You have to seek him out on the factory floor, if you want to speak to Andrea Santoni. The company founder is standing in the packing department, wearing a white coat. He carefully lays pairs of black ladies’ boots on grey silk paper. Instinctively, he runs a final, critical eye over the leather and seams. Only a perfect shoe can bear the name of Santoni. “We didn’t make our name with a brand, but with quality,” explains Signor Santoni.
Andrea Santoni, 72, and his son Giuseppe, 42, now sell their elegant designs in the most exclusive shopping malls in Milan, New York, Moscow and Tokyo. Santoni senior learned his craft the traditional way, rising through the ranks. Andrea started out as a leather cutter, moving on to stitcher and was eventually promoted to the position of Production Manager in a major corporation. Then, in 1975, he and his wife Rosa founded their own company in the village of Corridonia, near Macerata and not far from central Italy’s Adriatic coast. His son is the corporate strategist. Giuseppe has developed the export side of the business and now serves as the company Chairman.
Most of the work in the factory is still carried out by hand. Four hundred people now work for Santoni in Corridonia. From the outset, Andrea Santoni and his company were rooted in the traditions of the region. In the early years, an older generation of highly skilled shoemakers from the surrounding area did all the exacting seam work. “Today we take on young people as trainee leather stitchers in our factory to ensure that this tradition does not die out,” explains Andrea Santoni. Two of the hallmarks of a Santoni shoe are the hand-sewn seams and the famous anticatura, the antique finish achieved by applying multiple coats of leather dye.
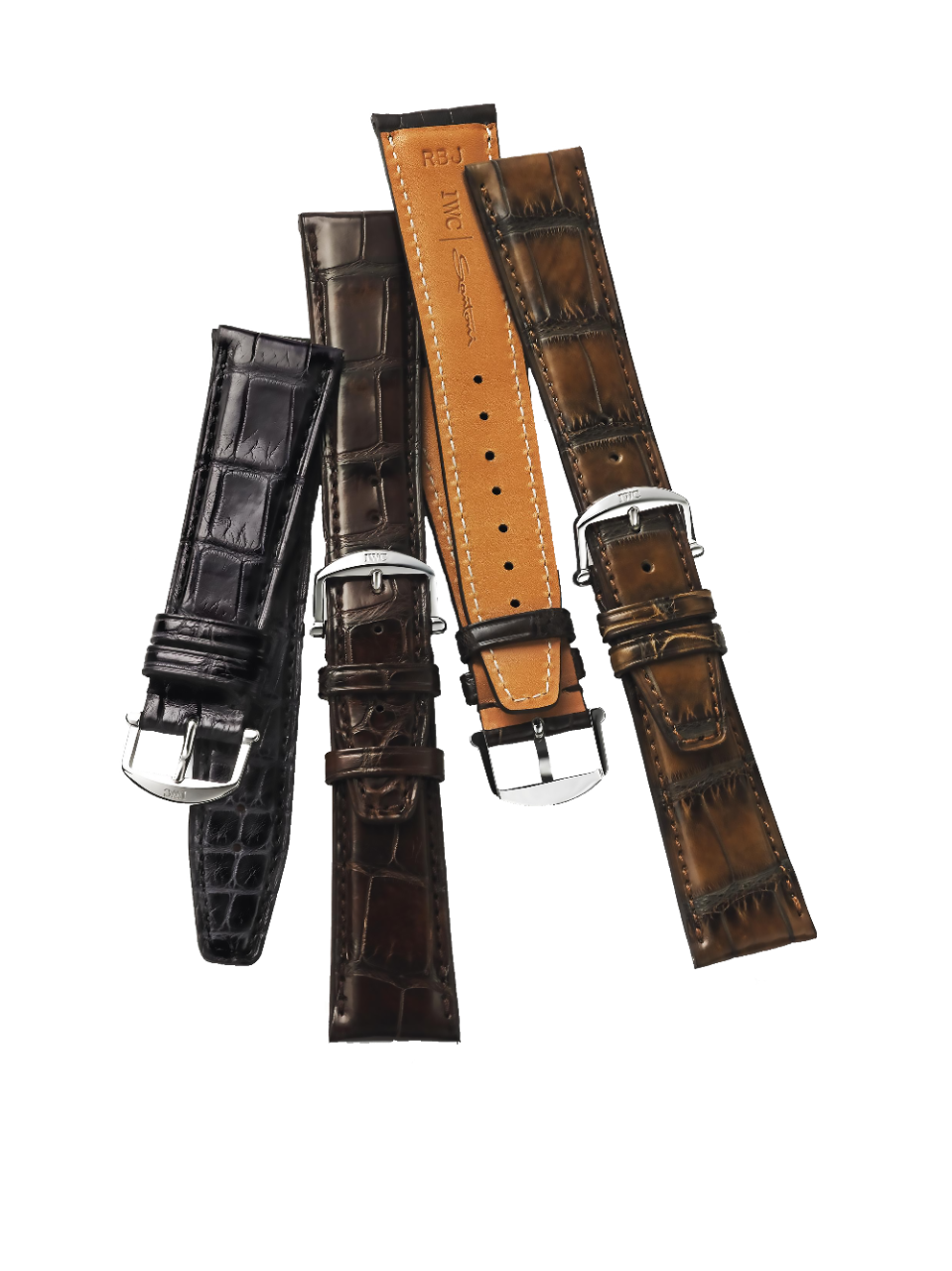
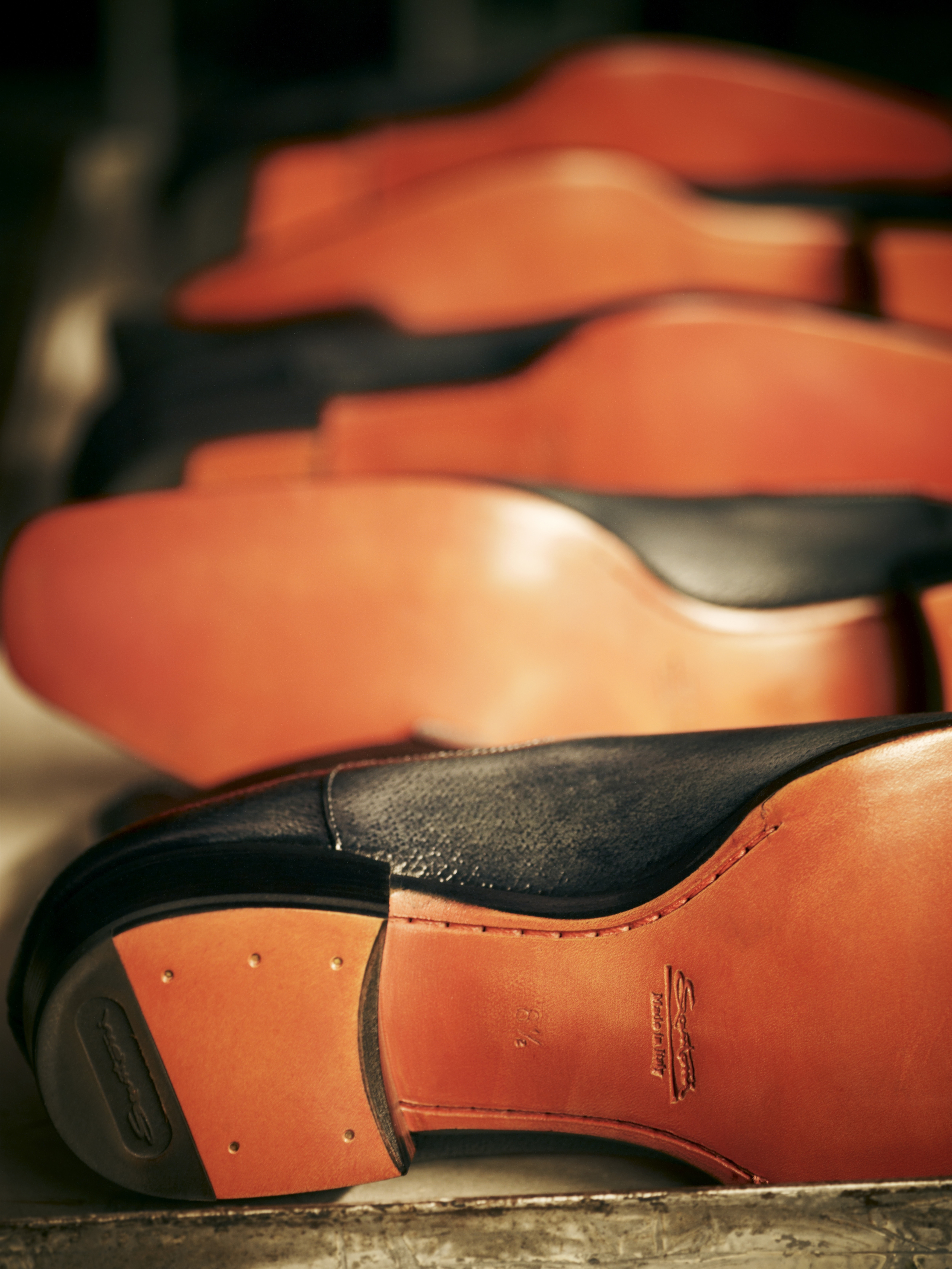
Nowadays Santoni even offers trainers, in addition to ladies’ and children’s collections. But the traditional expertise rests mainly in the gentlemen’s footwear of the “Manofatto” and “Limited Edition” lines, which are one-hundred-percent hand-crafted.
