OROLOGI MADE IN SCHAFFHAUSEN
Ogni orologio di IWC viene assemblato individualmente da uno dei nostri orologiai professionisti. Sono il loro occhio esperto, la loro destrezza manuale e la precisione della loro strumentazione che consentono di creare, partendo da centinaia di singoli componenti, gli orologio da polso IWC, ognuno dei quali è un affascinante connubio di estetica, funzionalità e perfezione, un modello di arte orologiera e di incomparabile eccellenza.
LA FILOSOFIA DI IWC
Schaffhausen rappresenta un’isola nel panorama orologiero svizzero. Il nucleo principale di costruttori di orologi si trova, infatti, nella Svizzera di lingua francese. Sin dalla fondazione di IWC, nel 1868, questa particolare posizione geografica ha favorito l’affermarsi di una peculiare filosofia aziendale. Con un chiaro focus sulla tecnologia e sullo sviluppo, la manifattura sulle rive del Reno produce segnatempo di precisione, il cui valore non teme il trascorrere del tempo. IWC Schaffhausen si è affermata su scala internazionale grazie alla propria passione per l’innovazione e lo spirito pionieristico. Tra i leader mondiali nel segmento degli orologi di lusso, IWC produce capolavori di alta orologeria che combinano tecnica ingegneristica e massima precisione con un design esclusivo. La reputazione del marchio di Schaffhausen si fonda anche e soprattutto sull’altissima competenza dei suoi collaboratori, che padroneggiano ai massimi livelli l’arte di costruire calibri di manifattura e complicazioni orologiere come la ripetizione minuti, il tourbillon e il calendario perpetuo. Per i progettisti e i designer di IWC la promessa di eccellenza «Probus Scafusia» – «Qualità made in Schaffhausen», formulata per la prima volta nel 1903, non è soltanto una grande sfida professionale, ma anche un’autentica passione.
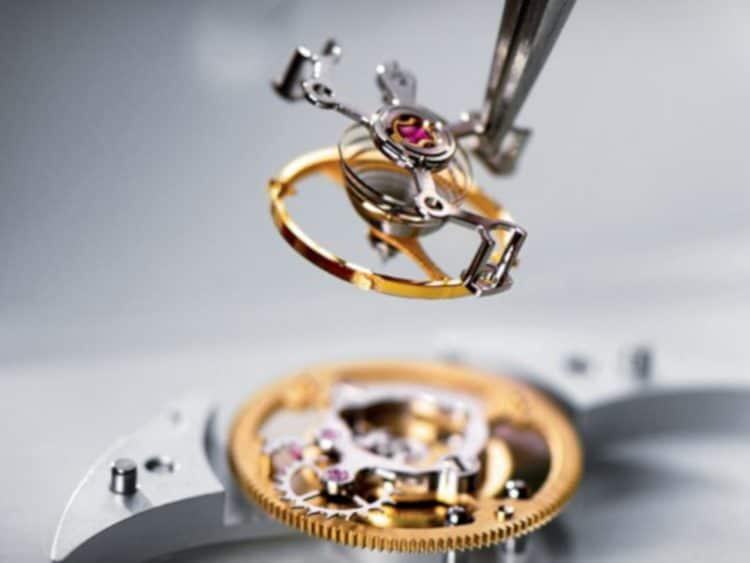
SVILUPPO
PRIMA CHE IL CUORE DI UN OROLOGIO IWC INIZI A BATTERE
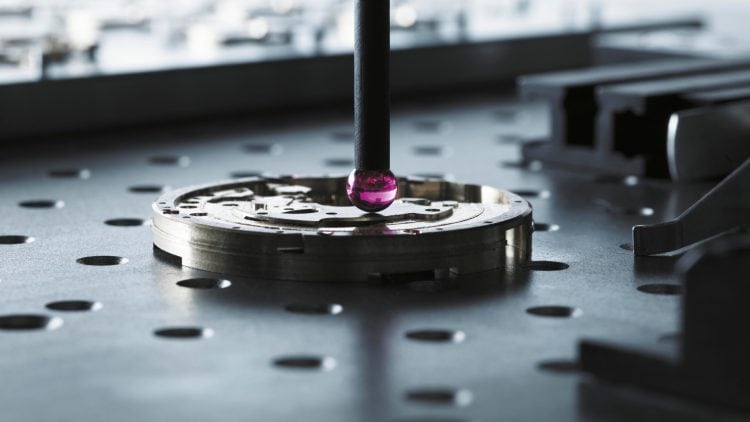
PROGETTAZIONE E DESIGN
Ogni volta che IWC inizia lo sviluppo di un nuovo modello, i nostri designer e ingegneri si pongono prima di tutto una domanda fondamentale: cosa desideriamo ottenere esattamente? Vogliamo che l’orologio apra nuovi orizzonti in termini di complessità? Vogliamo che il suo punto forte sia la riserva di carica? O piuttosto l’impermeabilità? Il primo passo consiste nel disegnare i primi componenti con i programmi CAD. In questa fase, per IWC è importantissimo che il lavoro di progettazione e design si integri perfettamente con le moderne tecnologie di produzione. Lavorando gomito a gomito con gli ingegneri, i nostri designer svolgono un ruolo cruciale nel definire il miglior modo di armonizzare estetica e funzionalità dell’orologio. Il quadrante e il cinturino o bracciale, la posizione delle indicazioni, la scelta dei materiali e dei colori, la finitura delle superfici sono sempre il risultato di un lavoro di squadra costruttivo. Oltre alla tecnologia e all’estetica, si devono considerare anche aspetti più emotivi, come per esempio la sensazione che si prova tenendo l’orologio in mano. Di conseguenza, non si lasciano al caso neppure dettagli come gli spigoli della cassa, il modo in cui si attivano i pulsanti o il rumore della corona quando scatta. Spesso, gli ingegneri e i designer di IWC si ispirano a vecchi schizzi e progetti. Perché, in ultima analisi, è proprio il rispetto per i pionieri del passato che assicura la continuità dell’azienda di Schaffhausen.
