INNOVATIVE MATERIALS
Every material has specific properties and offers certain advantages. The search for a material that meets the functional and aesthetic demands of a watch is a central component in IWC’s approach to engineering. In the course of its history, the company has acquired expertise that is unique in the processing of case materials.
CERALUME®
Ceralume®, a luminescent ceramic technology, is an innovative material from IWC Schaffhausen. In a highly engineered and patent-pending manufacturing process, ceramic powders are homogenously mixed with Super-LumiNova® pigments.
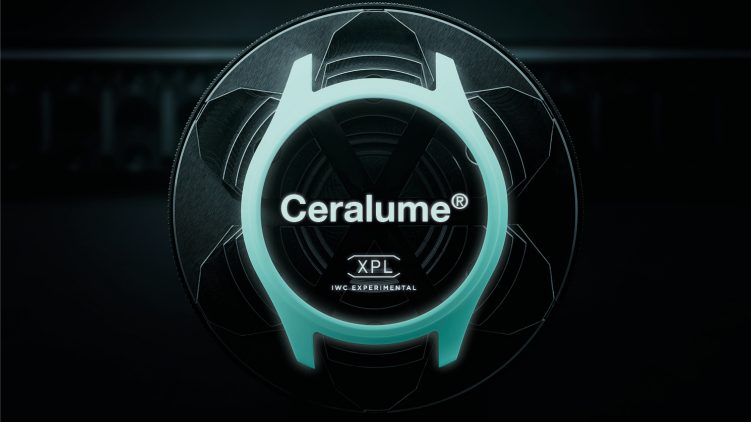
Conventional white ceramic is made by mixing zirconium oxide with other metallic oxides. These powders are shaped into to so-called “green body”, machines close to the final geometry and finally sintered at high temperatures in a kiln. For the white ceramic to glow in the dark, Super-LumiNova® pigments must be added to the ceramic powders. A key challenge in the development of Ceralume® was to achieve a perfectly homogenous mix of raw materials despite their different particle sizes and to avoid particle accumulations. To achieve these goals, IWC Schaffhausen’s engineers reverted to a dedicated ball milling process, which had to be customized to the raw materials used. In addition, the parameters of the sintering process and the grinding of the sintered ceramic body also had to be adapted to the luminous ceramic. In dark chamber tests, watch cases manufactured using the Ceralume® technology have emitted a bright blueish light for more than 24 hours.
FEATURED WATCHES
TITANIUM
Titanium is light and unbreakable. Additionally, the material is exceptionally skin-friendly and has an attractive matte-grey sheen.

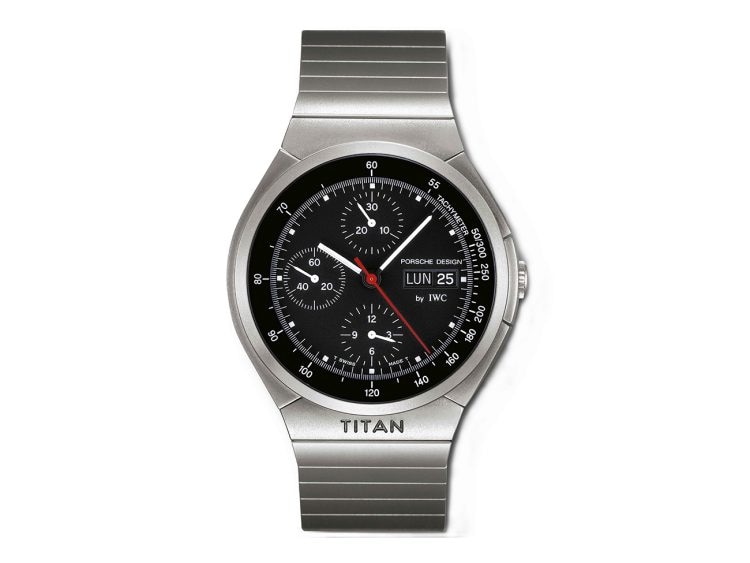
When a material needs to combine toughness with resilience, but still needs to be light, titanium is the best choice. The metal is enormously rugged and weighs about a third less than steel. Because of its skin-friendliness and anti-allergic properties, it is also used, among other things, for medical implants. All these properties virtually predestine titanium for use in watch cases. The challenge, however, is that the material is unusually hard and therefore difficult to machine. After every stage in the process, it needs to be soft-annealed or cooled down. In 1980, IWC unveiled the world’s first titanium wristwatch: IWC Porsche Design Titanchronograph (Ref. 3700). The engineers from Schaffhausen had acquired the expertise needed for its manufacture by liaising closely with experts from the French aviation and aerospace company Aérospatial. Since then, titanium watches have remained a fixed part of the portfolio, especially as members of the Pilot’s Watch and Ingenieur families.
