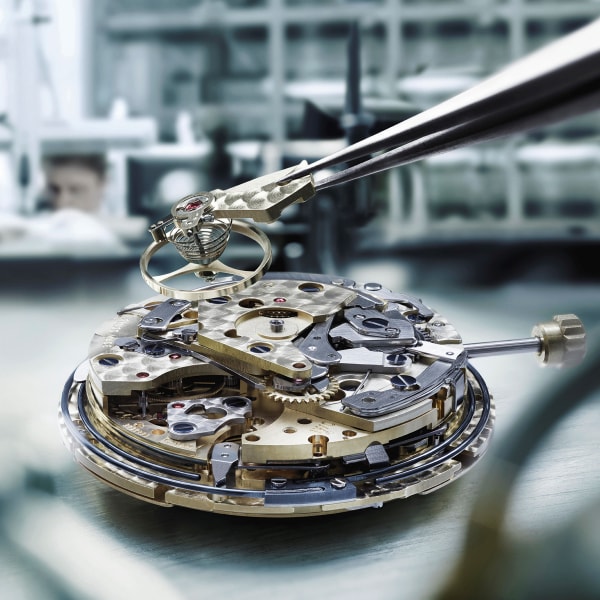
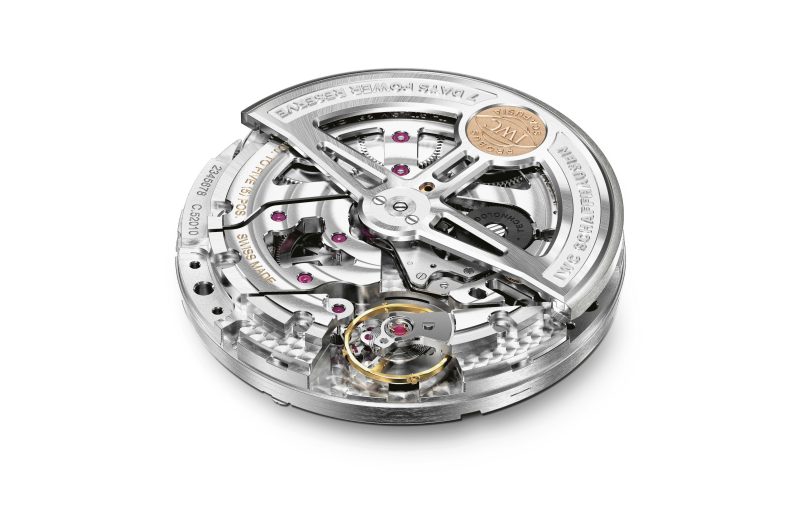
The Journal
Pellaton’s ingenious automatic meets state of the art engineering
Shipping and delivery conditions
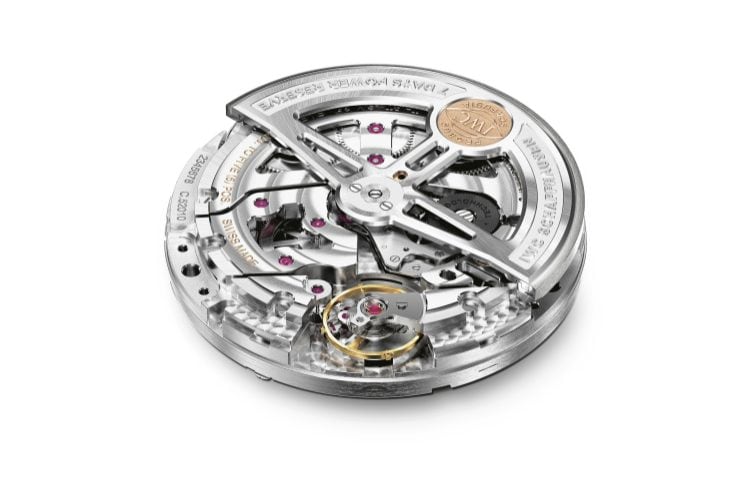
An automatic watch keeps running only because of the movements of the wearer’s arm. For 60 years now, the power driving IWC’s automatic in-house movements has come from the pawl-winding system developed by Albert Pellaton and improved continuously ever since. In the new 52000-calibre family, state-of-the-art ceramic technology has made the movement practically wear-free.
These days, people don’t leave home without first charging their smartphones, tablets or laptops. In this digital age, mechanical watches with automatic winding are even more of an anachronism.
Even without a battery, they seem to go on running forever. Of course, the watch that never stops is not some kind of miraculous perpetual motion machine. It, too, needs a source of energy to keep its hands moving. In this case, however, its mainspring is not manually wound via the crown but, almost incidentally, by the movements of the wearer’s arm. “In an automatic watch, the rotor converts kinetic energy into potential energy for the spring,” is how Thomas Gäumann, head of in-house movement development at IWC, describes the principle behind the function.
—The half moon-shaped rotor converts the wearer's kinetic energy into potential energy for the mainspring
GRAVITY FORCES THE ROTOR TO MOVE DOWNWARD
It is all made possible by gravity and inertia. The centrally bearing-mounted rotor is a semicircular segment made of brass, whose outer edge consists of a heavy metal such as tungsten. In view of the positional error, gravity continuously forces the rotor to move downwards. Even the slightest change in its horizontal position causes it to turn. And then there is inertia: If the watch case is accelerated at a certain angle, the rotor initially remains motionless but then generates even greater torque at the centre. The torque transmitted to the barrel via a reducing gear, where it winds the mainspring. The mechanism is particularly efficient when the wearer’s arm moves relative to his body when walking.