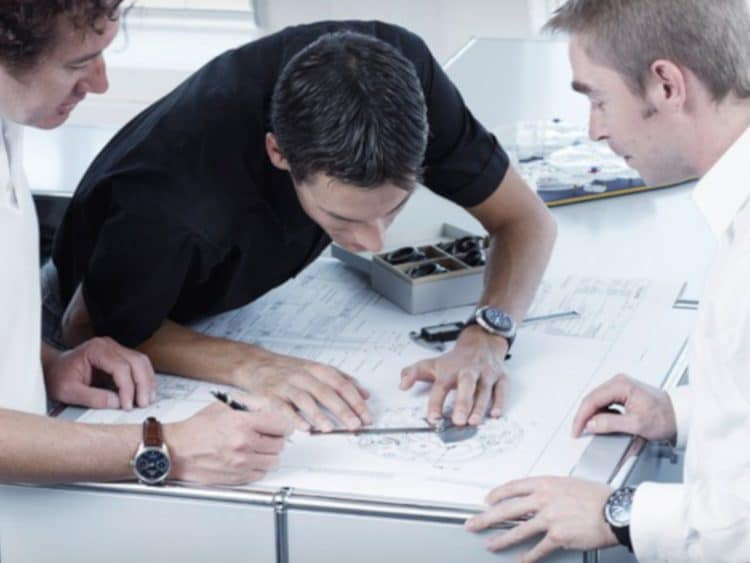
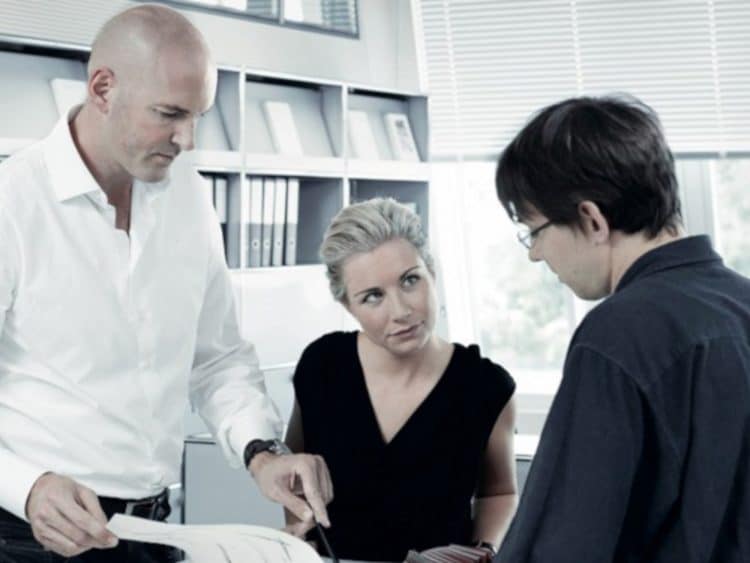
GESTIONE DELLA QUALITÀ
IWC garantisce l’elevata qualità dei suoi prodotti mediante una complessa attività di sviluppo e gestione della qualità, abbinata a un severo programma di sperimentazione e di collaudo. I metodi scientifici utilizzati comprendono simulazioni tridimensionali a computer, analisi a raggi X dei materiali e test volti a dimostrare il comportamento degli orologi in condizioni quotidiane estreme. Videocamere ad alta velocità e misuratori laser permettono di osservare ogni minimo spostamento, mentre speciali software provvedono a calcolare esattamente il profilo di resistenza di ciascun componente.
Per tutte le soluzioni di dettaglio – come le ruote, gli alberi, i profili dei denti o le dimensioni delle molle – le eventuali fonti di problemi vengono analizzate fin dalle primissime fasi di sviluppo: IWC definisce questo processo Failure Mode and Effects Analysis (FMEA), ovvero analisi della criticità di possibili errori. A tal fine i progettisti sfruttano le esperienze di precedenti progetti, i feedback del mercato e le segnalazioni relative alla facilità di manutenzione. Tutto ciò consente di assicurare che un orologio IWC funzioni in modo ineccepibile per molto tempo e, in caso di necessità, possa essere riparato senza problemi anche a distanza di anni.