CERATANIUM®
As light and robust as titanium but at the same time similarly hard and scratch-resistant as ceramic:
the Ceratanium® developed by IWC makes it possible for the first time to produce a completely black watch without any form of coating
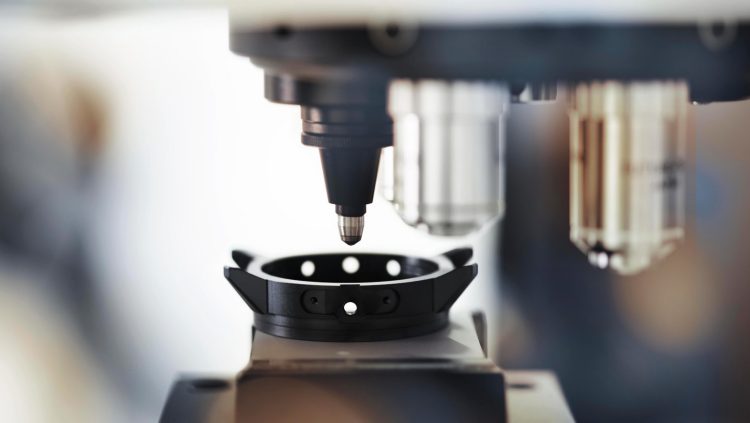
Another innovative material from Schaffhausen is Ceratanium® (ceramized titanium). It is as tough and almost as light as titanium but at the same time similarly hard and scratch-resistant as ceramic. Ceratanium® is based on a special titanium alloy that is made specifically for IWC. All the components in the case are milled, turned and drilled from the blank. It then goes into the oven for a thermal treatment. During this process, a phase transformation takes place, and the surface of the metal is ceramized. The process gives it not only the properties akin to ceramics, such as extreme hardness, but also its striking, matte black colour. For the first time, Ceratanium® makes it possible to manufacture components such as push-buttons or the pin buckle in a jet black design without coating in the Pilot’s Watch Chronograph 41 TOP GUN Ceratanium®.
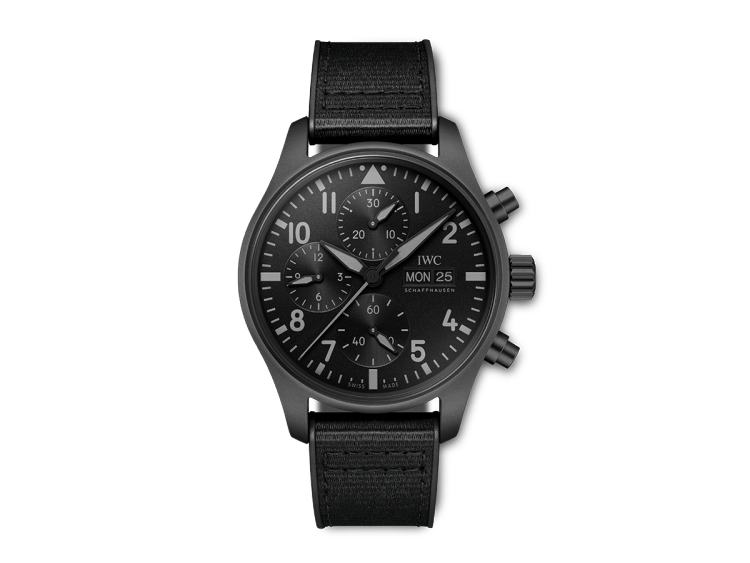
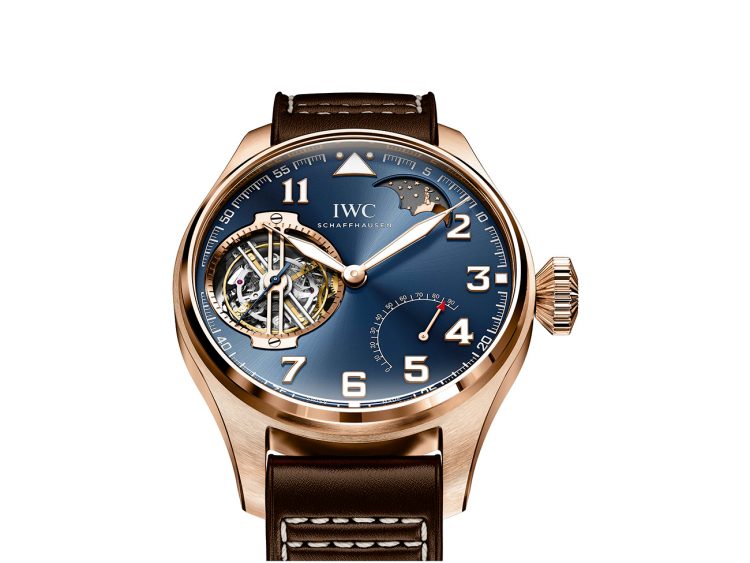
18 CT ARMOR GOLD®
18 ct Armor Gold® is a specialized type of gold that is significantly harder and more wear-resistant as conventional 5N gold.