The automatic sub-assembly is exposed to more wear and tear than most other parts in the movement
THE PAWL-WINDING SYSTEM MAKES USE OF EVERY SINGLE MOVEMENT
At IWC, the automatic system is inseparably linked with Albert Pellaton. The scion of a watchmaking family from Le Locle, he was appointed Technical Director to the Schaffhausen-based company in 1944 and made the development of an efficient automatic winding system his top priority. “From a design point of view, the difficulty lay in converting the rotor’s bidirectional movements into a unidirectional winding motion that would put the mainspring under tension,” says Gäumann, describing the initial situation. Most systems back then either diverted the rotor’s movements to a complicated transmission or used only rotations in only one direction to wind the movement. The resulting power and energy losses were considerable.
Pellaton hit upon a surprising solution: instead of putting a ball bearing or cog at the centre of the rotor, he used a heart-shaped, eccentrically bearing-mounted disc. The latter converts the rotor’s revolutions into the to-and-fro movements of a rocking bar. The bar’s rocking movements are then transmitted to the winding wheel by two pawls: while one of them pulls the wheel (i.e. winds it), the other glides smoothly over the top of it until the roles are reversed. The mechanism patented in 1950 is unusually efficient. “The rotor’s smallest movement in either direction is used to wind the mainspring,” explains Gäumann.
Even if the principle is simple enough, an automatic winding system poses many different challenges for the design engineers. On the one hand, the mechanism must function perfectly for a wide range of wearers with different habits and lifestyles. On the other, the automatic sub-assembly is exposed to more wear and tear than most other parts in the movement. In the new 52850 calibre, for instance, the rotor has to complete 2600 revolutions to fully wind the two barrels in the Portugieser Annual Calendar. Although the rotor weighs just less than five grams, the forces exerted on the components during rapid movements may be as much as 5000 times that of gravity. Protecting the oscillating system against wear and tear, therefore, merits special attention.
— Pellaton's automatic system uses movements of the rotor in both directions to wind the mainspring.
— Albert Pellaton
CERAMIC PROTECTS THE MECHANISM AGAINST WEAR AND TEAR
Apart from a sophisticated mechanism, the material chosen is also crucial. Technical ceramics, as the kind used in watch movements are known, are lighter and harder than steel and extremely resilient. IWC can look back on almost 30 years’ experience in working these materials. As in the manufacture of watch cases many years ago, the company has assumed a leading role in the industry in the use of ceramics for movement components.
The manufacture of very small ceramic parts within the prescribed tolerances, however, is extremely demanding because the basic raw material in powder form shrinks by around a third during the sintering stage. Only very few specialists master the highly complex manufacturing process. On top of this, design or geometrical modifications are usually needed in order to produce a brass or steel component in the high-tech material.
In view of the stresses and strains that affect it, the Pellaton winding system was a candidate for the use of ceramic from an early stage. IWC succeeded in producing the 51900 calibre – the driving force in the Portugieser Tourbillon Mystère Rétrograde – in zirconium oxide rather than copper beryllium for the first time in 2009. This improvement alone played a major role in reducing wear and tear. It seemed obvious that the next step should be to manufacture the winding wheel in this material. However, initial attempts failed: when the steel pinion was press-fitted, the ceramic wheel regularly shattered. The breakthrough came only after a new design and progress in the manufacturing technology. Now, for the 52000-calibre family, the automatic wheel and the pinion are produced together as a single, integrated component in black ceramic. “As a result, the interaction between the pawls and the wheel is now virtually wear-and-tear-free,” says Gäumann.
THE MATERIAL USED FOR THE CAM IS ALSO THE BEARING
But there was still more room for improvement. In the past, for instance, the cam for the Pellaton winding system was made of steel, at the middle of which a ruby jewel was pressed-fitted into position. However, this design called for an additional bearing for the rotor. Here, too, the use of ceramic brought a surprising solution. “Today, the cam is made entirely of white ceramic and thus serves simultaneously as the bearing for the entire rotor,” explains Gäumann. This modification saves space and has enabled the design engineers to make the rotor staff larger and to manage without a spring-mounted bearing for the entire sub-assembly. Mounting it on a firmly fixed bridge has made the automatic winding mechanism even more robust.
Pallaton’s solution, patented 60 years ago, is still modern today
“The Pellaton winding system is a unique piece of technology and takes its place in our company’s watchmaking legacy along with the perpetual calendar from Kurt Klaus and the Portugieser Minute Repeater,” says Gäumann. Then again, it is part of IWC’s ongoing tradition to rethink existing ideas. The improvements made to the 50000-calibre family may have been restricted to a few details. But it was only made possible by long years of intensive cooperation between watchmakers, design engineers and material specialists. When owners observe the new in-house movements through the sapphire glass back cover, they will not only be able to admire the optical perfection of the modified winding system. They will also be reminded daily of the passion with which the engineering philosophy of IWC founder Florentine Ariosto Jones is still pursued in Schaffhausen.