion and oxidation.
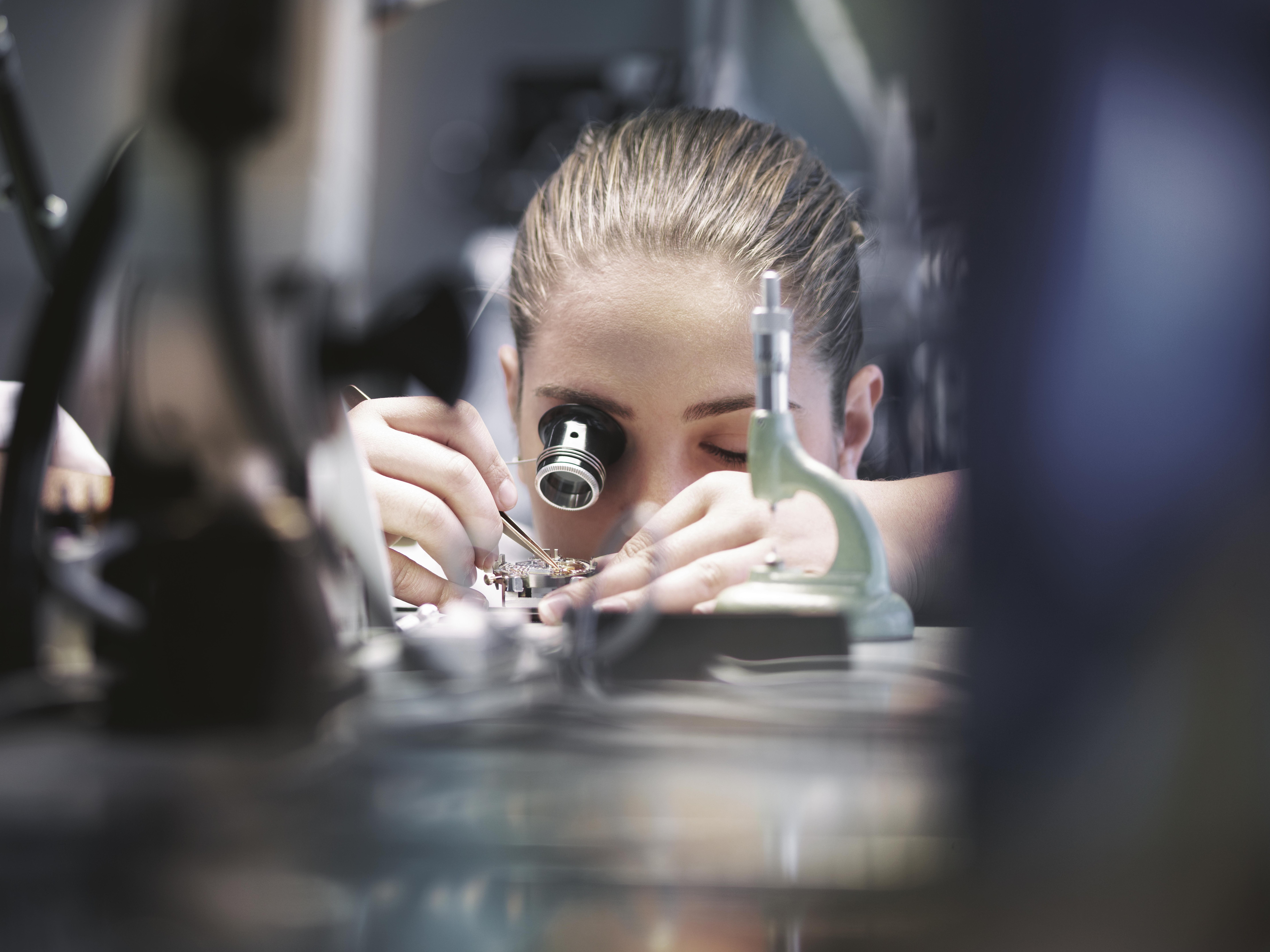
Without oil, a car or watch would grind to a halt in no time
Half a dozen lubricants with specific properties
In practice today, watchmaking calls for around half a dozen different oils and greases that are suitable for clearly defined purposes. From the barrel to approximately the centre wheel, where movements are slow and forces considerable, the oils used are relatively viscous and create a stable film of lubricant that is resistant to high pressure. The further we move from the mainspring, the greater the speeds and the smaller the forces exerted. The fourth wheel and the escape wheel, for instance, need a thinner oil that will allow the movement to run as freely as possible.
Another factor that helps determine the optimum lubricant is the material used. For example, it makes a difference whether a steel pivot rotates in a bearing made of brass or a synthetic jewel. It is also important that the tiny drops of oil do not spread and penetrate other parts of the movement. This is prevented using an epilame coating. This special surface treatment for lubrication points creates an oil-resistant film that keeps the oil where it belongs.
Probably the trickiest part of the process is lubricating the escapement. A tiny amount of grease is applied to about three teeth on the escape wheel. From here, it makes its way to the two pallet stones and is then evenly distributed over all the teeth on the escape wheel. The lever escapement is one of the most severely tested sub-assemblies in the entire watch, and an intact film of oil is vital for high precision.
AUTOMATIC LUBRICATION BOOSTS QUALITY
It is extremely difficult for a human being to carry out this job with a consistently high degree of reliability. “Gradual automation of the lubrication process has enabled us to improve the quality considerably,” explains Markus Bühler, who is responsible for Industrialization at IWC in Schaffhausen. A major step forward was achieved with the pneumatic oil dispenser, which makes it possible to apply drops of lubricant that are precisely the same size. Today, special robots apply oil to over 20 lubrication points simultaneously and guarantee consistently high quality standards. Today, even lubrication of the escapement, which is critical, is partly automated.
In future, it will be possible to shoot lubricant completely contact-free from short distances into the intended place. Most people will be familiar with the jet technology used here because it is the same as in their inkjet printers at home.
There are also high expectations for diamond-like carbon coatings: ultra-thin, extremely hard coatings on the surfaces of moving parts can reduce friction so dramatically that lubricants are no longer required. However, the process has failed to produce satisfactory results so far because of the tiny dimensions of the parts to be coated.
This means that today there is still no real alternative to torough lubrication. But even the best-quality watch oil comes to the end of its powers at some point. Tiny particles create impurities. So, like a sports car, a mechanical watch also needs a regular oil change. But while the car has to go the garage once a year, a wristwatch can go on functioning faultlessly for much longer. Only after five years will a watchmaker need to dismantle the movement and carefully clean the parts to remove particles of dirt and oil residues. Finally, he will reassemble the precision mechanism and lubricate it exactly as required, and thus ensure that it goes on performing faultlessly and showing the time reliably for the next five years.
In practice today, watchmaking calls for around half a dozen different oils and greases
Continue reading
When a complication is grande
IWC’s Grande Complication watches, especially the Portugieser Grande Complication, represent the pinnacle of traditional watchmaking. Find out more.
The Dream of Flying
Numerous special editions of IWC’s legendary Pilot’s Watches have been sold, with part of the proceeds going to the Antoine De Saint-Exupéry Youth Foundation and its partner organizations.
IWC Schaffhausen
Description
