Unternehmen
Armbanduhren aus Schaffhausen
Jede Uhr von IWC wird von einem unserer professionellen Uhrmacher einzeln zusammengebaut. Mit geschultem Auge, Fingerfertigkeit und Präzisionsinstrumenten setzen sie mehrere Hundert Einzelteile zu grossartigen Armbanduhren zusammen: Meisterwerke der minutiösen Handwerkskunst, der Funktionalität und des Designs, jede einzelne ein herausragendes Beispiel für Uhrmacherei auf höchstem Niveau.
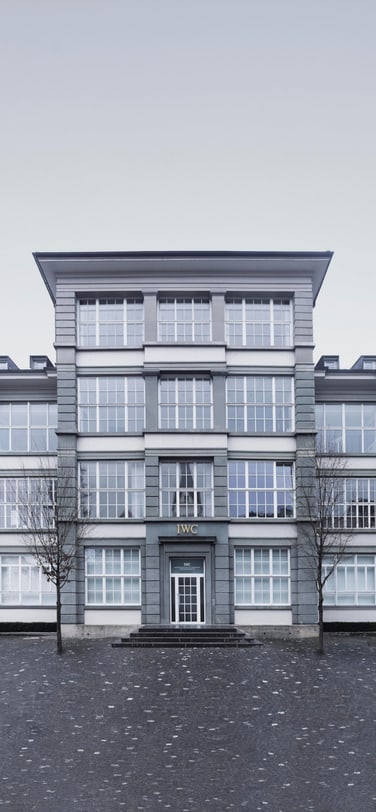
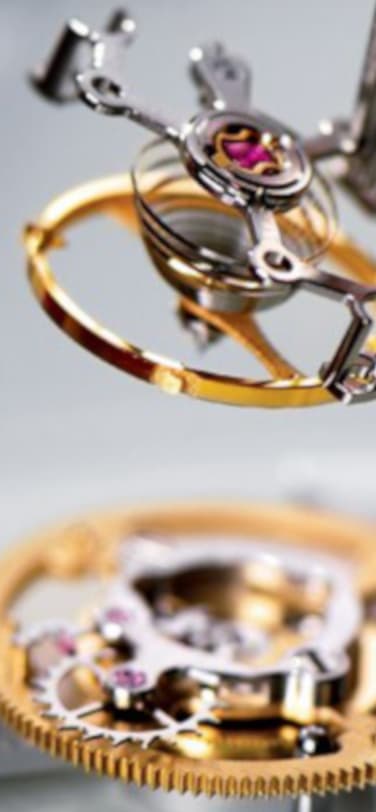
IWC-Philosophie
Die allermeisten Uhrenmanufakturen der Schweiz sind im französischsprachigen Teil des Landes ansässig, sodass Schaffhausen als Eiland in der Uhrmacherindustrie betrachtet werden kann. Seit der Gründung 1868 prägt der ungewöhnliche Standort die Unternehmensphilosophie. Mit klarer Ausrichtung auf Technologie und Entwicklung stellt IWC in ihrer Manufaktur am Ufer des Rheins präzise Zeitmesser von bleibendem Wert her. Mit ihrer Leidenschaft für innovative Lösungen und technischen Erfindergeist hat sich IWC Schaffhausen international einen Namen gemacht. Als eine der weltweit führenden Marken im Luxusuhrensegment erschafft IWC Meisterwerke der Haute Horlogerie, die Engineering und Präzision mit exklusivem Design vereinen. Die Reputation der Schaffhauser Marke beruht nicht zuletzt auf der Tatsache, dass ihre hoch qualifizierten Mitarbeiter jeden einzelnen Schritt in der Fertigung von Manufakturkalibern und Komplikationen wie der Minutenrepetition, dem Tourbillon und dem ewigen Kalender beherrschen. Für die Konstrukteure und Designer bedeutet das seit 1903 geprägte Qualitätsversprechen «Probus Scafusia» – «Bewährtes aus Schaffhausen» – nicht nur eine gewaltige Herausforderung, sondern ist auch Ausdruck ihrer grossen Leidenschaft.
