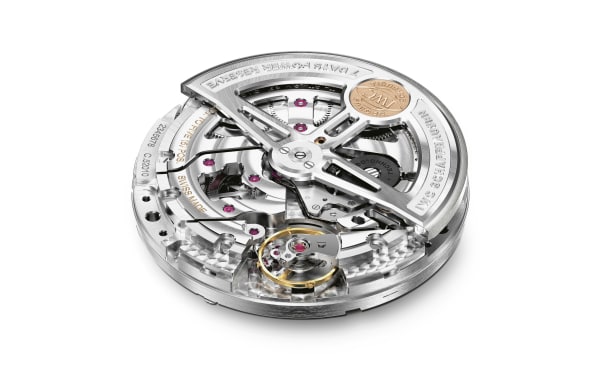

ARTÍCULOS
A Matter of Adjustment
Condiciones de envío y entrega
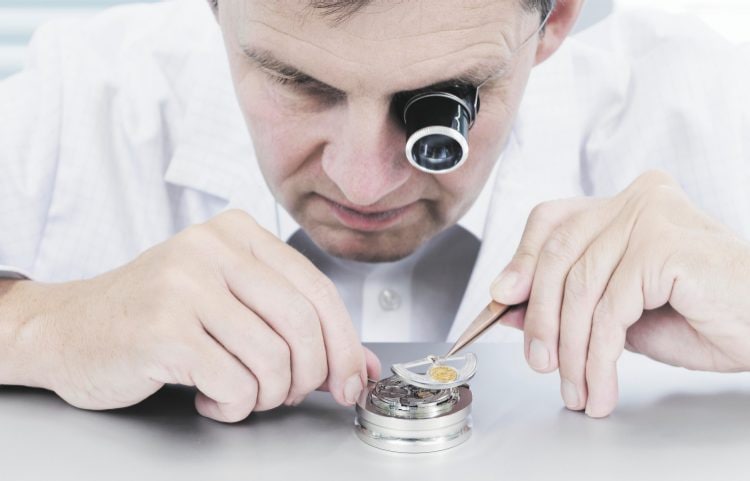
For an IWC watch to run accurately, the oscillations of the balance require careful adjustment. Constructing the oscillating system, assembling the movement and making precise settings calls for the input of dozens of experienced specialists. Apart from skill and patience, manually adjusting a watch requires a wide-ranging knowledge of possible sources of error and the energy flows within the movement.
Someone who buys an IWC expects to get an elegant, extremely accurate timepiece. “If a mechanical watch is to show the correct time reliably, its balance must oscillate at a precise, even rate,” explains Christoph Bühler, Head of Timing at IWC.
In a movement with a frequency of 4 hertz, the ring-shaped “pendulum” – in a watch the balance wheel – completes eight beats, or vibrations, per second. The escapement releases the wheel train at the correct intervals and advances the seconds hand by precisely one mark on the dial.
Although this may sound simple, it is extremely complicated in practice. Mechanical watches are delicate mechanisms with hundreds of individual parts in constant motion. In order to achieve the desired accuracy in all positions, the oscillations of the balance require careful adjustment by hand. Réglage, or adjustment, is a process involving several stages in which specialists from various departments edge their way gradually towards maximum precision.
In order to achieve the desired accuracy in all positions, the oscillations of the balance require careful adjustment by hand
All the parts must fit precisely
The first stage in the process is the inspection and assembly of the oscillating system, for which the timers are responsible. Their job calls for extremely well-developed fine motor skills. It is vital that all the parts match perfectly. The balance spring should be two-thirds of the diameter of the balance rim and have 14 to 16 coils. The rim itself is tested for true running using a set of figure-of-eight callipers. As on a bicycle wheel, even a small dent would negatively affect the rate. The timer also checks the balance staff pivots to see that they run in the bearings with a minimum of frictional loss. He also ensures that the balance spring is centred and running flat. Only then can optimum oscillation be guaranteed at a later stage.
— Mechanical watches are delicate mechanisms with hundreds of individual parts
Bending the Breguet spring by hand
The trickiest part of the entire process is the bending of the balance spring. Using a principle developed by Abraham-Louis Breguet over 200 years ago, the outer coil is bent up and over the volute, or flat part of the spring. When vibrating, the spring expands evenly and increases the movement’s accuracy. To this day at IWC, Breguet springs are bent by hand. “Although special forming tools ensure more consistent quality, the job requires a lot of dexterity,” says Bühler. After bending the final coil, the balance fitter wedges the outer end with a conical stud on the balance spring and connects the spring through this to the balance cock.