TESTS
IL LUNGO E DIFFICILE CAMMINO DAL PROTOTIPO AL PRODOTTO FINITO
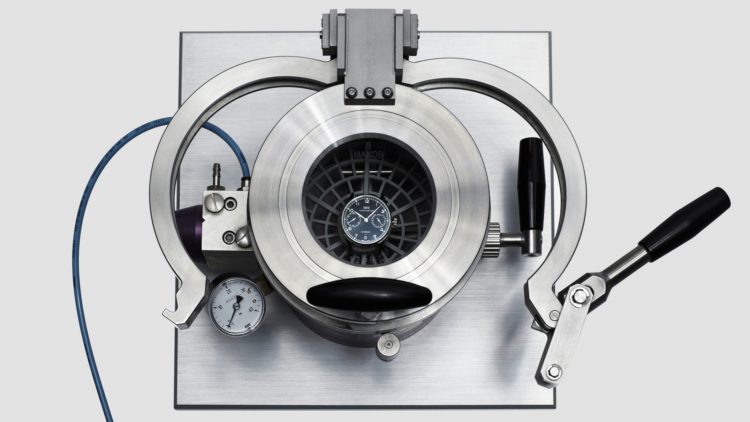
QUALIFICAZIONE E OMOLOGAZIONE
Il concetto di «qualificazione» identifica un programma di verifica che dura vari mesi e comprende circa trenta severi test, a livello di prototipo o in fase di omologazione della preserie. Questi test simulano in forma concentrata tutto ciò a cui potrebbe trovarsi esposto un orologio nelle situazioni normali ed estreme della sua lunga vita. Solo dopo che il rigoroso collaudo di svariati prototipi e la realizzazione della preserie avranno dissipato ogni minimo dubbio, l’idoneità alla produzione in serie potrà dirsi comprovata e la leggenda di IWC arricchirsi di un nuovo, affascinante capitolo.
TEST DI RESISTENZA ALLA CORROSIONE E AI RAGGI UV
Un test di due settimane in un bagno salino a 37° C garantisce che vengano impiegati solo materiali resistenti all’uso quotidiano e al contatto con acqua salata. Il colore dei quadranti, esposti per giorni a un’intensa luce ultravioletta, non deve subire variazioni.
TEST DI USURA
Nei test di resistenza agli urti un orologio affronta vari livelli di accelerazione. Tenendo presente che l’unità di misura dell’accelerazione di gravità è 1 g = 9,81 m/s², con un carico d’urto di 100 g ogni componente di un orologio con cassa da 100 grammi deve sopportare sollecitazioni equivalenti a 10 chilogrammi. I Pilot’s Watches di IWC sono addirittura riusciti a sopravvivere alcuni minuti a forze di 30 g in un acceleratore centrifugo. Nel pendolo di Charpy, invece, l’orologio viene sottoposto per una frazione di secondo a un’accelerazione di ben 5000 g, per simulare la caduta su un fondo di legno duro dall’altezza di 1 metro. Un’altra severa prova di resistenza è lo «chapuis extrême», un test in cui l’orologio viene agitato per ore all’interno di un piccolo contenitore esposto a urti continui su tutti i lati – 140 000 urti con una gravità simulata di 25 g, 94 000 urti a 100 g e 960 urti a 500 g.
TEST CLIMATICI
Durante i test climatici l’orologio viene provato in tutte le condizioni termiche a cui potrebbe trovarsi esposto nel corso della sua vita. In termini geografici, ciò equivale a un viaggio dall’Alaska al Sahara, passando per la foresta pluviale del Brasile. Gli orologi vengono posti in un’apposita camera per test climatici in cui, per diversi giorni e talvolta per settimane, devono sopportare sbalzi di temperatura che vanno da -20°C a +70°C e fino al 95% di umidità relativa. La fase successiva è un test di funzionamento prolungato, che si avvale di un microfono con brandeggio motorizzato per verificare la regolarità della marcia.