Development
Bevor eine IWC-uhr zum ersten mal tickt
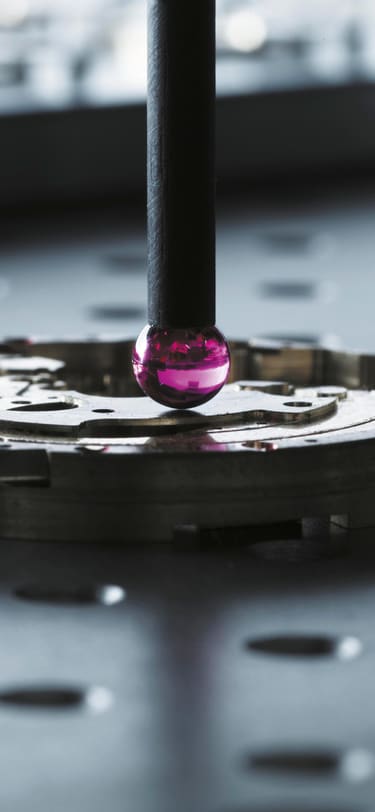
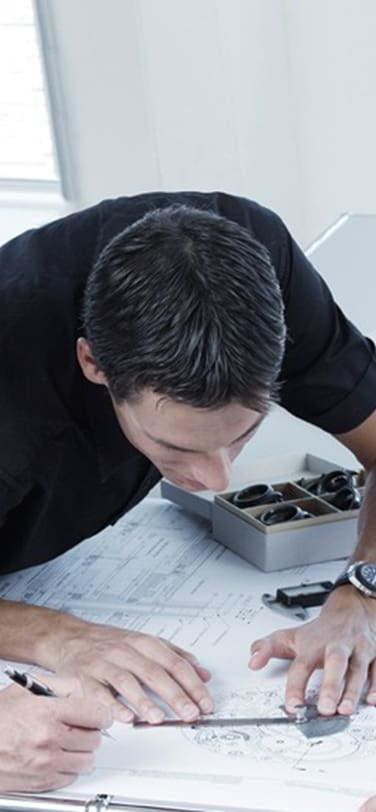
Konstruktion und Design
Wenn IWC mit der Entwicklung eines neuen Modells beginnt, stellen sich unsere Experten für Design und Konstruktion folgende Fragen: Was genau wollen wir erreichen? Soll die Uhr neue Massstäbe in puncto Kompliziertheit setzen? Liegt ihre Stärke in der Gangreserve oder doch eher in der Wasserdichtheit? Anschliessend werden mit Hilfe der rechnerunterstützten Konstruktion die ersten Komponenten entworfen. Hierbei misst IWC der Integration von Konstruktion und Design mit modernen Fertigungstechniken eine hohe Wichtigkeit bei. In enger Zusammenarbeit mit unseren Konstrukteuren tragen die Uhrendesigner entscheidend dazu bei, Form und Funktion bestmöglich miteinander in Einklang zu bringen. Das Zifferblatt und das Leder- oder Metallarmband, die Position der Anzeigen, die Wahl der Materialien und Farben sowie die Oberflächenbehandlung ergeben sich allesamt logisch aus konstruktiver Teamarbeit. Neben technischer Leistung und überzeugendem Design spielen auch weitere, emotionale Aspekte eine wichtige Rolle – etwa das Empfinden beim Berühren einer Uhr. So ist es kein Zufall, wie sich die Kante eines Gehäuses anfühlt, wie sich ein Drücker bedienen lässt oder wie es klingt, wenn die Krone einrastet. Oft lassen sich die Konstrukteure und Designer von alten Skizzen und Zeichnungen inspirieren. Denn nicht zuletzt ist es der Respekt für die Uhrmacherpioniere der Vergangenheit, der die Kontinuität der Schaffhauser Manufaktur garantiert.
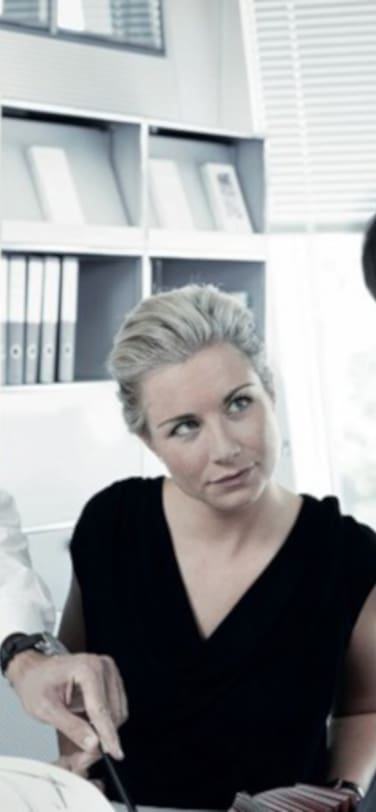
Qualitätsmanagement
Dank eines ausgereiften Entwicklungs- und Qualitätsmanagements sowie eines anspruchsvollen Test- und Prüfprogramms kann IWC höchste Qualität garantieren. Die modernen wissenschaftlichen Methoden, die dabei zum Einsatz kommen, umfassen tiefendimensional gestaltete Computersimulationen, Röntgenanalysen von Materialien sowie Praxistests unter extremen Bedingungen. Mit Highspeed-Kameras und Lasermessgeräten werden noch so kleine Bewegungen sichtbar gemacht. Eine ausgefeilte Software errechnet genaue Belastungsprofile.