The oldest of the three factory shop floors is dedicated to men’s fashion. Fine leathers are stored in the cellar: English cowhide, American horsehide, and exotic skins such as crocodile, iguana and toad, even eel. That is why cutting the uppers to shape requires nimble fingers and manual dexterity. One false move can render valuable material unusable. The cutters for the hand-crafted shoe models cut around cardboard templates. Every centimetre of the leather is used.
After the individual parts of the upper have been cut out, they are stitched together. Many companies outsource this part of the work, but Andrea Santoni prefers to keep everything under one roof. “It’s all a question of quality control,” he says. Of course his factory does not use a conveyor belt. A manually operated carousel, known as the “manovia,” fulfils this function.
Once the upper has been stitched together, it has to be attached to the sole. This is done on the famous cobbler’s last: a hollow shape of a foot, which used to be wooden but is now moulded plastic. During fitting, the leather upper is mounted on the last, adjusted to the sole and stitched on. But no single shoe can meet every specification. So there is a range of models, each one differently constructed. The Bologna method, for example, does not mount the shoe on a last, but stitches it together empty, “like a bag”. The upper is only mounted on the last at a second stage. This method ensures that the leather is a perfect fit for the shape of the foot. The Goodyear system is also used for premier-quality shoes. The leather upper is mounted on the last by hand or by machine. Then the upper, edge and inner sole are stitched together. A cork paste is applied to the seam, to improve its stretch properties. The result is a sturdy shoe which nevertheless guarantees a soft feel in response to the movements of the foot.
This seam will hold forever. No machine can guarantee that
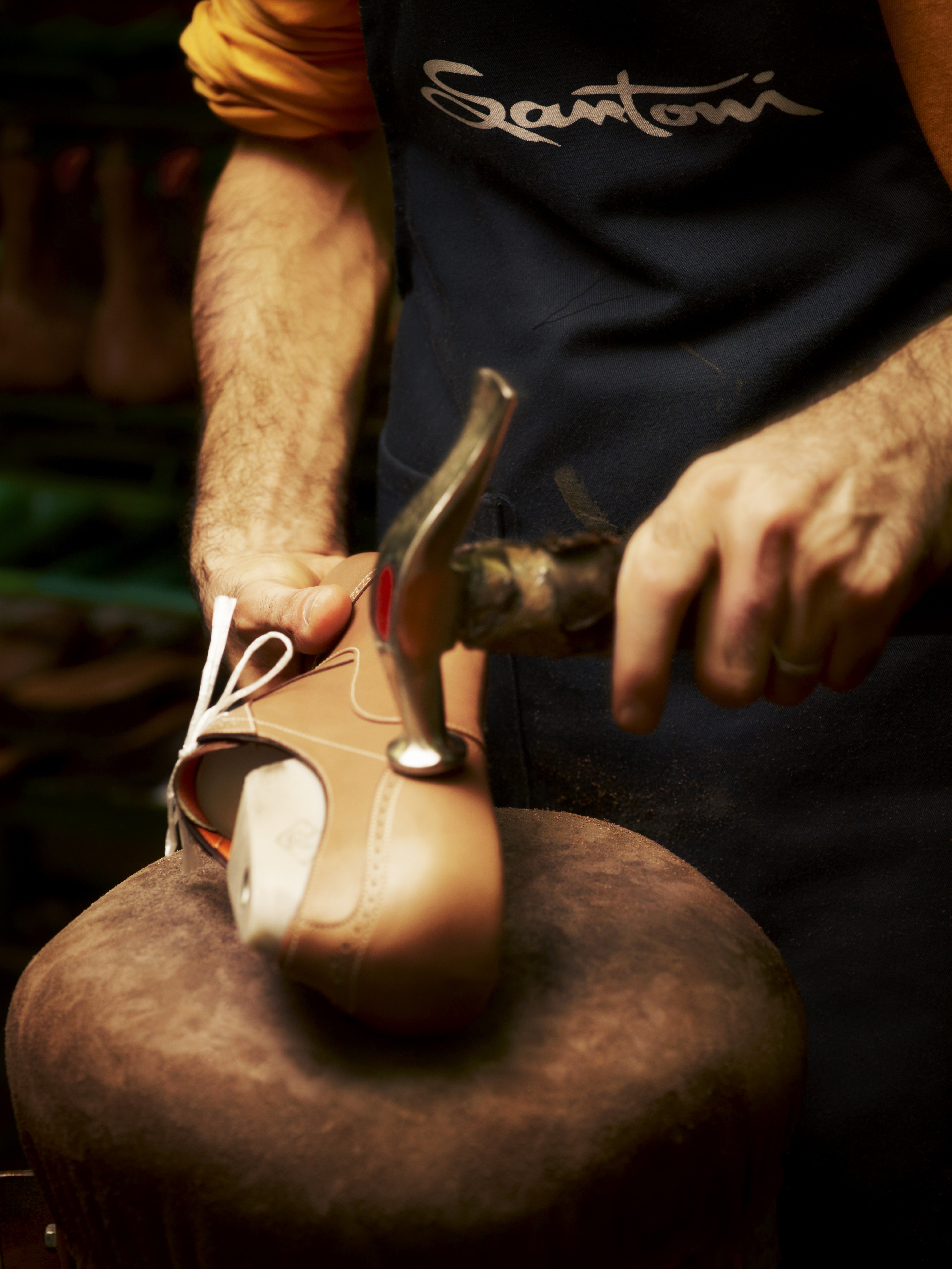
The unmistakable, identifying feature of a Santoni shoe is the laborious antique processing of the leather. Andrea Santoni dyed the first pair himself. He modelled this work on the elegant shoes of the French shoemaker Berluti. Later he entrusted the anticatura to his workers. One of the first to learn this art of dyeing from him, 12 years ago, was Fiorella Montemarani. She has now mastered the process perfectly. “The main requirements are patience and the lightness of touch needed to apply an irregular but even coating of the dye,” she reflects. Each leather absorbs dye differently, so the pressure of the brush or cloth must be adapted to the type of leather. The only dye used is aniline, imported from France. Some models, such as “Sirah” from the Limited Edition, receive up to ten coatings of dye, until they are flawless. The result is fascinating three-dimensional colour tones in the leather, not only in brown, but also powerful blue shades. These are an exclusive feature of the company’s products. “They make each shoe unique,” points out Andrea Santoni.