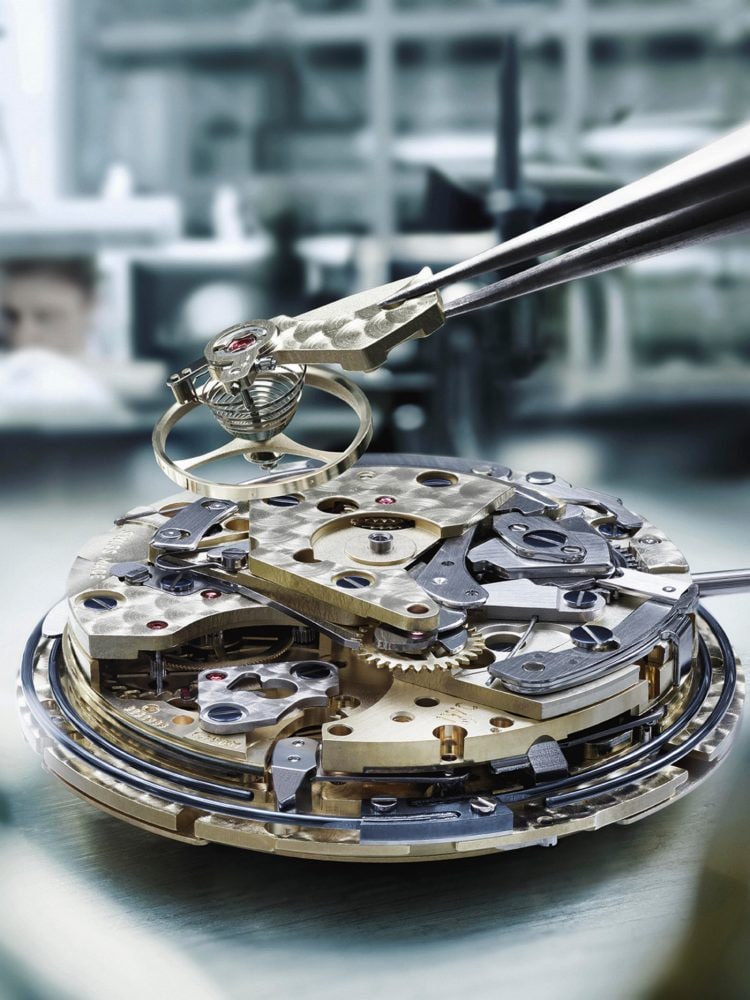
ASSEMBLAGGIO
DA IWC, ALTA TECNOLOGIA E TALENTO ARTIGIANALE VANNO DI PARI PASSO
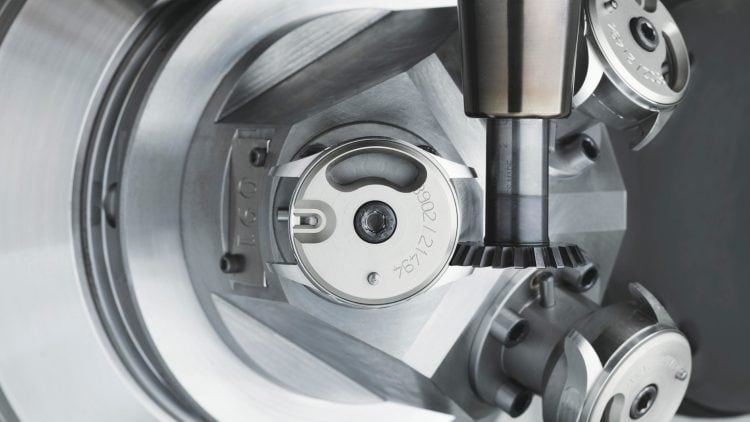
TECNICHE DI PRODUZIONE
Durante la produzione dei componenti, i pezzi grezzi vengono lavorati con l’ausilio di fresatrici CNC che permettono di conseguire tolleranze ridottissime, pari in genere ad appena +/–0,02 millimetri, in alcuni casi addirittura a +/–0,002 millimetri. Finita la lavorazione a macchina, i pezzi vengono rifiniti a mano o passati in una macchina per elettroerosione. Per i componenti del movimento si impiegano prevalentemente macchine CNC per elettroerosione a filo (EDM), grazie alle quali la rugosità superficiale, che in ogni caso non supera una tolleranza di 0,005 millimetri, viene ridotta ulteriormente fino a 0,001 millimetri.
ASSEMBLAGGIO DEL MOVIMENTO
L’assemblaggio del movimento consiste nella connessione del meccanismo di carica, del ruotismo e dello scappamento e nel successivo réglage, ossia nella regolazione di precisione. A seconda del modello di orologio vengono installati anche il meccanismo automatico e cronografico, nonché quello del calendario e delle ore. Le operazioni più impegnative sono la messa a punto dello scappamento e la regolazione della coassialità e planarità della spirale, un lavoro manuale di altissima precisione che nessuna macchina sarebbe in grado di svolgere con gli stessi elevatissimi standard qualitativi. Ogni fase del processo di assemblaggio implica il controllo e l’eventuale correzione di tutte le funzioni e regolazioni di precisione. Al termine di questo processo, gli orologiai altamente qualificati del reparto Complicazioni provvedono ad aggiungere al movimento di base moduli come il calendario perpetuo o il meccanismo rattrapante. Il tourbillon e la ripetizione minuti vengono invece totalmente assemblati nel reparto Specialità: qui avvengono le fasi di lavorazione del preassemblaggio e dell’assemblaggio definitivo, nonché tutte le regolazioni fini e l’inserimento nella cassa.