Details wie Räder, Wellen, Zahnprofile oder die Dimension von Federn werden bereits in der frühesten Entwicklungsphase auf potenzielle Fehlerquellen untersucht. Bei IWC wird dieses Verfahren als «Fehlermöglichkeits- und Einflussanalyse» (FMEA) bezeichnet. Die Entwickler greifen auf ihre Erfahrungen aus früheren Projekten, auf Feedback vom Markt sowie auf Vorschläge, wie Uhren noch wartungsfreundlicher konstruiert werden könnten, zurück. So stellen sie sicher, dass eine IWC-Uhr auch in vielen Jahren noch funktioniert und repariert werden kann.
Tests
Der harte weg vom prototyp bis zur fertigen uhr
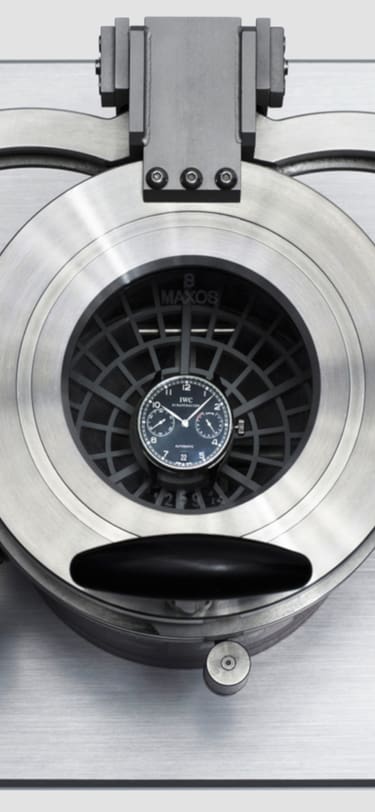
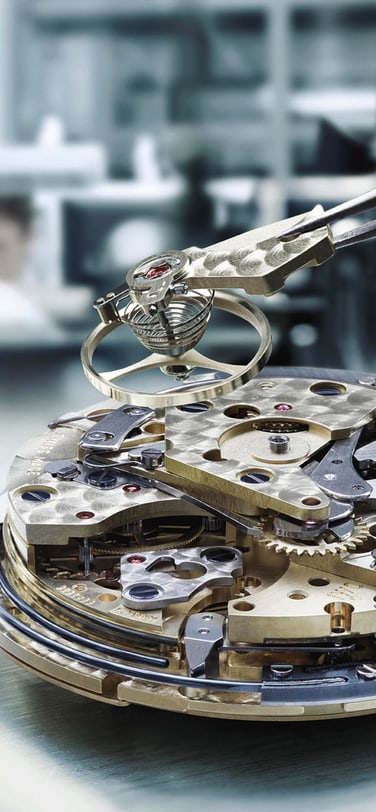
Qualifizierung und Homologisierung
Qualifizierung bezeichnet ein Programm von rund dreissig anspruchsvollen Tests über mehrere Monate hinweg, die für neue Uhren in der Prototypenphase oder später im Rahmen der Homologisierung der Nullserie konzipiert wurden. Die Tests simulieren in kondensierter Form praktisch alles, was einer Uhr im Laufe ihrer Lebenszeit unter normalen und extremen Bedingungen widerfahren kann. Erst wenn mehrere Prototypen strenge Tests bestanden haben und bei der Nullserie keine weiteren Probleme mehr auftauchen, ist die Serientauglichkeit erreicht – und der legendären Geschichte von IWC kann ein weiteres faszinierendes Kapitel hinzugefügt werden.
Korrosions- und UV-tests
Im Rahmen eines zweiwöchigen Salzbadtests bei 37 Grad Celsius werden Materialien aussortiert, die durch tägliches Tragen oder in Salzwasser korrodieren. Zifferblätter werden tagelang starkem UV-Licht ausgesetzt und dürfen dabei keine farblichen Veränderungen aufweisen.