The ornamental seams are a special feature, painstakingly executed by hand. Antonio D’Alena, who has worked for Santoni for seven years, is currently working on the upper seams of a moccasin. He ties a knot after every stitch. “This seam will hold for ever. No machine can guarantee that,” he explains. Sitting next to him, colleagues are concentrating on the complicated concealed seam, which is found only in the most exclusive models. The needle is only allowed to penetrate the bottom layer of the leather in the upper. This results in a sophisticated relief pattern on the top surface. If the needle pierces the leather even once, the entire upper is unusable. It takes around four years to master the technique. Santoni is one of the few manufacturers still to use it.
Shelves full of shoes, wrapped in sheet plastic, line every corner of the workshop. These are the uppers, mounted on the lasts, complete with inner soles. As a rule, they stay on the shelf for four to six weeks, and have to be protected from dust and damp. When the shoes are detached from the lasts, they are still missing the outsole and heel. If the sole is rubber, this is stuck on. If it is leather, it is sewn.
The Santoni philosophy of “everything under one roof” also applies to the design of the models. In the brand new headquarters, built to ecological criteria in Corridonia, young designers are tasked with adapting the various collections to current trends, with the necessary finesse. Their manager in this work is Giuseppe Santoni, who monitors the shoes’ development up to the point of readiness of the finished collections. He and his sister Ilenia, 38, want to carry on the family firm and, of course, expand it if possible. Ilenia has specialized in administration. But none of that specialization prevents her from designing a new collection of santoni accessories too. Her bags and belts have two characteristic features: they are made of leather, dyed several times, and completed with hand-stitched seams. Because everything that leaves the factory in Corridonia has to be genuine Santoni.
CONTINUE READING
Icons of good style
The most sporting member of the Portugieser family from IWC Schaffhausen, the Portugieser Automatic, has a powerful and masculine aura. Find out more.
Forever Classic: IWC'S Portofino
IWC’s renowned Portofino line reflects classic design in its simplicity. Producing a watch where “less is more” is never simple and can reflect true aesthetic achievement.
REINVENTING TIMELESS BEAUTY
For the new Da Vinci collection, IWC reinterpreted the iconic round design of this watch family from the 1980s and gave it a more contemporary style. In doing so, the Swiss watch manufacturer created some of the most beautiful ladies’ watches in its history.