Gold is timeless and retains its value. It embodies luxury and elegance more than any other precious metal. The pure gold content of an IWC watch case is 75 per cent, which is equivalent to 18 carats. The gold is alloyed with other materials and in this way assumes the desired colour. 18 ct Armor Gold® is an unusual new variant of 5N gold. The material is produced using a sophisticated process, during which the microstructure of the alloy is transformed. As a result, the material is significantly harder and more wear-resistant as conventional 5N gold. 18 ct Armor Gold® features for the first time in the Big Pilot’s Watch Constant Force Tourbillon Edition “Le Petit Prince” (Ref. 590303). This material is ideally suited for the bulky case and the striking diamond crown on the Big Pilot’s Watch.
BRONZE
Thanks to its specific composition, the bronze alloy used by IWC is just as hard as stainless steel and particularly skin-friendly.
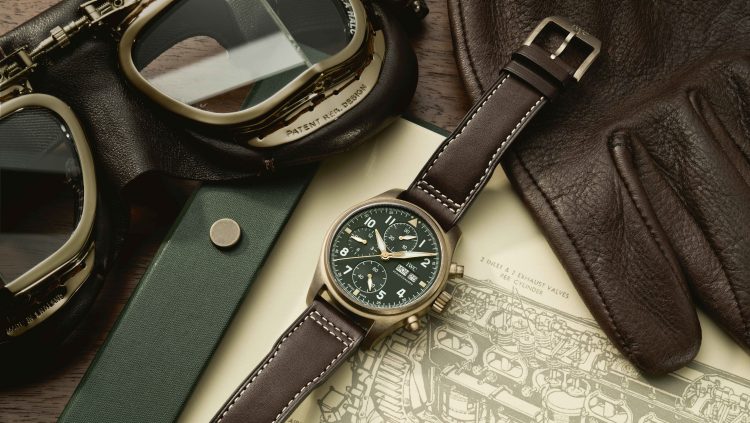
Bronze is one of the oldest materials in the history of humankind. Its use in the production of items of cultural significance is documented back to the middle of the fourth millennium BCE. Bronze is a catch-all metallurgical term used to describe alloys with a copper content of at least 60 per cent. For its watch cases, IWC uses aluminium bronze, which along with copper also contains aluminium and iron. This specific composition makes the alloy around 50 per cent harder than standard bronze and approximately as hard as stainless steel. An additional feature is the material’s high biocompatibility. It is the only form of bronze permitted for use in the food industry. Bronze, as used among other things for the Pilot’s Watch Automatic Spitfire (Ref. 326802), develops a singular patina with time, which makes every watch unique.