Verschleisstest
Zu Testzwecken werden einzelne Teile bereits in der Konstruktionsphase produziert, um die Mindestanforderungen für Komponenten zu prüfen, die normalerweise einem hohen Verschleiss ausgesetzt sind. Die Drehlünette der Aquatimer etwa wird einem Dauertest unterzogen, der vier Tauchgänge pro Tag simuliert, um eine Mindestlebensdauer von zehn Jahren zu garantieren. Die Drehlünetten der IWC-Taucheruhren müssen ihre Zuverlässigkeit zudem in schmutzigem Wasser unter Beweis stellen. Auf dem Kronen- und Drückerprüfstand werden Chronographendrücker 10 000 bzw. 20 000 Mal betätigt, um ihre Verschleissfestigkeit zu testen.
Klimatests
Mit dem Klimatest kann das gesamte Spektrum an klimatischen Bedingungen, die einer Uhr ausgesetzt sein kann, systematisch getestet werden. Geografisch gesprochen umfasst dieser Test alle Klimazonen von Alaska über die Sahara bis zum brasilianischen Regenwald. Die Uhren werden in einen Klimaschrank gelegt und dort über einen Zeitraum von mehreren Tagen und mitunter Wochen Temperaturwechseln von –20 bis +70 Grad Celsius und einer relativen Luftfeuchtigkeit von 95 Prozent ausgesetzt. Nach diesem Härtetest steht ein Langzeitgangtest auf dem Programm. Mit Hilfe eines automatischen Mehrlagenmikrofons wird bei diesem Test die Regelmässigkeit des Gangs geprüft.
Assemblage
Hightech und handarbeit sind bei IWC keine gegensätze
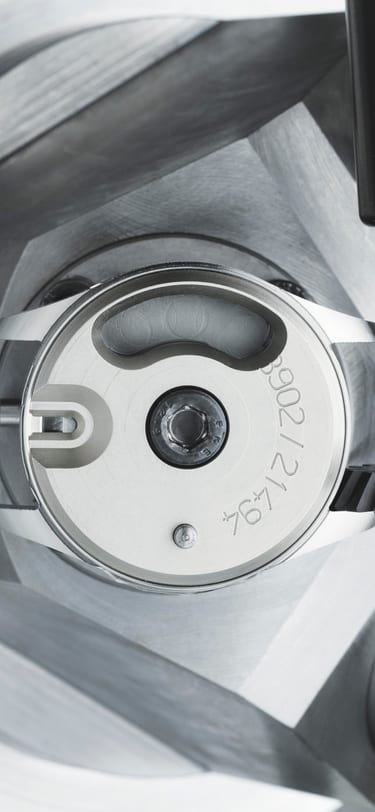
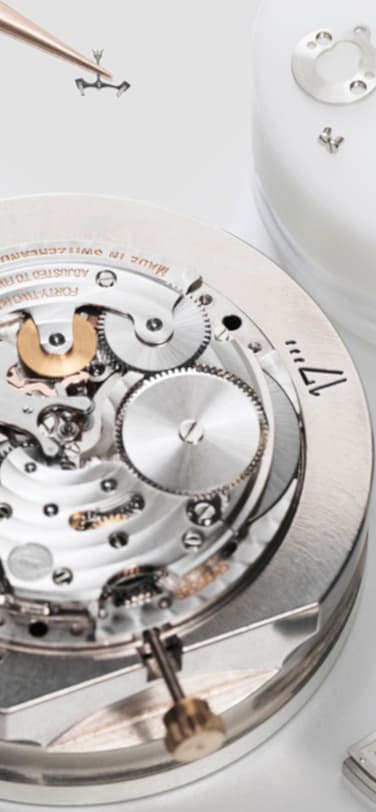
Produktionstechniken
Während der Teileproduktion werden mit Hilfe von CNC-gesteuerten Fräsmaschinen Rohlinge gefertigt. Nach der Oberflächenbearbeitung beträgt die Toleranz bei Werkteilen allgemein nur ±0,02 Millimeter, in speziellen Fällen sogar nur ±0,002 Millimeter. Nach der Bearbeitung gehen die Teile zum Handarbeitsplatz oder kommen auf die Erodiermaschine. Die CNC-Drahterodiermaschinen werden vorwiegend für die Fertigung von Teilen im Uhrwerk eingesetzt. Die erreichte Oberflächenrauheit beträgt 0,005 Millimeter, beim Feinerodieren bis zu 0,001 Millimeter.