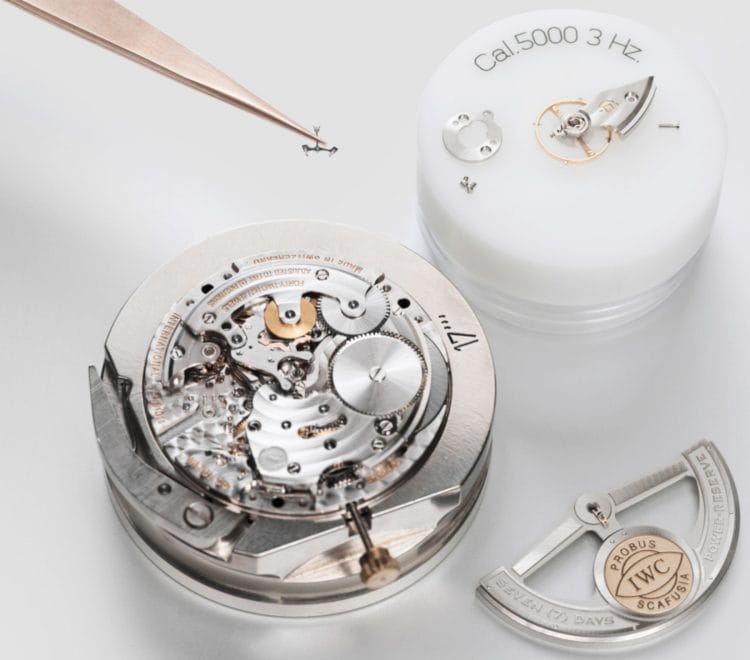
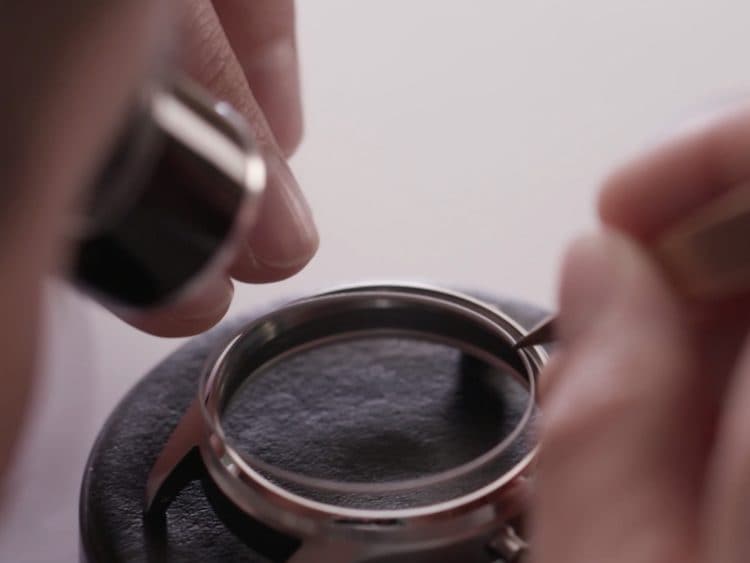
FABBRICAZIONE E MONTAGGIO DELLA CASSA
In termini di precisione e impegno, la produzione della cassa non è in alcun modo inferiore alle altre fasi della produzione. Per gli orologi in metallo prezioso, i componenti della cassa vengono fabbricati con pezzi grezzi preformati. Le casse in acciaio e in titanio vengono invece ricavate da barre prodotte appositamente per IWC, che vengono lavorate su stazioni di tornitura e fresatura CNC fino a raggiungere una precisione di un centesimo di millimetro. Le stazioni di fresatura vengono impiegate non soltanto per fresare le anse e alesare i fori per la corona e i pulsanti, bensì anche per realizzare le complesse superfici a forma libera tipiche, per esempio, degli orologi Ingenieur. Dopo queste lavorazioni per asportazione di truciolo si procede a un meticoloso controllo delle dimensioni e ad un’accurata finitura delle superfici, per portarle agli standard di precisione propri di IWC. Gli spigoli vengono smussati e arrotondati, le zone prefissate sfaccettate, le tracce di tornitura, fresatura e trattamento eliminate, le superfici sottoposte a microfinitura nonché lucidate, satinate e sabbiate. Per finire, le superfici di certi componenti della cassa vengono valorizzate dai nostri specialisti con trattamenti decorativi come il perlage, persino in punti non visibili dall’esterno. La fabbricazione della cassa si conclude con una serie di complessi test, p.es. per verificare l’impermeabilità e l’estetica.
QUADRANTE, LANCETTE E INSERIMENTO DEL MOVIMENTO NELLA CASSA
In questi reparti, ogni operazione viene eseguita a mano. A seconda del modello, il montaggio del quadrante sul movimento – già perfettamente regolato – avviene a mano oppure con l’aiuto di appositi strumenti. Lo stesso vale per le lancette, che devono essere applicate all’altezza esatta e fissate saldamente sul perno. Nei cronografi, anche l’azzeramento delle lancette esige un’assoluta precisione. Il movimento viene quindi inserito nella cassa e fissato a un apposito anello oppure alla cassa stessa. Se si usa un anello, questo viene tenuto in posizione da una molla ondulata situata nel fondello. Gli alberi di carica vengono regolati uno ad uno. Un collante speciale fissa le corone avvitate sull’albero di carica.
CONTROLLO FINALE
Per dieci giorni, i movimenti degli orologi a carica automatica vengono ruotati continuamente, mentre per quelli a carica manuale viene effettuata una carica completa a giorni alterni. Questo «rodaggio» fa sì che le ruote e i perni si adattino perfettamente gli uni agli altri e che il lubrificante penetri in tutti i punti previsti.