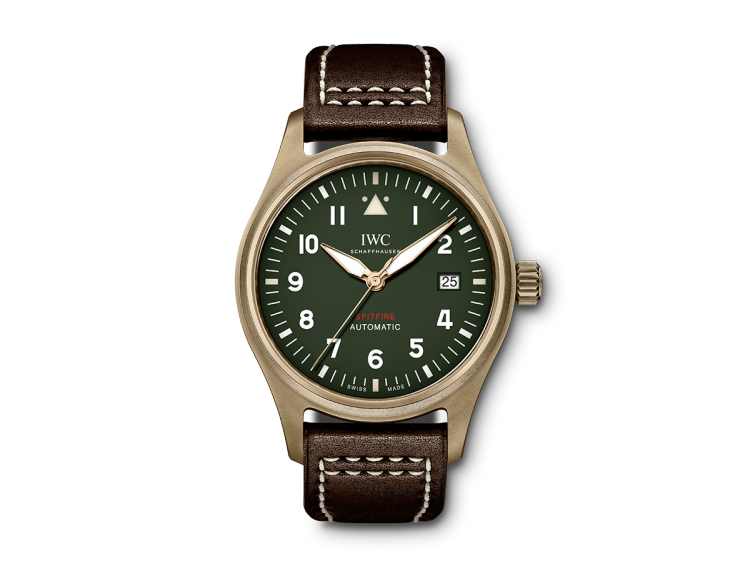
CERAMICS
Ceramics are lighter and harder than steel, absolutely scratch-resistant and have an agreeable, velvety surface.
These properties make the high-tech material ideal for use in wristwatches.
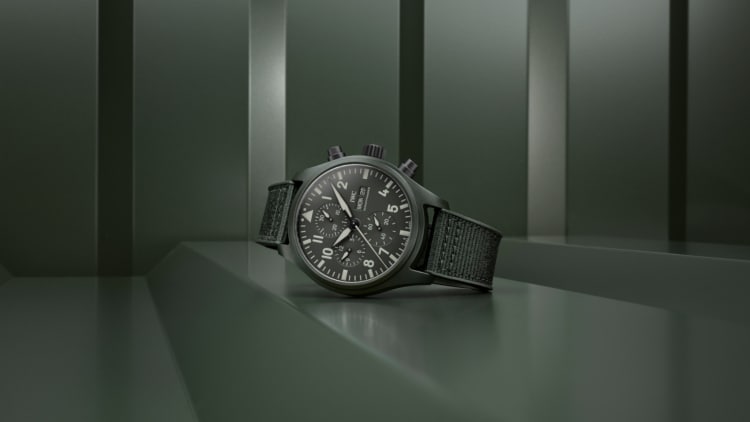
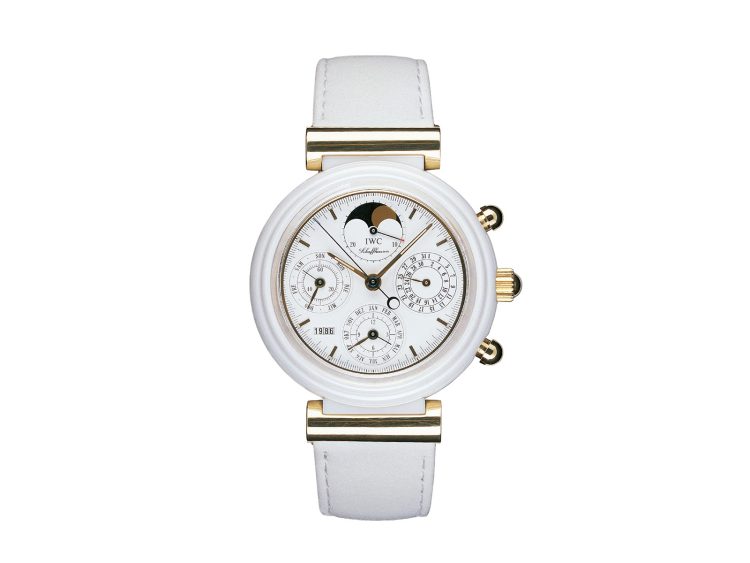
Technical ceramics of the kind used in watches are based on polycrystalline powders such as silicates, aluminium oxide or silicon carbide. They are mixed with various additives to form a homogeneous mass, shaped and sintered at very high temperatures in an oven. During the sintering process, the additives vaporize to leave extremely stable ceramic bodies. The manufacture of a watch case, however, is very demanding because the ceramic shrinks by around a third during the baking process. This shrinkage has to be factored in as early as the design phase to ensure that the movement later fits snugly inside the case and satisfies the narrow tolerances. IWC presented the world’s first ceramic watch, the Da Vinci Perpetual Calendar (Ref. 3755), in 1986. Since then, the company has launched watch cases made of black boron carbide high-performance ceramic or brown silicon nitride ceramic. An example of innovative ceramics from Schaffhausen is the Colors of TOP GUN: Colored Ceramic Watches.