Assemblage des Uhrwerks
Die Assemblage des Uhrwerks umfasst die Verbindung von Aufzug, Räderwerk und Hemmung. Anschliessend erfolgt die Réglage oder Feinjustierung. Je nach Modell können hier auch der Automatikaufzug und Chronograph sowie der Kalender- und Stundenzählmechanismus involviert sein. Die komplexeste dieser Aufgaben ist die Einstellung der Hemmung und die Anpassung der Spiralfeder für einen perfekten Rund- und Flachlauf: Diese feinste Handarbeit könnte von einer Maschine nicht einmal annähernd so präzise und hochwertig ausgeführt werden. Funktionen und Feinjustierungen werden kontinuierlich in jeder Phase der Assemblage geprüft und ggf. korrigiert. In der Komplikationenabteilung ergänzen hoch qualifizierte Uhrmacher die Grundwerke mit Komplikationen wie dem ewigen Kalender oder dem Rattrapante-Mechanismus. In der Spezialitätenabteilung werden Uhrwerke mit Tourbillon und Minutenrepetition von A bis Z aufgebaut: Sie durchlaufen die Arbeitsschritte Vormontage und Montage sowie alle Feineinstellungen und das Einschalen ins Gehäuse.
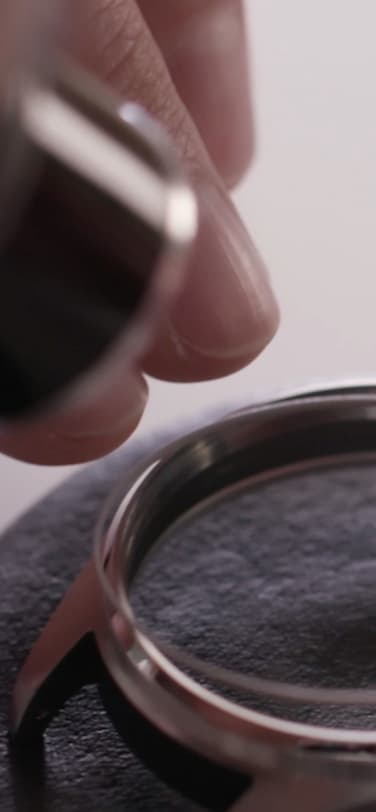
Gehäusefertigung und -montage
In puncto Präzision und Aufwand steht die Gehäusefertigung den anderen Fertigungsstufen in nichts nach. Bei Uhren aus Edelmetall werden die Gehäuseteile aus vorgeformten Rohlingen gefertigt. Gehäuse aus Edelstahl und Titan werden aus eigens für IWC hergestellten Stangen gefertigt, die auf CNC-gesteuerten Dreh- und Fräsmaschinen weiterverarbeitet werden – auf einen Hundertstelmillimeter genau. Auf den Fräszentren werden die Bandanstösse sowie Kronen- und Drückerbohrungen in die Werkringe gefräst und komplexe Freiformflächen hergestellt, z. B. die an den Gehäusen der Ingenieur-Uhren. Nach der spanabhebenden Bearbeitung wird die Masse akribisch geprüft, und die Oberflächen werden in präziser Handarbeit auf IWC-Standard gebracht. Die Kanten werden entgratet und gerundet, oder es wird facettiert. Dreh-, Fräs- und Bearbeitungsspuren werden beseitigt, die Oberflächen feingeschliffen, poliert, satiniert und gestrahlt. An manchen Gehäuseteilen gestalten Spezialisten verzierte Oberflächen wie z. B. eine Perlage – und das sogar an Stellen, die von aussen nicht sichtbar sind. Aufwendige Tests, beispielsweise zur Wasserdichtheit des Gehäuses, sowie Aspektkontrollen schliessen die Fertigung des Gehäuses ab.