La parte conclusiva del processo di verifica della qualità è costituita dai numerosi controlli finali. Per testarne un’ultima volta la resistenza alle sollecitazioni dell’uso quotidiano, l’orologio viene caricato completamente, dopodiché si procede al controllo della precisione di marcia, delle funzioni e dell’aspetto, nonché ai test di tenuta stagna sotto pressione atmosferica e idrica. Ogni prodotto che lascia la manifattura di Schaffhausen si distingue così per una qualità al di sopra di ogni dubbio. Una certificazione di qualità totale, che trasforma la leggendaria promessa di qualità IWC in una realtà concreta e tangibile per tutti i proprietari di un orologio IWC.
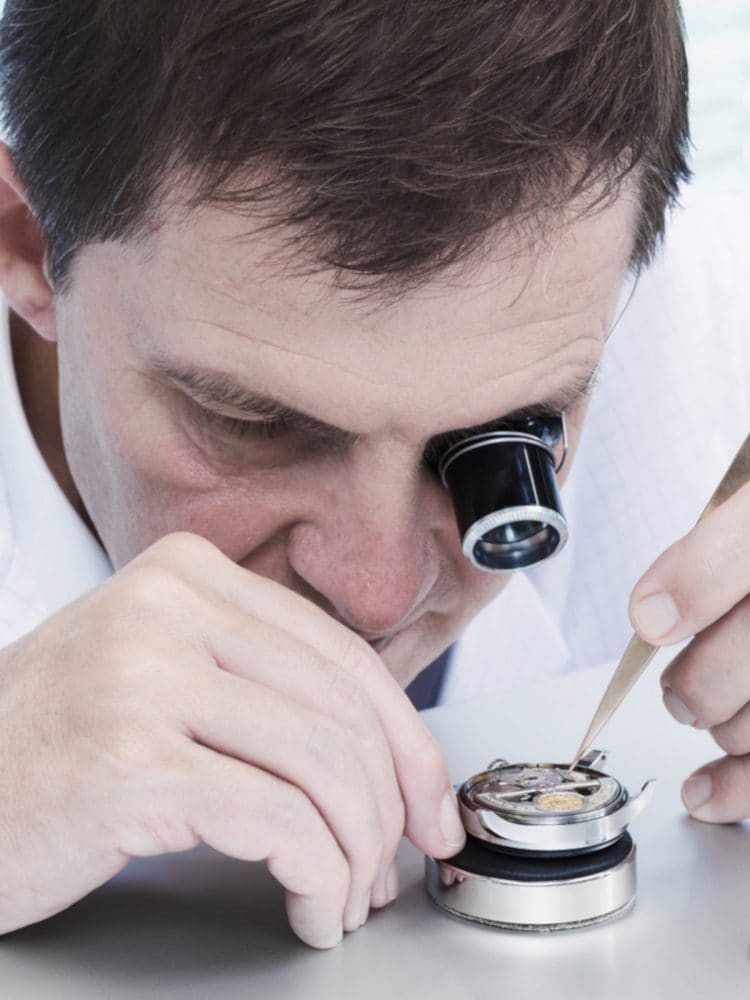
PERSONALIZZAZIONE
UN’INCISIONE RENDE UNICO IL TUO OROLOGIO IWC
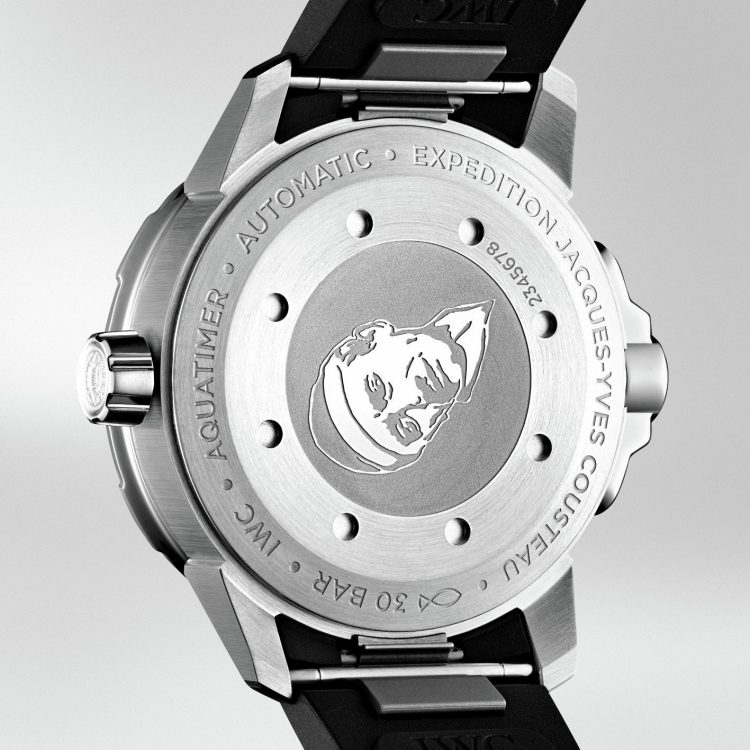
Ogni orologio IWC ha la propria personalità. Ma ci sono clienti che ci chiedono ancora di più: un orologio da tasca o da polso assolutamente unico e individuale.