PLATINUM
Platinum is the rarest, purest and most precious of all the metals used in the production of jewellery.
It is imperishable and has a singular, whitish sheen.
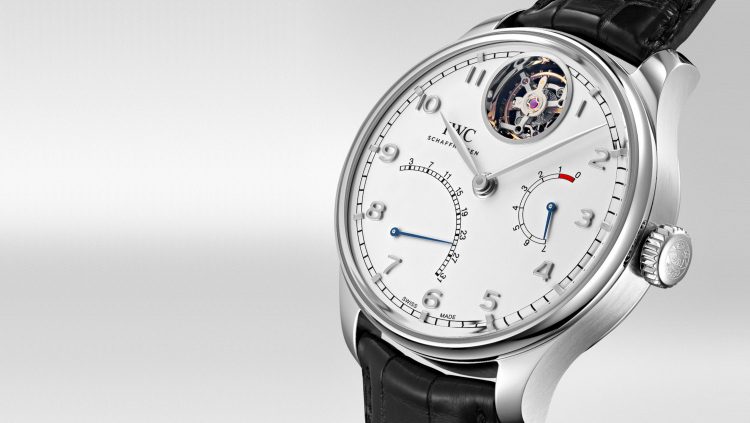
Platinum has lain inert in the depths of the earth for billions of years. But it is only in the past few hundred years that we have been able to extract and process the shiny grey-white metal. Platinum is extremely scarce and precious. Around ten metric tons of ore need to be mined to produce a single ounce of the metal. It then takes more than one hundred separate stages to separate the platinum from the ore. This process may take up to several months. Because of its unusually high purity, platinum is heavier than either silver or gold. IWC uses platinum for the Portugieser Perpetual Calendar (Ref. IW503406), for instance. This imperishable precious metal imbues any wristwatch with a unique character of its own.
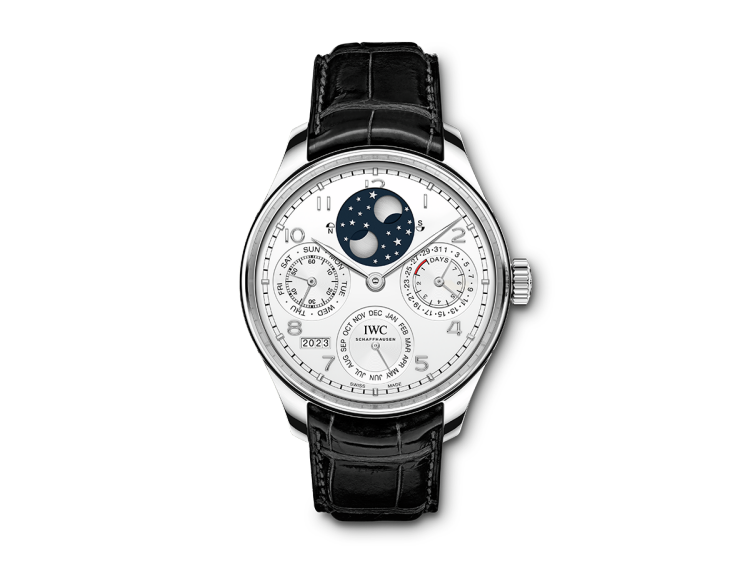