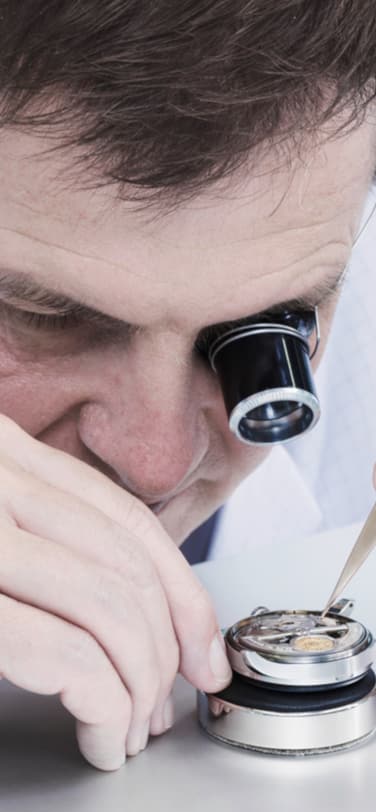
Zifferblatt, Zeiger und Werkeinbau
In diesen Abteilungen werden alle Arbeiten von Hand ausgeführt. Spezialisten montieren die Zifferblätter je nach Modell von Hand oder mit Hilfswerkzeugen auf das fertig regulierte Werk. Das Gleiche gilt für die Zeiger, die exakt auf die richtige Höhe gesetzt werden und fest auf der Zeigerwelle halten müssen. Bei Chronographen muss zudem die Nullstellung der Zählzeiger absolut präzise sein. Das Werk wird entweder an einem Werkring oder direkt im Gehäuse befestigt. Bei Verwendung eines Werkrings wird dieser von einer Wellenfeder gehalten, die im Gehäuseboden platziert ist. Die Aufzugswellen werden individuell angepasst. Ein spezieller Klebstoff sichert die auf die Aufzugswelle geschraubten Kronen.
Endkontrolle
Über einen Zeitraum von zehn Tagen werden bei Uhren mit automatischem Aufzug die Uhrwerke ständig bewegt und die Uhren mit Handaufzug jeden zweiten Tag aufgezogen. Durch den Gebrauch können sich die Räder und Triebe perfekt aufeinander einstellen, und die Schmierung kann bis zu den vorgesehenen Stellen vordringen.
Die Qualitätssicherung schliesst mit einer umfangreichen Endkontrolle ab. Durch vollständiges Aufziehen des Uhrwerks, Messung der Ganggenauigkeit, Prüfung der Funktionen und der optischen Merkmale sowie Bestätigung der Luft- und Wasserdichtheit wird die Uhr ein letztes Mal auf Alltagstauglichkeit getestet. Jedes Produkt, das die Schweizer Manufaktur am Rhein verlässt, ist zweifelsohne von höchster Qualität. Die lückenlose Qualitätssicherung garantiert dem zukünftigen Besitzer einer IWC-Uhr, dass das Unternehmen seine legendären Qualitätsversprechen rigoros hält.
Personalisierung
Eine gravur macht ihre IWC-uhr zum unikat
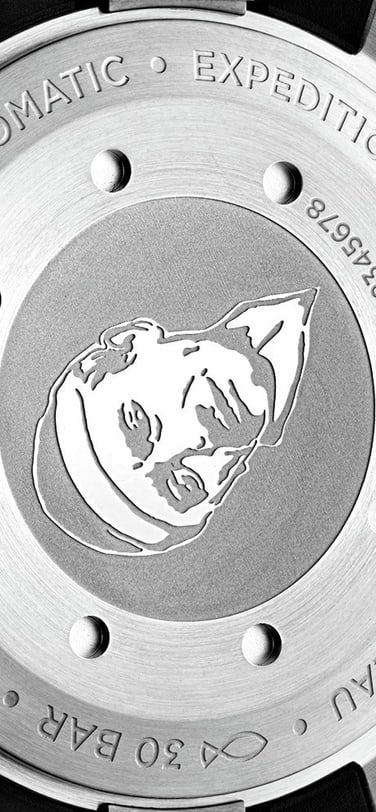
Jede Uhr aus dem Hause IWC hat ihre ganz eigene Persönlichkeit. Häufig wünscht sich ein Kunde jedoch noch das gewisse Extra und bittet uns, seiner Taschen- oder Armbanduhr noch mehr Individualität zu verleihen.
Dank moderner Gravurtechniken bietet IWC nahezu unbegrenzte Möglichkeiten. Praktisch jeder Anfrage nach bestimmten Änderungen zur Personalisierung einer Uhr können wir uneingeschränkt nachkommen. «Gravieren» stammt vom französischen Wort «graver» und bedeutet ursprünglich «eine Furche ziehen».
Durch das Einritzen von Zeichnungen, Mustern, Verzierungen oder Schrift in Holz, Stein, Elfenbein und Metall werden reizvolle Licht- und Schatteneffekte erzielt, die ganz persönliche Vorstellungen zur Geltung bringen.