Grazie a moderne tecniche di incisione, IWC offre una gamma di opzioni pressoché illimitata, in grado di soddisfare praticamente qualsiasi richiesta. «Incisione» viene dal termine latino «incidere» che, in origine, significava «scavare un solco».
L’incisione di disegni, motivi, decorazioni o iscrizioni su legno, pietra, avorio e metallo consente di ottenere affascinanti giochi di luce e ombra e di dar vita a creazioni molto originali.
Nascono così vere e proprie opere d’arte in miniatura, piccoli capolavori creati per l’eternità, come quelli che ornano il fondello dell’Aquatimer Chronograph Edition «Expedition Jacques-Yves Cousteau» o dell’Ingenieur Chronograph Silberpfeil. La tecnica dell’incisione è ideale per personalizzare i nostri segnatempo: delle iniziali, una data, uno stemma di famiglia, un logo aziendale o una dedica personale fanno di ogni orologio IWC un pezzo unico, l’essenza stessa dell’individualità.
ASSISTENZA
IL PIACERE DI UN OROLOGIO IWC SI TRASMETTE DI GENERAZIONE IN GENERAZIONE
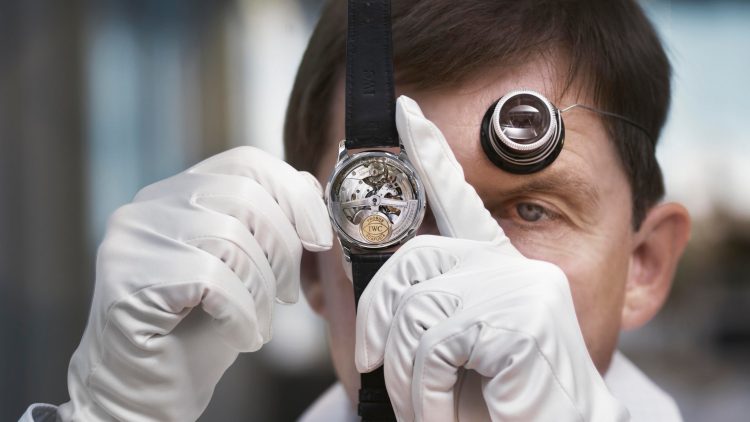
MANUTENZIONE E ASSISTENZA
In 25 paesi di tutto il mondo sono più di duecento gli orologiai e gli addetti al servizio di assistenza che si dedicano esclusivamente alla cura e alla riparazione di orologi IWC appartenenti a ogni epoca, a partire dalla fondazione della manifattura nel 1868. Affinché nessun dettaglio vada perso, nel registro anagrafico della manifattura viene conservata una scheda per ogni orologio prodotto, dal 1885 in poi.
Il «sancta sanctorum» del servizio riparazioni è il magazzino ricambi. Nei suoi scaffali sono immagazzinati milioni di componenti, ordinatamente disposti. La garanzia di poter fornire ricambi originali ha per IWC un’elevata priorità, perché solo così un orologio può conservarsi da una generazione all’altra. Gli intervalli di assistenza variano notevolmente a seconda del modo e delle condizioni in cui viene usato l’orologio.
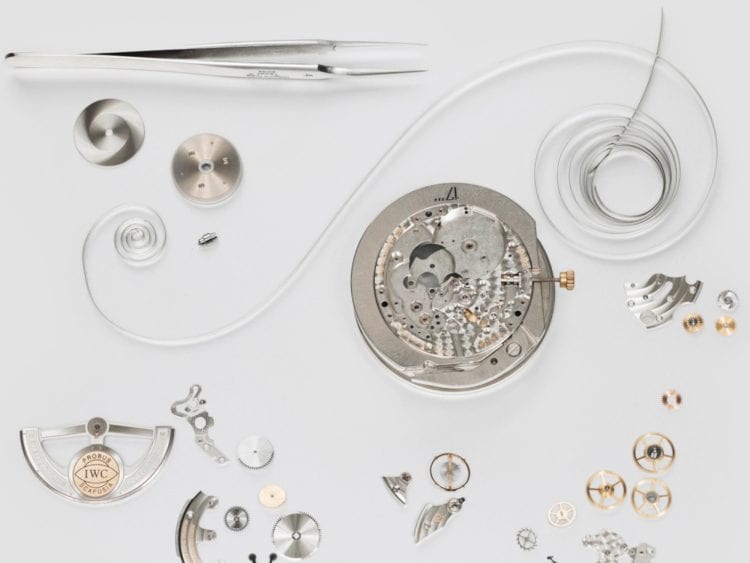
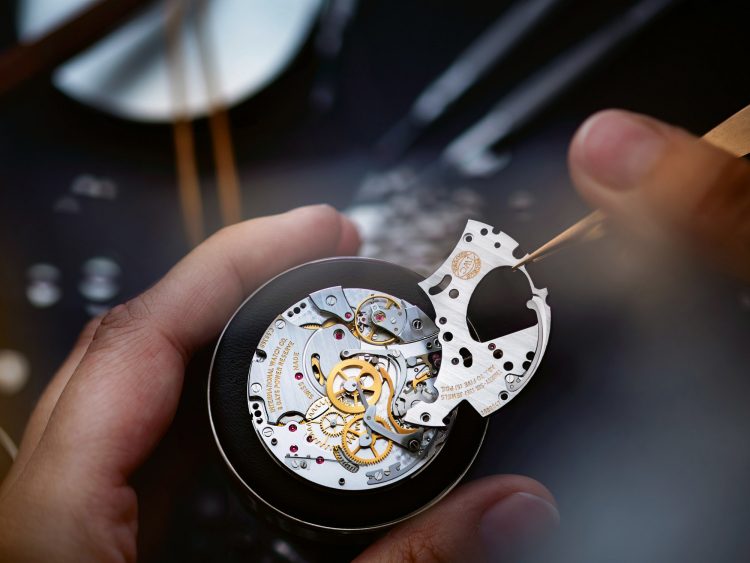
SERVIZIO DI MANUTENZIONE STRAORDINARIO
Il servizio di manutenzione straordinario prevede lo smontaggio completo del movimento pezzo per pezzo e la pulizia dei singoli componenti. Gli specialisti esaminano attentamente ogni parte del movimento, riparando o sostituendo quelle usurate o guaste. Successivamente, l’orologio viene riassemblato e, ove necessario, oliato e lubrificato.