Renewing the entire balance assembly in an old watch is particularly labour-intensive. When an 854 calibre arrives in Schaffhausen for an overhaul, the skilled hands of a timer like Annelies Bürki are called for. With over 40 years’ experience, she can bend the specially shaped springs from old calibres without the help of a diagram. Depending on the state of the escapement, she may need to replace the balance staff and roller with the impulse pin, polish the pivots and carefully poise the balance rim. Apart from counting, setting, bending and finally attaching the stud to the balance spring, the work involved here may well take several hours.
During assembly, the watchmaker integrates the balance and spring into the movement and makes the basic adjustment. During a ten-day running-in period, the oils and lubricants are distributed throughout the movement and the parts begin to mesh smoothly. After more modifications, the watch progresses to the precision adjustment stage. Here, 20 watchmakers focus on further increasing the accuracy of the mechanism until they meeting the strict tolerances required. “Over a period of 24 hours, an in-house movement that leaves our workshops may gain up to six seconds but must never lose time,” says Kai Stiewe, Head of Precision Adjustment at IWC.
The timing machine supplies vital data
In order to make a precise adjustment, the watchmaker requires exact details about the rate. In the past, movements would spend hours being measured against a reference clock and any deviations noted. Today, timing machines use a contact microphone to record the sounds generated by the balance and spring, such as that of the impulse pin making contact with the pallet lever. This way, any deviation in the rate or the amplitude of the balance can be identified within minutes. Modern timing machines measure these parameters with the watch in six different positions: with the dial up and down, and with the crown to the right, left, up and down. “We can’t possibly make allowance for every aspect of the owner’s habits, but we do obtain data that helps with our adjustments,” say Stiewe, explaining the advantages of this method.
If there is a rate error, the balance vibrates too quickly or too slowly, and the watch is either fast or slow. The required correction can be made either by adjusting the effective length of the balance spring or the moment of inertia in the balance rim. In IWC’s 98000 calibres, the active length of the spring is adjusted using the index, which is attached to the balance spring by two tiny pins. Moving the index in one direction or the other causes the balance to vibrate faster or more slowly. Other IWC calibre families feature an indexless balance. Their frequency is adjusted using four weight screws on the balance rim. Screwing them outwards causes the vibrations to slow. Screwing them inward speeds up the rim. “Depending on the position of a rating error, a specialist knows where and what to turn,” says Stiewe.
— IWC’s 98000 calibres
— IWC watchmaker at work
The amplitude requires fine adjustment
Often, an error in the amplitude requires correction. When it is too high, the balance oscillates beyond the ideal limit, indicating that too much energy is being transmitted from the wheel train. This may have a negative impact on the watch’s accuracy. If this is the case, the pallet stones need to be pushed outwards slightly. As a result, the friction between escape wheel and pallets is increased, which leads to a loss of energy and a reduction in amplitude. Allowance must also be made for the fact that the dimensions of the pallet lever and the escape wheel, as well as the distance between the teeth, differ slightly from one calibre to another. Any or all of these factors may influence the amplitude, which explains the individual nature of the necessary adjustments.
If, on the other hand, the amplitude is too low, energy is being lost somewhere. In such cases, the watchmaker will carefully trace the flow of energy from the barrel to the balance. He checks that all the necessary points in the wheel train are lubricated and that the endshake is correct. The interplay between escapement and balance also deserves particular attention. Only if this is correct can the pallet lever provide the balance with the regular supply of energy it requires through the impulse pin.
At the precision adjustment stage, the beat is also measured. A beat error exists when it takes too long for the balance to start moving after the watch is wound. To counteract this, the watchmaker changes the point at which the balance spring sticks on the balance cock and positions the impulse pin centrally in the pallet fork. “Thanks to the fact that the watch is now in beat, it will run without any delay even when the mainspring is not fully wound,” explains Stiewe.
“Setting and adjusting a watch is often a test of patience.”
— Christoph Bühler, Head of Timing at IWC
Mentally syncing with the wheel train
Both Bühler and Stiewe believe that the main requirement for high-level precision is the experience of the watchmakers and timers. Precision adjustment in particular calls for an all-round knowledge of possible sources of error as well as a fundamental understanding of energy flows. Often, the ability to identify with the movement and go with the flow of the wheel train leads to an optimum adjustment. “Setting and adjusting a watch is often a test of patience, but when an IWC is ultimately running with absolute precision, everyone who has been involved is extremely proud,” say Bühler in summary.
— The main requirement for high-level precision is the experience of the watchmakers