Auf diese Weise entstehen auf kleinstem Raum Wunderwerke für die Ewigkeit, wie z. B. die Bodengravur der Aquatimer Chronograph Edition «Expedition Jacques-Yves Cousteau» oder der Ingenieur Chronograph Silberpfeil. So wird aus einer IWC-Uhr durch die Gravur von Initialen, eines Datums, Familienwappens, Firmenlogos oder einer persönlichen Widmung ein wertvolles Einzelstück – Individualität in Reinkultur.
Service
Eine IWC-uhr erfreut generationen
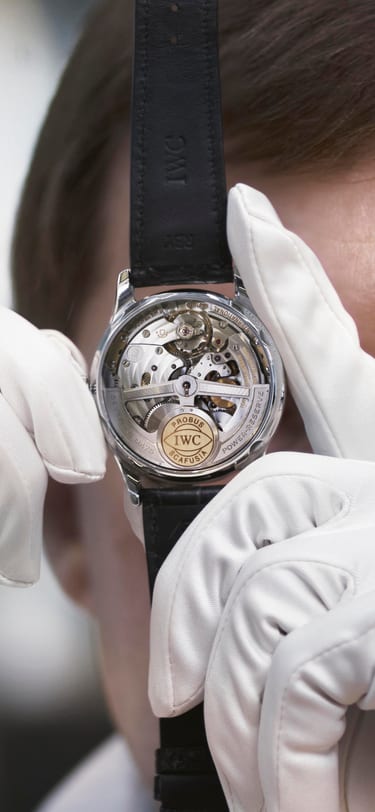
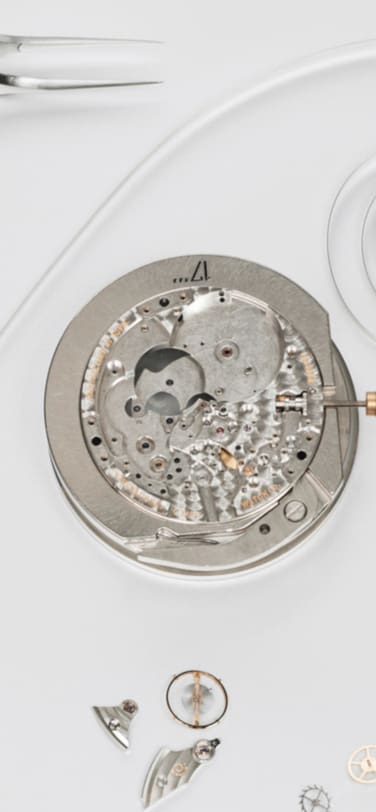
Pflege und Service
In 25 Ländern weltweit widmen sich mehr als zweihundert Uhrmacher und Servicetechniker der Wartung und Reparatur von IWC-Uhren jedes Jahrgangs seit Gründung des Unternehmens im Jahr 1868. Um sicherzustellen, dass kein einziges Detail verloren geht, führt IWC detaillierte Aufzeichnungen zu jeder Uhr, die das Werk seit 1885 verlassen hat.
Herzstück der Reparaturabteilung ist das Ersatzteillager. Hier lagern Millionen von fein säuberlich geordneten Kleinstteilen. Die Bereitstellung von Originalersatzteilen hat bei IWC hohe Priorität, denn nur so kann sichergestellt werden, dass die Uhr über Generationen hinweg erhalten bleibt. Der zeitliche Abstand zwischen einer solchen Wartung variiert zum Teil erheblich und hängt davon ab, wie und unter welchen Bedingungen die Uhr getragen wird.
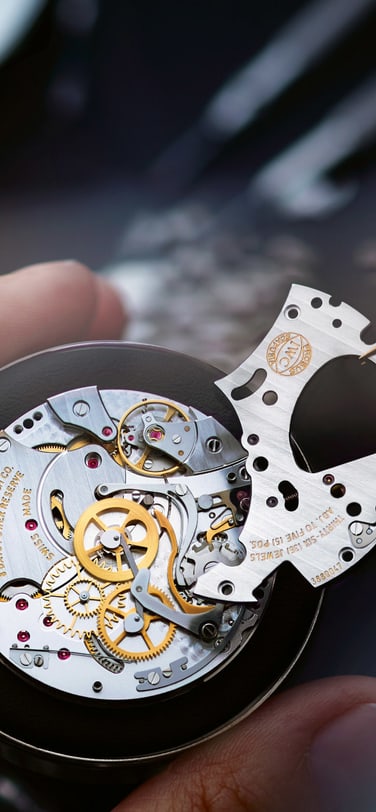
Der Grosse Service
Beim grossen Service wird das Uhrwerk komplett zerlegt, und die einzelnen Werkbestandteile werden gereinigt. Spezialisten kontrollieren jedes Werkteil akribisch und reparieren bzw. ersetzen verschlissene und defekte Teile. Anschliessend wird das Uhrwerk von Grund auf neu zusammengebaut und dabei immer wieder punktuell geölt und geschmiert.