Infine, si verifica la precisione e si esegue una nuova messa a punto del movimento. Anche la cassa viene smontata completamente. I graffi vengono riparati, i componenti della cassa e del bracciale vengono levigati o lucidati, gli angoli rifiniti. Segue una meticolosa pulizia. Prima di essere restituito al cliente ogni orologio deve superare il controllo finale, che prevede un intenso programma di test sull’arco di più giorni. Solo così è possibile garantirne la precisione di marcia e l’impermeabilità negli anni a venire.
Ogni proprietario di un orologio IWC può contribuire ad aumentare la vita utile del proprio segnatempo: basta seguire i consigli e suggerimenti contenuti in questo sito e nell’opuscolo «Il servizio di assistenza IWC» disponibile nelle boutique e nei centri assistenza IWC e presso i nostri rivenditori autorizzati.
CERTIFICATO IWC
La storia di ogni orologio IWC ha inizio nella manifattura, dove orologiai animati da un’inesauribile passione dedicano ore e ore alla cura di ogni dettaglio. Per non perderli mai definitivamente di vista, già nel 1885 IWC iniziò a tenere dei registri anagrafici dei propri segnatempo. Vi vengono annotati tutti i dati rilevanti, quali data di vendita, calibro, materiale, numero di cassa e, per i modelli più recenti, anche il numero di referenza. Eredi o acquirenti successivi hanno così la possibilità (dietro un contributo spese) di ottenere precise informazioni sul proprio orologio IWC e di farsene attestare l’autenticità. Queste e altre informazioni vengono fornite sotto forma di certificato.
Per il rilascio dei certificati è necessario consegnare l’orologio a una boutique IWC oppure a un rivenditore autorizzato. Il segnatempo verrà inviato alla manifattura di Schaffhausen, dove sarà esaminato attentamente da uno dei nostri esperti orologiai.
Purtroppo non è possibile richiedere indicazioni relative al valore di mercato di un determinato modello. Esso dipende infatti da fattori variabili come la domanda e l’offerta, nonché dalle condizioni del movimento e della cassa.
In the event of a worst-case scenario involving loss or theft, it is advisable to report the incident in writing to the police and IWC. The case number, or the reference number for a newer model, in question is then entered in a special register, which ensures the watch is recognized if it is taken to an IWC service centre. This registration process has so far allowed many missing watches to be reunited with their rightful owners.
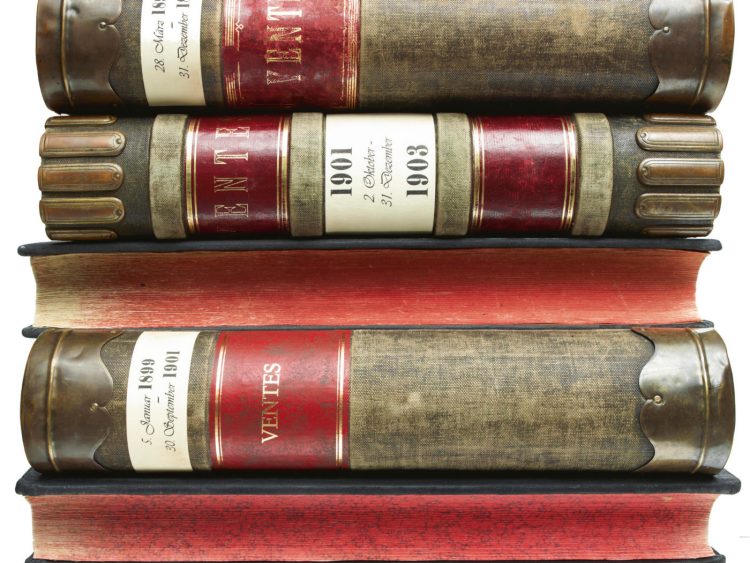