Zum Schluss wird das Werk auf Ganggenauigkeit geprüft und neu reguliert. Auch das Gehäuse wird vollständig auseinandergenommen. Kratzer werden ausgebessert, Gehäuseteile und Bandkomponenten werden geschliffen oder lapidiert, poliert und am Ende gründlich gereinigt. Bevor die Uhr an den Kunden zurückgeschickt wird, durchläuft sie in der Endkontrolle ein mehrtägiges, intensives Prüfprogramm. Nur so können ein genauer Gang und die tadellose Wasserdichtheit des Zeitmessers über weitere Jahre hinweg gewährleistet werden.
Jeder Besitzer einer IWC-Uhr kann selbst dazu beitragen, die Langlebigkeit seiner Uhr zu erhöhen. Hinweise dazu finden sich auf der Website iwc.com und in der Servicebroschüre «Der IWC-Service». Letztere ist bei IWC-Boutiquen und IWC-Servicecentern sowie bei autorisierten Verkaufspartnern erhältlich.
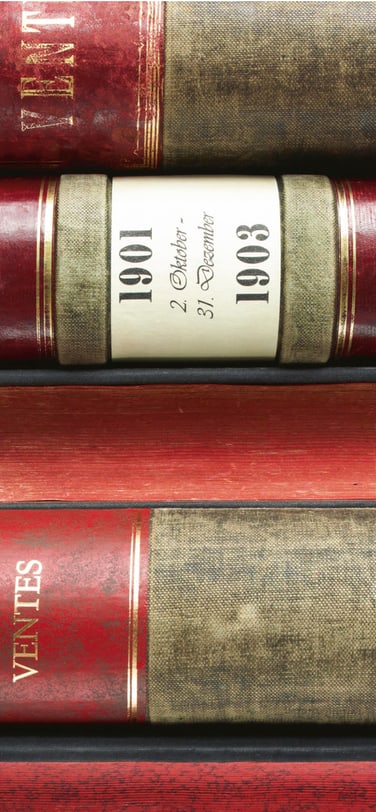
IWC-zertifikat
Die Geschichte jeder IWC-Uhr beginnt in der Manufaktur, wo sich passionierte Uhrmacher mit jedem Detail viele Stunden lang beschäftigen. Um diese Zeitmesser nie ganz aus den Augen zu verlieren, hat IWC 1885 damit begonnen, über sie Buch zu führen. Sämtliche Angaben wie Verkaufsdatum, Kaliber, Material und Gehäusenummer und bei neueren Modellen auch die Referenznummer werden notiert. Erben oder spätere Käufer haben daher die Möglichkeit, gegen einen Kostenbeitrag genaue Auskünfte über ihre IWC-Uhr zu erhalten und sich die Echtheit ihrer Uhr bestätigen zu lassen. Diese und weitere Informationen werden in Form eines Zertifikats ausgestellt.
Für die Zertifikatsausstellung ist es erforderlich, dass die Uhr in einer IWC-Boutique oder bei einem Fachhändler abgegeben wird. In unserer Manufaktur in Schaffhausen wird der IWC-Zeitmesser dann einer sorgfältigen und detaillierten Prüfung durch einen erfahrenen Uhrmacher unterzogen.
Leider ist es nicht möglich, Angaben über den Sammlerwert eines Modells zu machen, da dieser von Faktoren wie Angebot und Nachfrage sowie vom Zustand des Werks und des Gehäuses abhängt.
Sollte einmal der tragische Fall eintreten, dass eine IWC-Uhr gestohlen wird oder verloren geht, ist es ratsam, den Verlust bei der Polizei und bei IWC schriftlich zu melden. Die betreffende Gehäuse- oder Referenznummer wird dann in einem speziellen Register festgehalten, damit die Uhr erkannt wird, falls sie in einem IWC-Servicecenter auftaucht. Dank dieser Registrierung konnten schon oft vermisste Uhren an ihre rechtmässigen Eigentümer zurückgegeben werden.